In the world of industrial machinery, the efficiency and longevity of equipment are paramount, particularly in systems where high pressure and high temperatures are involved.
One critical component in such machinery is the high pressure shaft seal. These seals are indispensable in turbines, compressors, pumps, and other high-performance equipment, where preventing leakage of fluids is crucial for operational integrity and safety.
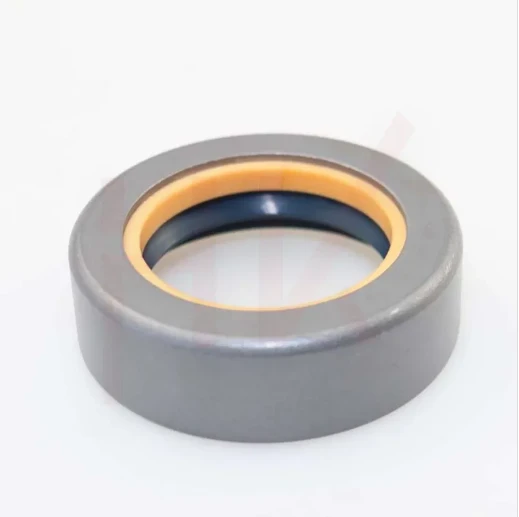
High pressure shaft seals, crafted to withstand extreme conditions, function as the first line of defense against leakage. Their design involves robust materials and intricate engineering to ensure they can endure the pressure without compromising the performance of the entire system. An expertly designed seal not only prevents fluid leakage but also reduces the risk of contamination and minimizes maintenance downtime, ultimately leading to cost savings and improved efficiency.
The engineering behind high pressure shaft seals can be likened to a symphony of physics and material science. Engineers often choose materials that can resist the harsh environments these seals must endure. For instance, seals made from synthetic rubber compounds are popular due to their excellent elasticity, chemical resistance, and temperature resilience. Advanced seals may incorporate metal components and specialized coatings to further enhance their durability and performance.
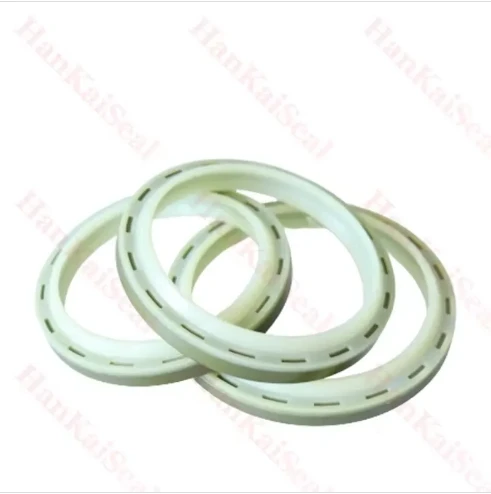
One notable aspect of high pressure shaft seals is their customization potential. Each industrial application can present unique challenges, from varying pressures and temperatures to differing fluid types. Customizing seals to match specific operational requirements is where expert knowledge in seal design and material science becomes invaluable. By understanding the unique demands of each system, engineers can tailor seals to provide optimal performance, ensuring seamless operations and prolonged equipment life.
high pressure shaft seals
Developments in technology have ushered in innovative manufacturing techniques for high pressure shaft seals. Techniques such as injection molding and precision machining allow for complex geometries and tighter tolerances, directly translating to better performance under pressure. Furthermore, advancements in computer-aided design (CAD) enable engineers to simulate various operational scenarios, allowing for virtual testing and refinement of seal designs before they are manufactured.
From an expertise standpoint, selecting the right high pressure shaft seal involves considering factors such as axial and radial loads, temperature gradients, and fluid composition. In high-stakes environments where operational failure can lead to substantial economic or environmental impacts, the importance of expert consultation cannot be overstated. Companies that invest in expert advice and high-quality seals often find significant returns in reliability and performance.
Gaining trust in seal performance also relies on rigorous testing standards. Reputable manufacturers subject their seals to comprehensive testing protocols, often exceeding industry standards. These tests, which may mimic real-world operational stresses, ensure that the seals will perform consistently under the toughest conditions. Certifications from recognized entities further enhance the credibility of seal manufacturers, providing customers with assurance that their equipment is protected by components of the highest caliber.
In summary, high pressure shaft seals are an integral part of high-performance machinery, blending sophisticated design with cutting-edge materials and technology. Their role extends beyond mere fluid containment, contributing to the efficiency and reliability of entire systems. By leveraging expertise, embracing innovation, and adhering to stringent standards, manufacturers of these seals continue to solidify their authority and trustworthiness in the industrial sector, ensuring that businesses operate smoothly and without unnecessary disruptions.