In the world of industrial machinery and automotive engineering, the high pressure oil seal stands as an unsung hero, ensuring the flawless operation of complex systems. These seals are meticulously engineered components that play a critical role in preventing fluid leaks and maintaining the pressure balance within machinery, making them indispensable in high-performance environments.
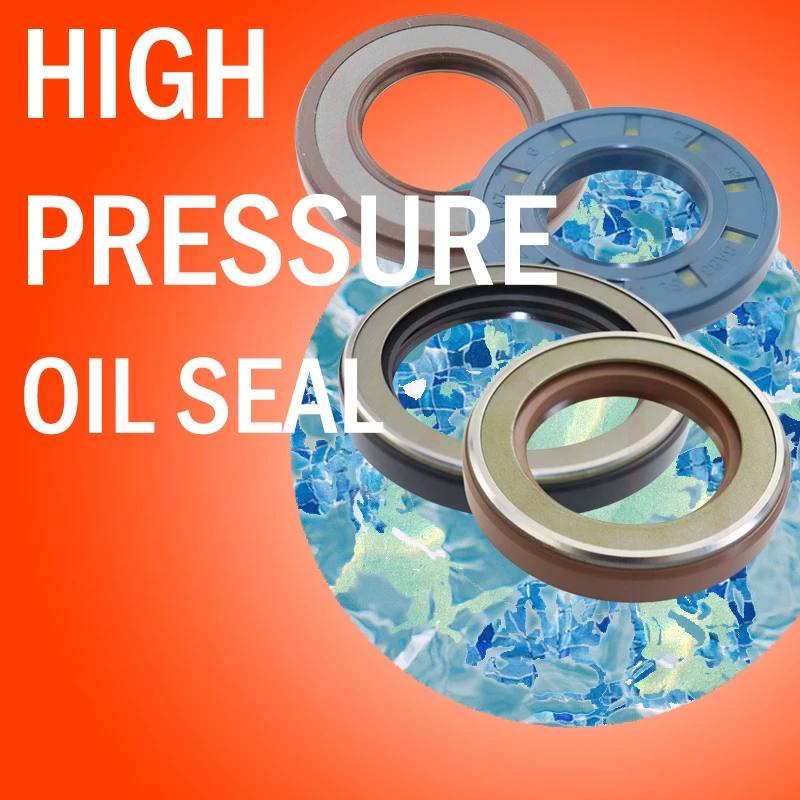
High pressure oil seals are designed to meet rigorous demands in industries where pressure and contamination are principal concerns. Industries such as automotive, aerospace, oil and gas, and manufacturing rely heavily on these components to ensure efficiency and reliability. In these settings, equipment undergoes extreme conditions, including high rotational speeds and operating temperatures, making the role of oil seals paramount in safeguarding against premature machinery failure and costly downtime.
Cutting-edge technology and materials science are at the forefront of developing these seals. High pressure oil seals are crafted from advanced elastomers and polymers capable of withstanding incredible pressure differentials and resisting wear and tear over extended periods. Fluorocarbon elastomers, for example, are commonly used due to their ability to resist heat, oil, and chemical degradation. These materials ensure that seals maintain their integrity, even in harsh environments, thereby guaranteeing a longer service life and fewer replacements.
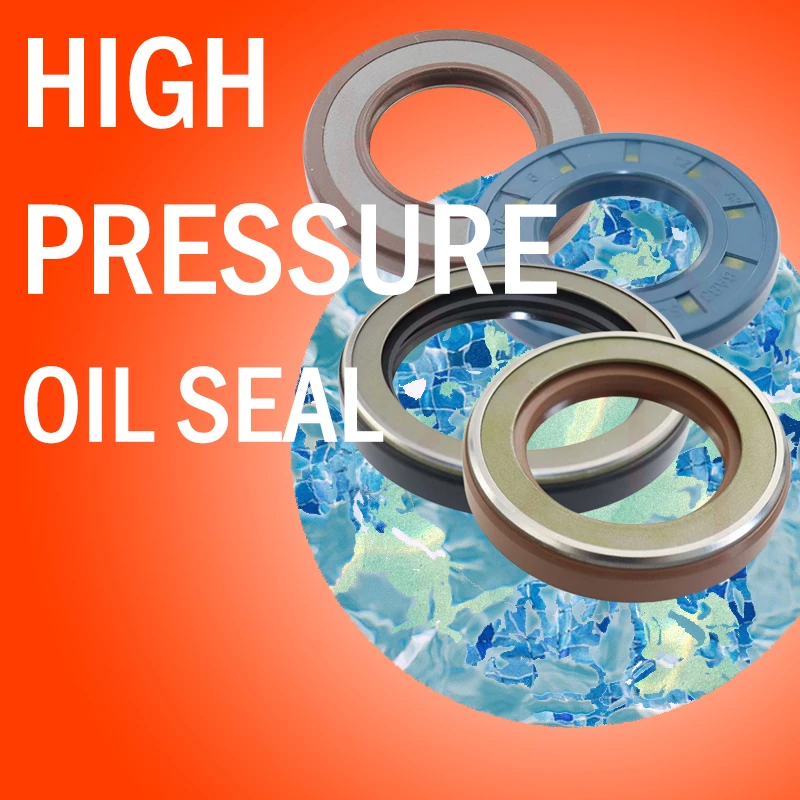
From an engineering perspective, the efficacy of high pressure oil seals lies in their intricate design, which must accommodate the specific requirements of each application. This includes factors such as shaft diameter,
fluid pressure, and environmental conditions. Customization is often essential, allowing for tailored solutions that enhance the seal's efficiency and performance. Furthermore, expert installation is necessary to prevent mechanical damage and ensure seamless operation.
high pressure oil seal
Brands producing high pressure oil seals leverage decades of experience and expertise to provide products that not only meet international standards but also exceed customer expectations. Their reputation for quality and reliability is built on a foundation of rigorous testing and continuous innovation. Users can trust that these seals will exhibit exceptional durability and efficiency in high-pressure applications, enabling optimum equipment performance.
Maintaining trustworthiness in the use of high pressure oil seals involves regular inspection and maintenance, an area where informed users must be diligent. This includes periodic checks for signs of wear and degradation, such as cracking, hardening, or unusual fluid leakage. Keeping abreast of the manufacturer's guidelines and maintenance schedules ensures the seals' longevity and the continued performance of the machinery they protect.
The importance of selecting the right high pressure oil seal cannot be overstated. Making informed decisions based on the specific application needs and consulting with experts ensures that the correct seals are chosen, minimizing the risk of machine failure and maximizing productivity. Trust in the reliability of these components is essential for industries that cannot afford interruptions, serving as a testament to their indispensable role in today's technologically driven environment.
Incorporating high pressure oil seals into industry-standard practices highlights their unparalleled expertise, reliability, and vital presence, ensuring machinery operates smoothly, safely, and efficiently under even the most challenging conditions.