For industries that rely on machinery, the proper functioning of equipment is crucial for maintaining productivity and minimizing downtime. One often-overlooked component that plays a significant role in this process is the oil seal. Custom-made oil seals have risen in prominence due to their ability to cater to specific industrial needs, ensuring reliability and longevity in applications ranging from automotive to aeronautics.
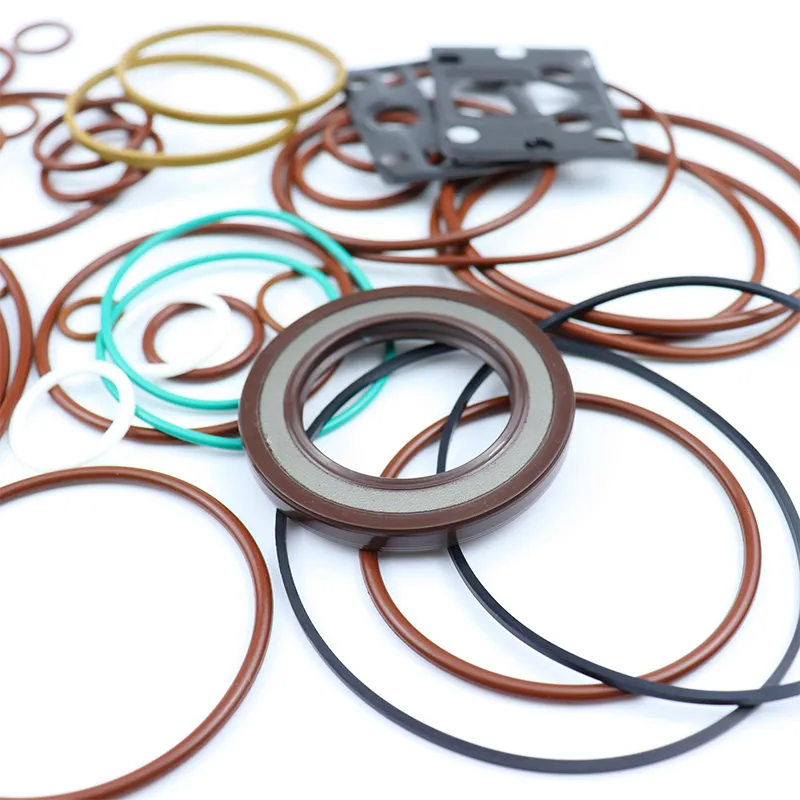
Oil seals, also known as rotary shaft seals, perform the essential task of preventing lubricant leakage and blocking contaminants from entering crucial machinery parts. When off-the-shelf seals fail to meet the demanding requirements of specialized applications, custom-made options provide a viable solution. Their design can be tailored to fit specific dimensional and material needs, and this customization can vastly enhance the effectiveness of seals in unique operating environments.
Industries with challenging conditions—such as those involving extreme temperatures, high pressures, or exposure to aggressive chemicals—benefit significantly from custom-made oil seals. For example, in the automotive sector, bespoke oil seals ensure that engines operate smoothly despite variable thermal expansions. Engineers can choose materials that resist degradation, ensuring seals remain intact under pressure without the risk of cracking or warping. This level of detail in custom manufacturing can greatly extend the lifespan of machinery, offering a proactive approach to maintenance that standard seals simply cannot provide.
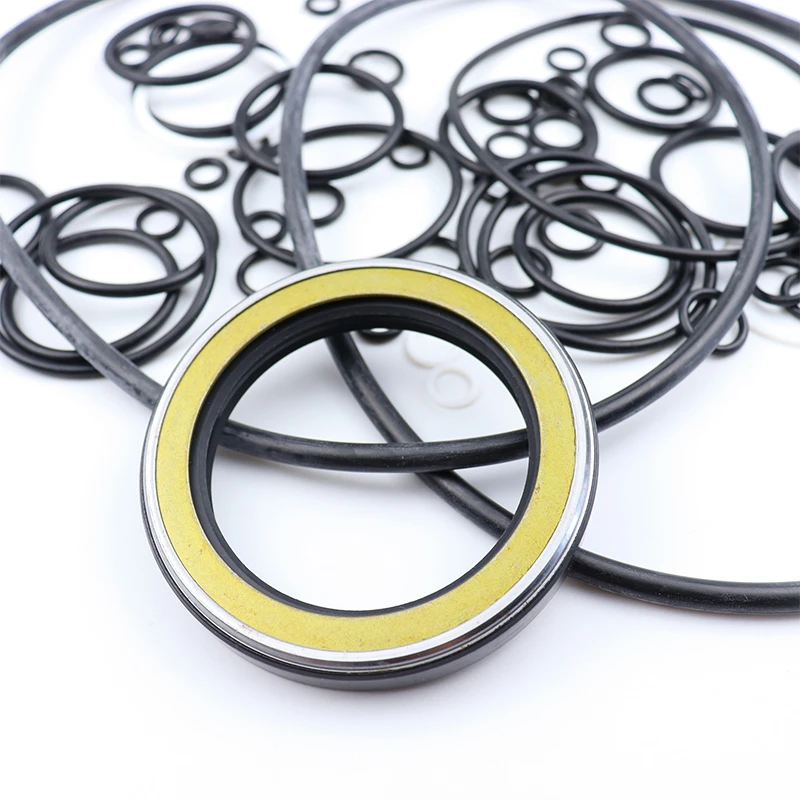
In manufacturing, the expertise required to design and produce custom-made oil seals involves close collaboration among engineers, materials scientists, and industrial designers. Such collaboration brings together an understanding of the physical and chemical properties needed for different applications, ensuring that every custom seal meets rigorous industry standards. This collaborative process also emphasizes experience; knowledge gleaned from hands-on work in specific industries allows for a nuanced approach to creating seals that meet both immediate and long-term operational needs.
custom made oil seals
Custom-made oil seals also stand as a testament to authoritativeness. Companies specializing in these products often hold various certifications, demonstrating compliance with international quality standards. This not only showcases their technical prowess but also provides customers with peace of mind regarding product reliability. Furthermore, these manufacturers usually offer extensive testing and quality assurance procedures, ensuring each seal meets high-performance benchmarks.
Trustworthiness is central to the relationship between custom seal manufacturers and their clients. A reputation built over years of successful project completion reinforces a manufacturer's credibility. By consistently delivering high-quality custom solutions tailored to client specifications, these companies cultivate long-term partnerships. Customers must ensure that they choose a manufacturer who is transparent about their processes, materials, and capabilities, as such transparency is a cornerstone of trust.
For businesses seeking to enhance equipment reliability, investing in custom-made oil seals is a wise decision. While the upfront costs may appear higher than standard seals, the long-term benefits—such as reduced maintenance costs, fewer operational stoppages, and enhanced equipment longevity—offer substantial economic advantages. As industries continue to evolve and face increasingly complex demands, the role of custom-made oil seals in safeguarding the seamless operation of machinery becomes ever more critical. Engaging with experienced, authoritative, and trustworthy manufacturers ensures that each seal is precisely crafted to fulfill its purpose effectively, ultimately boosting operational efficiency and reliability.