Oil seals designed for high-pressure applications play a crucial role in a variety of industrial settings. These components, also known as rotary shaft seals, are engineered to ensure the flawless operation of machinery by preventing leaks and contaminant ingress in systems where hydraulic and lubricating fluids are used under high pressure.
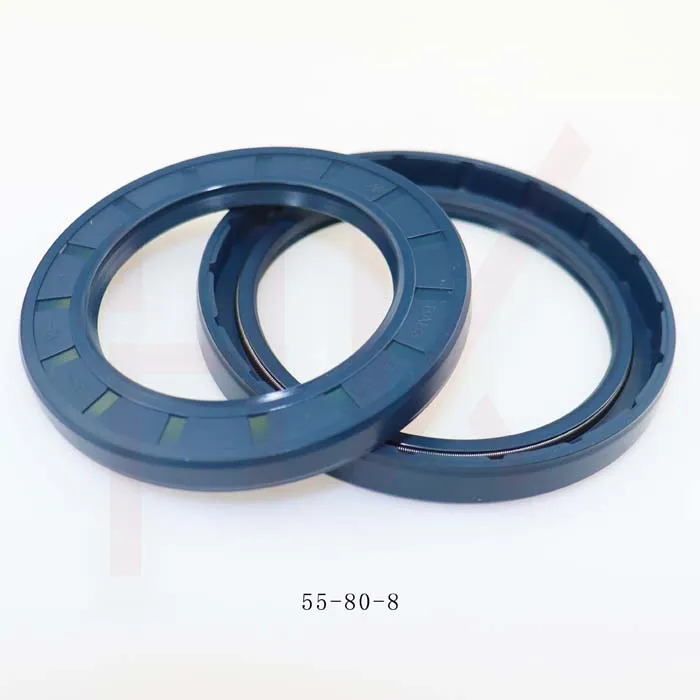
In industries where machinery is pushed to its limits, such as automotive, aerospace, and heavy machinery manufacturing, the demand for reliable oil seals cannot be overstated. These seals maintain the integrity of fluid systems, ensuring that they function optimally without the risk of damaging leakage that could lead to costly downtime or catastrophic equipment failure.
Manufacturing oil seals for high-pressure environments requires an expertise deeply rooted in material science and engineering. The seals must be made from robust materials that can withstand intense environments, including extreme pressures and high temperatures. Common materials include nitrile rubber, fluoroelastomers, and in some severe cases, PTFE, which offer durability and resistance to wear while maintaining a tight seal.
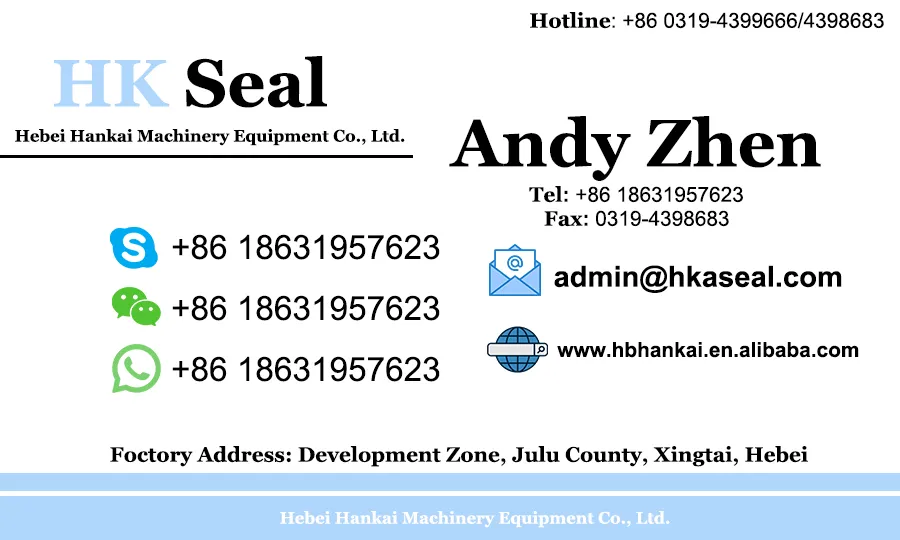
From experience, selecting the appropriate oil seal involves more than just understanding the operational environment. It begins with a thorough analysis of system requirements—considering factors like pressure levels, temperature ranges, and rotational speeds. Failure to properly assess these parameters can lead to seal failure. Consultation with seal manufacturers who demonstrate deep expertise in high-pressure applications can significantly enhance the longevity and reliability of the seals.
Professionals dealing in oil seals emphasize the need for precise measurement and installation processes. Misalignment or improper fitting can result in seal abrasion or extrusion, both of which compromise seal integrity. Therefore, employing specialized tools and adhering to manufacturer guidelines during installation ensures that the seals perform as expected.
oil seal high pressure
Moreover, regular maintenance checks are vital. They should be part of an overall predictive maintenance strategy that involves regular inspection for signs of wear and potential failure. By adopting smart maintenance practices, businesses can preempt seal-related issues, thereby enhancing machine uptime and reducing long-term operational costs.
The authority of any oil seal provider in high-pressure applications is not only demonstrated through their product offerings but also through their commitment to research and development. Leading companies invest significantly in innovation, developing next-generation seals that can handle higher pressures and temperatures while offering extended service life. By continuously improving seal design and material composition, they help industries meet evolving challenges.
Trustworthiness in the context of oil seals for high pressure means offering solutions that consistently perform as promised. It embodies providing technical support, ensuring product quality through rigorous testing, and maintaining transparent communication channels with clients.
In conclusion, oil seals suitable for high-pressure applications are essential to maintaining the efficiency and reliability of industrial machinery. Professionals seeking top-tier performance must engage with manufacturers who offer deep expertise, provide durable and innovative solutions, and uphold high standards of accountability. By doing so, they ensure that their machinery operates smoothly, seizing the benefits of high performance while mitigating the risks associated with high-pressure operations.