Oil seals, often considered the silent guardians of machinery, play a vital role in ensuring the longevity and optimal performance of countless mechanical systems. Used across various industries, these components exhibit a perfect blend of simplicity and engineering prowess, safeguarding systems from potential hazards such as contamination, leakage, and equipment failure.
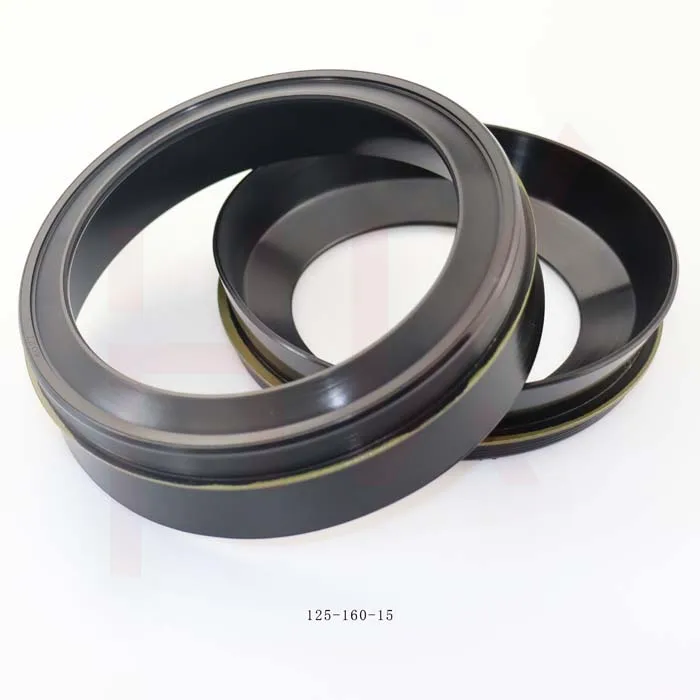
At their core, oil seals are designed to achieve one fundamental function to seal the gap between stationary and moving components within a mechanical assembly. This primary function is multi-faceted, encompassing several critical tasks that contribute to the seamless operation of machinery.
Firstly,
oil seals perform the function of containment. They prevent lubricants, primarily oils, from leaking out of the system, thereby ensuring that the internal components are appropriately lubricated. Lubrication is essential for reducing friction between moving parts, which in turn minimizes wear and tear, extends the lifespan of the components, and maintains efficient operation. When oil seals fail to contain the lubricant, machinery becomes prone to increased wear, overheating, and, eventually, catastrophic failure.
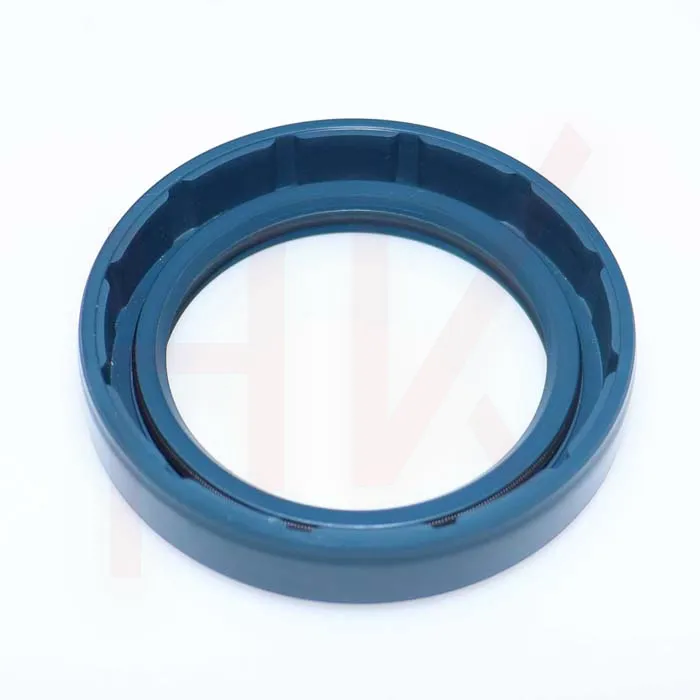
Moreover, oil seals serve as barriers against contamination. In industrial environments, machines are subjected to a plethora of contaminants, including dust, dirt, and moisture. If these external particles infiltrate the lubrication system, they can cause significant damage, leading to impaired performance or even complete shutdowns. By keeping such contaminants at bay, oil seals enhance the reliability and durability of machinery, ensuring that operations remain smooth and uninterrupted.
what is the function of oil seal
A further exploration of oil seals reveals their importance in maintaining pressure differentials within systems. Certain machinery, especially those involved in hydraulic and pneumatic applications, relies on specific pressure conditions to function correctly. Oil seals help maintain these pressure levels by providing a firm seal around moving shafts and other components. This capability prevents loss of pressure, thereby ensuring that the machinery operates efficiently and safely.
In terms of material science, oil seals are manufactured using high-performance materials like nitrile, silicone, and fluorocarbon, each selected based on the specific application and environment. These materials are engineered to withstand varying temperatures, pressures, and chemical exposures, highlighting the precise expertise involved in their design and the adaptability required for their functioning.
The selection and application of oil seals demand a keen understanding of both the machinery they serve and the environmental conditions in which they operate. Improper selection can lead to premature failure, resulting in costly repairs and downtime. Therefore, professionals who exhibit expertise in fluid dynamics and material science are highly instrumental in both the designing phase and the ongoing maintenance of these essential components.
Given their silent yet significant role, oil seals exemplify a key principle in engineering that the smallest components often hold the weightiest responsibilities. Their expert design and function ensure trustworthy results, underscoring their indispensability in a wide array of operations from automotive to aerospace, making them a cornerstone of industrial trustworthiness and reliability. A comprehensive understanding of oil seals not only enhances the expertise of industry professionals but also fortifies the foundational mechanisms of modern engineering.