Dust seals are an indispensable component in protecting mechanical systems from the degradation caused by dust and other environmental contaminants. In an era where machinery and equipment performance dictate the pace of industrial advancements and productivity, the role of dust seals cannot be overstated. This essential product applies across various industries, including automotive, aerospace, and manufacturing, safeguarding the integrity and longevity of components.
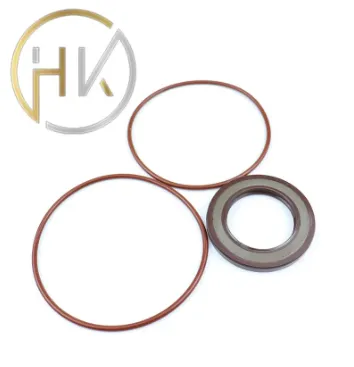
Real-world experience consistently demonstrates the critical nature of dust seals in operational efficiency and maintenance reduction. Expert technicians and engineers report fewer mechanical breakdowns and extended life of equipment when effective dust seals are employed. This is crucial in environments where dust and particulate matter are prevalent, such as mining operations or construction sites.
Understanding the diverse applications of dust seals showcases their versatility and adaptability. In the automotive industry, for instance, dust seals are pivotal in protecting internal components of engines and transmissions. They prevent dust and dirt from entering these systems, thus maintaining lubrication integrity and avoiding friction that leads to wear and tear. Similarly, in the aerospace sector, dust seals ensure that critical components remain uncontaminated, supporting both operational safety and efficiency.
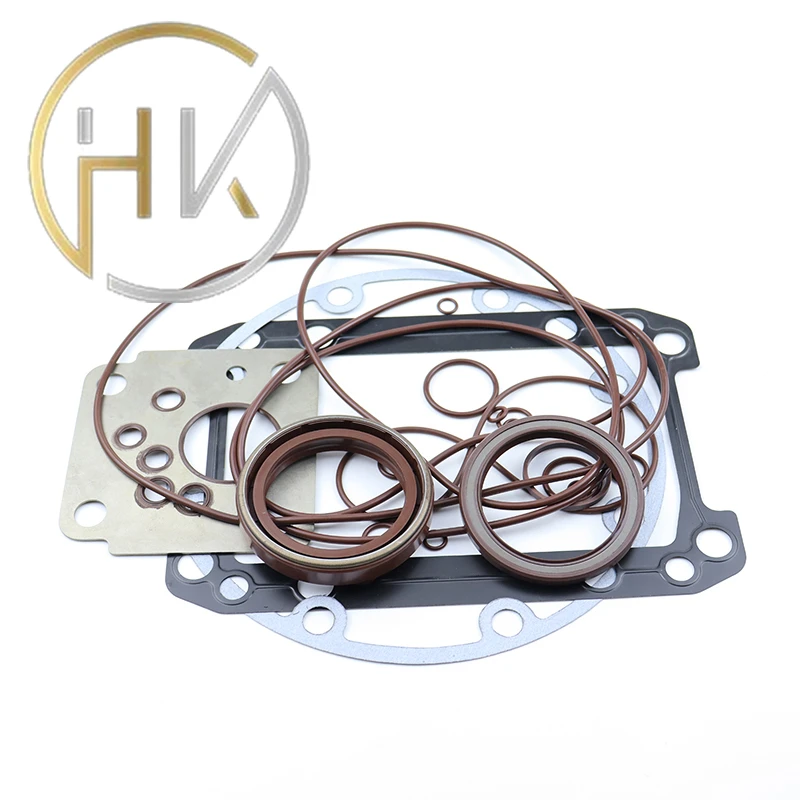
From a technical standpoint, expertise in the design and material selection for dust seals significantly impacts their effectiveness. Materials like polyurethane, silicone, and polytetrafluoroethylene (PTFE) are commonly chosen for their durability and resistance to environmental factors. Polyurethane’s resilience makes it suitable for high-impact environments, while silicone's temperature resistance is ideal for applications involving extreme thermal conditions. PTFE, known for its low friction and chemical resistance, is preferred in highly sensitive or chemically aggressive situations.
dust seal
By leveraging professional insights, companies can tailor dust seal specifications to meet specific operational needs, thus optimizing their machinery's performance. For example, employing double-lip or labyrinth-type seals can offer enhanced protection in settings with high dust concentration, ensuring minimal ingress of contaminants.
In terms of authoritativeness, industry standards and certifications enhance the credibility of dust seal manufacturers and their products.
ISO certifications and compliance with regulatory standards attest to the quality and reliability of the seals being furnished. Furthermore, leaders in the seal manufacturing industry often share data and insights from product testing and development, allowing for informed decision-making by engineers and maintenance personnel.
Trustworthiness is established through the consistent performance of dust seals in protecting key components, which is often substantiated by longevity studies and customer testimonials. Companies that have adopted robust dust seal solutions observe marked improvements in equipment uptime and reductions in maintenance costs, fostering trust in these protective solutions.
In conclusion, dust seals are more than just protective barriers; they are vital components that ensure the seamless operation and longevity of critical systems in various industries. With the expertise in design and material selection, adherence to industry standards, and proven trustworthiness through performance, dust seals represent an authoritative solution in the domain of environmental protection for machinery. For businesses aiming to enhance equipment reliability and cut maintenance expenses, investing in high-quality dust seals is a decision backed by both experience and professional acumen.