The shaft oil seal, often overshadowed by more conspicuous components in mechanical systems, plays a pivotal role in engineering applications. It ensures the seamless operation of machinery by preventing the leakage of lubricants and thereby sustaining optimal performance. A crucial element in a plethora of industries, the shaft oil seal demands careful attention and understanding to fully leverage its benefits.
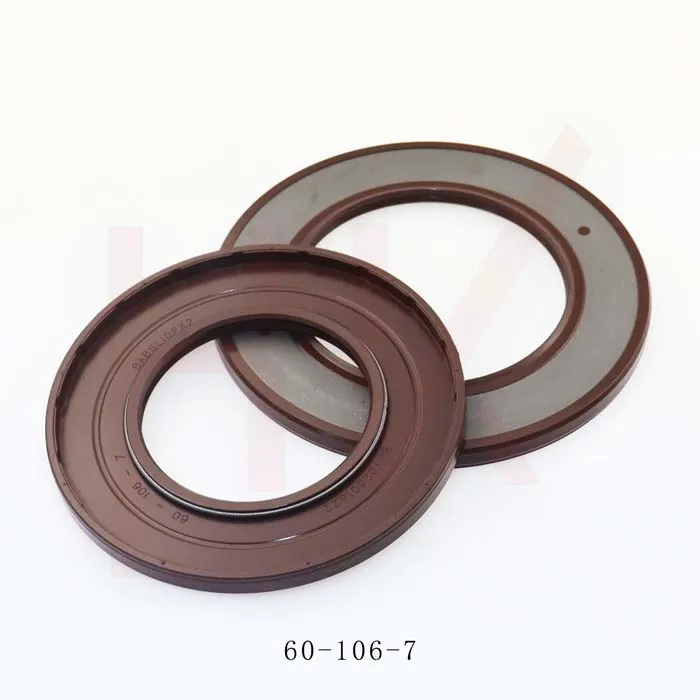
The primary function of a shaft oil seal is to separate two different components within machinery, maintaining a barrier between internal lubricants and the external environment. This separation not only preserves the lubricant but also safeguards the machinery from contaminants such as dust, dirt, and moisture. By doing so, the shaft oil seal minimizes wear and prolongs the lifespan of the mechanical system, thus contributing to a significant reduction in maintenance costs.
In terms of design, shaft oil seals are typically composed of a flexible elastomer lip, which is in direct contact with the shaft. Supporting this lip is a metallic insert, providing structural rigidity and ensuring consistent contact with the rotating shaft. This combination of materials must be chosen meticulously, taking into consideration the operational environment — temperature, speed, and chemical exposure all dictate the materials' compatibility and effectiveness.
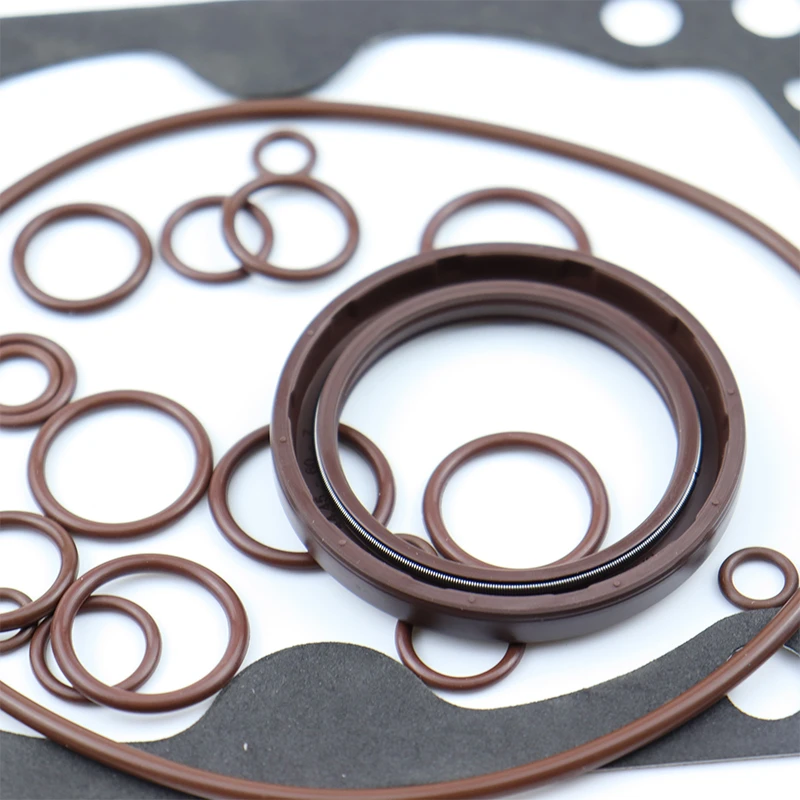
From a professional standpoint, selecting the right shaft oil seal requires expert knowledge. Not every seal is suitable for all applications; thus, understanding the specifics of each operation can prevent potential failures. Parameters such as shaft speed, temperature, the consistency of the lubricant, and the pressure it must withstand, all influence the selection process.
For instance, high-speed applications might require seals with low-friction materials to manage heat generated by operation. Conversely, in chemical-laden environments, seals made from fluorocarbon or Polytetrafluoroethylene (PTFE) offer superior resistance to corrosive elements. These nuances highlight the importance of expertise when handling shaft oil seals, underscoring that an informed selection process can enhance system efficiency and reliability.
shaft oil seal
In recent years, advancements in technology have introduced innovations in the realm of shaft oil seals. Manufacturers now utilize cutting-edge materials and design methodologies to produce seals with improved performance metrics. Computational simulations play a vital role in refining the design, allowing engineers to predict stress points and optimize the seal geometry for enhanced effectiveness.
Moreover, the concept of sustainability has permeated the engineering landscape. Modern shaft oil seals are increasingly being designed with eco-friendly processes, reducing material waste and energy consumption during manufacturing. This trend aligns with global efforts to minimize carbon footprints and protect the environment, resonating with industries seeking green solutions.
However, the crux of optimizing shaft oil seal performance lies in maintenance.
Regular inspection and timely replacement of worn seals are imperative. A neglected seal can lead to catastrophic failures, escalating repair costs, and unplanned downtime. Implementing a robust maintenance regimen, guided by thorough documentation and performance logging, ensures that machines operate at peak efficiency.
Establishing trust with your clientele also hinges on the quality assurance processes adhered to during the production of shaft oil seals. Reputable manufacturers subject their products to rigorous testing, complying with international standards to ensure reliability and longevity. This commitment to quality builds credibility and fosters long-term relationships with customers.
To summarize, the shaft oil seal is an indispensable component that requires astute understanding and expertise to employ effectively. Its role in maintaining lubricant integrity and safeguarding machinery underpins its significance in engineering. By embracing innovations, committing to sustainability, and upholding stringent maintenance practices, industries can fully exploit the potential of shaft oil seals, ensuring their systems run smoothly and efficiently — a testament to the seal's enduring value and importance.