In the universe of mechanical engineering and automotive design, the humble oil seal stands as a silent guardian, playing an indispensable role in ensuring the efficiency and longevity of machinery. The importance of oil seals cannot be overstated as they keep machinery running smoothly by preventing the leakage of lubricants and blocking contaminants from creeping into the system. This multifaceted component is essential for maintaining the seamless operation of various applications across industries.

Drawing from years of experience in the field, oil seals have been engineered to be robust in their functionality and design. Manufactured from a range of materials such as nitrile rubber, silicone, and polymer composites, these seals are tailored to withstand extreme conditions, including high pressure, temperature fluctuations, and aggressive contaminants. The choice of material is critical, as it determines the seal's ability to perform under different mechanical stresses, thereby directly impacting the machinery's reliability.
Oil seals are vital in automotive engines,
hydraulic systems, and industrial machinery. Their primary purpose is to seal the spaces between stationary and moving components in equipment, thus preventing the escape of oils and lubricants. This not only prevents leakage but also enhances the performance of the machinery by maintaining optimal lubrication conditions. The result is a reduction in wear and tear, minimization of maintenance costs, and extension of the overall lifespan of the equipment.
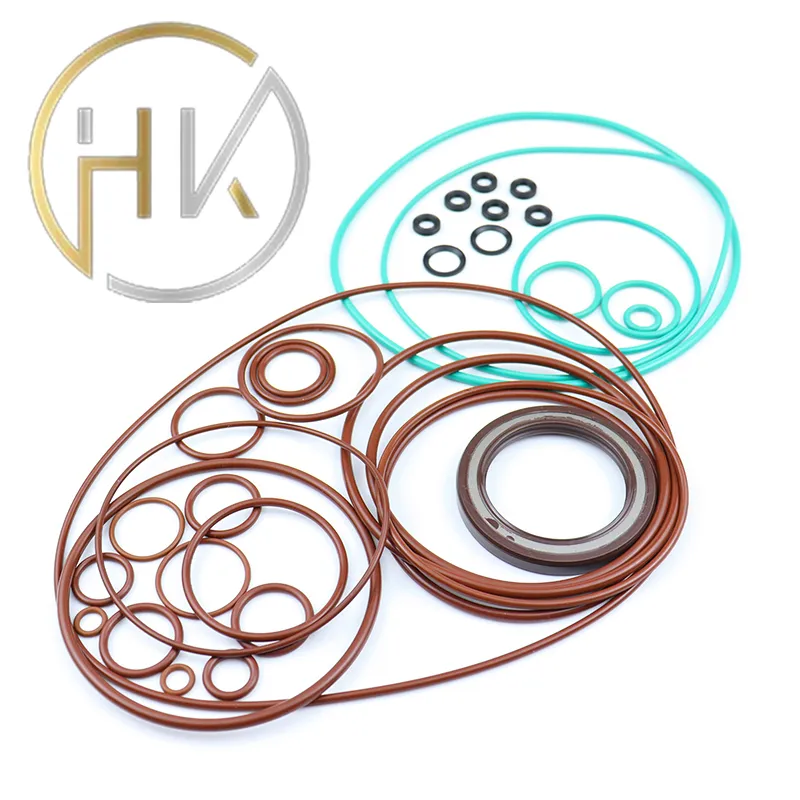
Expertise in the selection and installation of oil seals is paramount, as even the slightest miscalculation can lead to compromised performance. The precise fit is crucial — too tight, and the seal may wear prematurely; too loose, and it could fail to prevent leakage. The installation process often requires specialized tools and trained personnel to ensure that seals are correctly seated and that interference and centricity tolerances are maintained.
oil seals
From an authoritative perspective, industry standards such as ISO and DIN specify the dimensions, tolerance, and materials of oil seals. These standards are crucial for manufacturers and engineers alike, ensuring compatibility and reliability across different applications and international boundaries. In compliance with these standards, oil seals are subject to rigorous testing to confirm their endurance under simulated real-world conditions. This meticulous verification process further underlines their unmatched importance in the integrity of mechanical assemblies.
Trustworthiness is an inherent characteristic of quality oil seals, achieved through extensive research and development undertaken by leading manufacturers. These seals are the result of sophisticated engineering and innovation, combining materials science with cutting-edge design technology. Companies that invest in quality assurance and adhere to safety certifications further cement their reputation, becoming trusted partners in the industrial and automotive sectors.
Ensuring the effectiveness of oil seals involves routine inspection and maintenance. Regular checks for wear, cracks, or distortions are vital in preempting failures that could lead to costly repairs or operational downtime. Replacing oil seals at recommended intervals rather than waiting for them to fail can save substantial resources in the long run. Engineers often emphasize predictive maintenance strategies, which leverage data and software tools to predict seal lifespan based on usage patterns and environmental conditions.
In conclusion, the oil seal, though modest in appearance, is a cornerstone of efficient machinery operation. From safeguarding against leaks to protecting against contaminants, its role is foundational in both automotive and industrial applications. Relying on expert knowledge, adhering to authoritative standards, and fostering trustworthy manufacturing practices are essential in maximizing the performance and reliability of oil seals. As machinery continues to evolve, the innovation in oil seal technology will undoubtedly advance, further cementing their indispensable role in the world of engineering.