In industries where precision and durability are paramount, sealing ring kits play an indispensable role. These versatile and essential components are crucial for ensuring the integrity of various systems, from automotive engines to complex industrial machinery. Understanding the importance, design, application, and maintenance of sealing ring kits not only elevates one's mechanical prowess but also ensures operational efficiency and longevity.
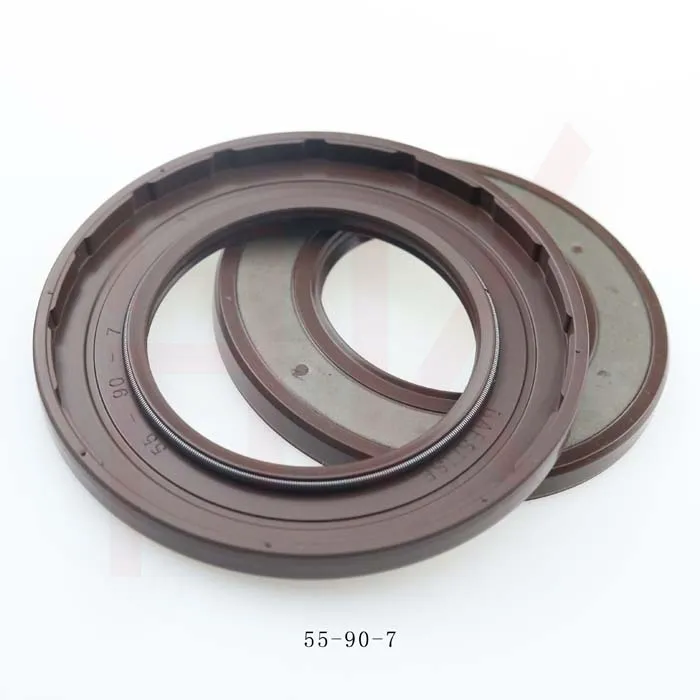
Sealing ring kits are collections of rings made from different materials like rubber, silicone, or PTFE, each selected based on the specific needs of the application. Their primary function is to provide a robust seal that prevents the leakage of fluids or gases, maintaining pressure and ensuring the operational efficacy of mechanical systems. This function might seem straightforward, but the complexity lies in choosing the correct material, size, and type of sealing ring for the task at hand.
A typical sealing ring kit includes a variety of rings designed to fit different grooves and cavities. In automotive systems, for instance, they play a critical role in engine performance by preventing oil leaks and maintaining proper compression. In an industrial setting, they help in maintaining the hydraulic or pneumatic systems that power machinery. The choice of sealing ring impacts not just the performance but also the safety and maintenance costs of the equipment involved.
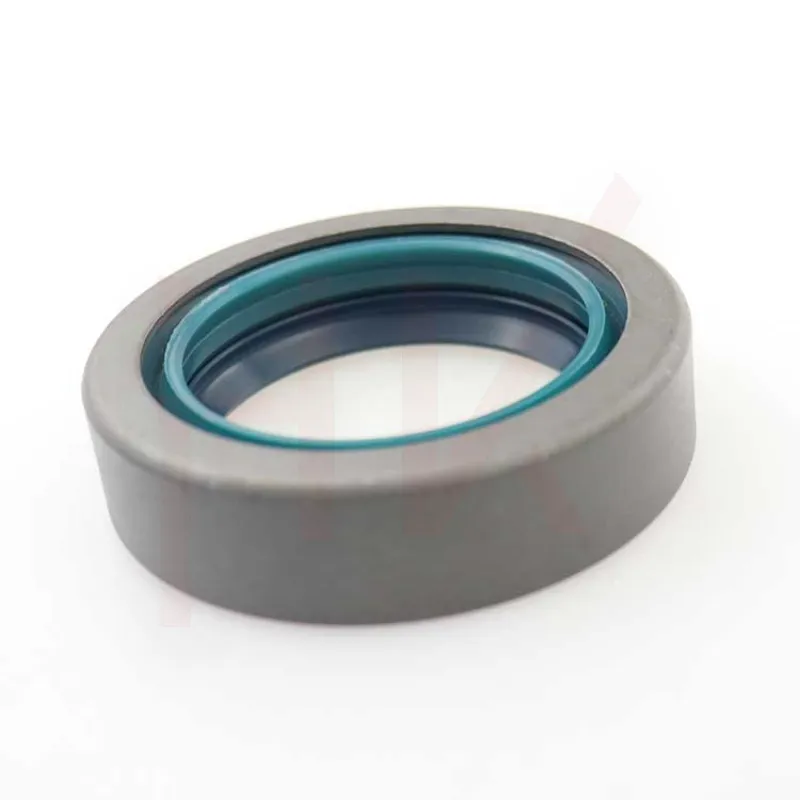
Expertise in selecting and applying sealing ring kits is necessary for any engineer or technician involved in equipment maintenance or manufacturing. Factors such as temperature, pressure, chemical compatibility, and the mechanical load are crucial when deciding on the right sealing ring. The wrong choice can lead to catastrophic system failures, costly downtimes, and even pose safety hazards. Therefore, it's vital that users are adept in understanding these variables and proficient in applying this knowledge to ensure seamless operations.
sealing ring kit
Trustworthiness in the use of sealing ring kits comes from utilizing high-quality products from reputable manufacturers. Quality assurance is crucial; a reliable kit will offer consistency and durability, reducing the risk of premature failure. Additionally, understanding the specifications and industry standards can prevent purchasing inferior products that carry the risk of failure.
Sealing ring kits also demand regular maintenance checks for wear and tear. Over time, exposure to extreme conditions can degrade materials, compromising their sealing efficiency. Regular inspections and timely replacements are therefore part of maintaining a robust machinery system. Maintaining a log of inspections and replacements further enhances operational integrity and prolongs equipment lifespan.
Authority in the field of sealing ring kits comes from staying updated with the latest advancements in materials science and technology. Innovations often lead to the development of new materials or ring designs that offer improved performance, sustainability, and cost-efficiency. Engaging with industry seminars, workshops, and literature can provide a substantive edge in this continuously evolving field.
In conclusion, mastery over sealing ring kits involves understanding the nuanced balance between material properties, system requirements, and operational conditions. For those in engineering and maintenance, it is not enough to see these kits as mere accessories; they are pivotal components that guarantee the precision and reliability of machinery systems. By leveraging expertise, reliable sourcing, regular maintenance, and continuous learning, businesses ensure their systems are efficient, safe, and economical.