High pressure pump seals play an indispensable role in the efficient and reliable operation of high-pressure pumping systems. As the linchpin of fluid control, these seals are tasked with ensuring that high-pressure pumps maintain optimum pressure levels while preventing leaks. Their significance cannot be understated, especially in industries such as oil and gas, chemical processing, and water treatment, where fluid integrity is paramount.
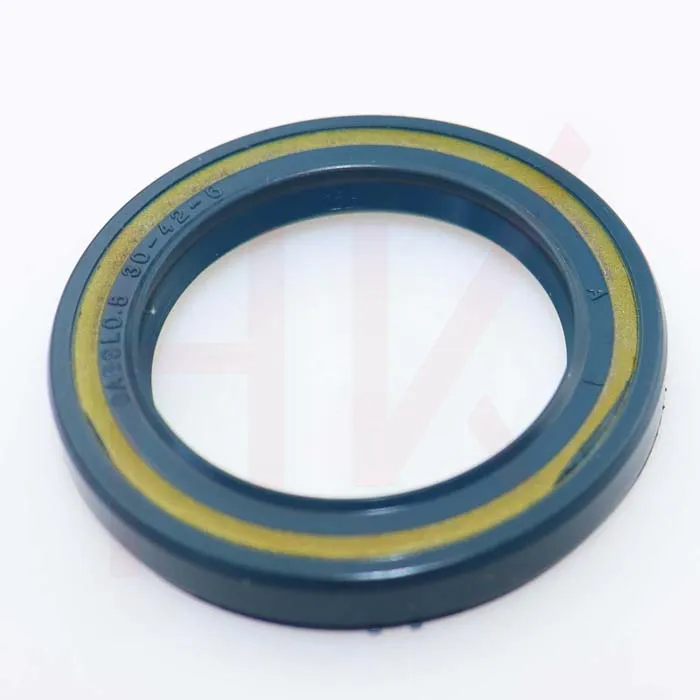
Experience with high pressure pump seals often underscores the need for precise installation and maintenance protocols. Misalignments or improper installation can lead to catastrophic failures. Those with hands-on experience emphasize the importance of regular inspections and timely replacements. For example, in the oil and gas sector, the failure of a pump seal can result in operational downtime costing thousands of dollars per hour, not to mention the environmental and safety risks involved.
Professional expertise surrounding high pressure pump seals involves a deep understanding of material science and fluid dynamics. Modern seals are crafted from advanced materials like Teflon, Viton, or high-performance elastomers, each chosen based on the specific chemical and thermal conditions they will face. Engineers with expertise in this area focus on the compatibility of seal material with the pumped fluid. For instance, some chemicals might require seals made from resistant materials to avoid degradation and ensure longevity.
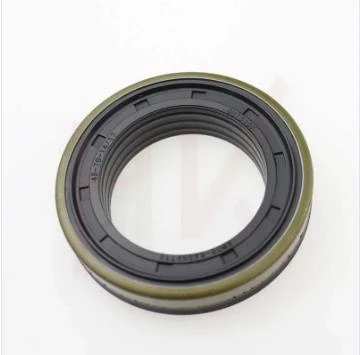
Authoritativeness in the field of high pressure pump seals is often attributed to the manufacturers who lead in research and development. Companies such as John Crane and Flowserve are often cited as industry standard-bearers. Their commitment to innovation results in seals that push the boundaries of temperature and pressure resistance. Moreover, their certifications and compliance with industry standards, such as those from the American Petroleum Institute (API), provide additional layers of credibility and trustworthiness to their products.
high pressure pump seal
Trustworthiness in high pressure pump seals is further enhanced by rigorous testing and quality assurance processes. Trust comes from not only meeting promises but exceeding them with proven reliability and performance. Manufacturers typically conduct extensive fatigue testing, thermal cycling, and pressure endurance trials to ensure each seal can withstand real-world application demands. Users who have consistently seen their equipment outperform expectations offer testimonials that bolster the trust others place in these seals.
Understanding the intricacies of high pressure pump seals also involves comprehending the various types available, such as single, double, and cartridge seals. Each type offers unique benefits and considerations. Single seals, while cost-effective, may not provide the redundancy needed for critical applications. Double seals offer additional security but at a higher upfront cost. Cartridge seals, on the other hand, simplify installation and reduce maintenance time.
When selecting a high pressure pump seal, it is essential to consult with experts who can analyze the operational parameters and environment to recommend the best solution. Factors such as pump operating speed,
pressure load, and fluid properties dictate the optimal seal choice. An ill-suited seal can lead to energy inefficiency, increased maintenance costs, and premature system wear.
In conclusion, the world of high pressure pump seals is one marked by precision, expertise, and a commitment to excellence. The interplay of materials science, engineering acumen, and rigorous testing protocols ensures that these seals remain robust under pressure. Whether for industry newcomers or seasoned professionals, investing in quality seals and adhering to best practices in their maintenance will invariably lead to enhanced system performance and reliability.