Rotary shaft oil seals, often considered the unsung heroes in mechanical assemblies, play a pivotal role in ensuring machinery functions smoothly by preventing leakage of lubricants and protecting against contaminants like dust, dirt, and moisture. These seals are indispensable in numerous applications, from automotive engines and agricultural machinery to industrial turbines and robotics. Let us delve into the intricacies of rotary shaft oil seals, exploring various aspects that underscore their significance and utility.
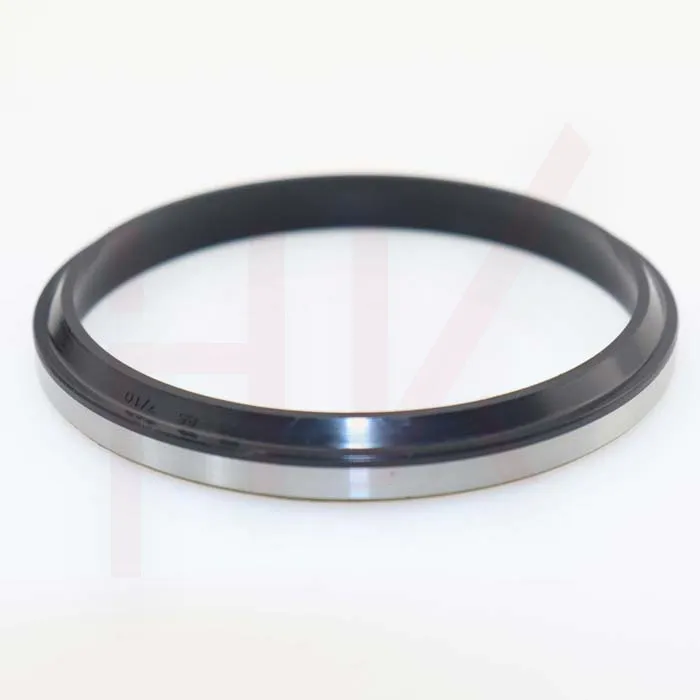
Crafted with precision, rotary shaft oil seals come in various materials such as nitrile rubber, fluoroelastomers, silicone, and PTFE, each offering unique benefits suited to specific environments. Nitrile rubber, for instance, is renowned for its excellent resistance to petroleum-based oils, making it an ideal choice for automotive industries. On the other hand, fluoroelastomers provide superior heat and chemical resistance, making them indispensable in high-temperature applications.
The design of rotary shaft oil seals is tailored to ensure optimal performance. These seals typically comprise three main components the sealing element, the metal case, and the spring. The sealing element, usually made from flexible materials, adheres closely to the rotating shaft, providing an effective barrier against fluid escape. The metal case offers structural support, enhancing the seal's rigidity and helping it fit snugly within the machinery housing. Meanwhile, the spring ensures consistent pressure, keeping the sealing lip engaged with the shaft despite fluctuations in pressure and temperature.
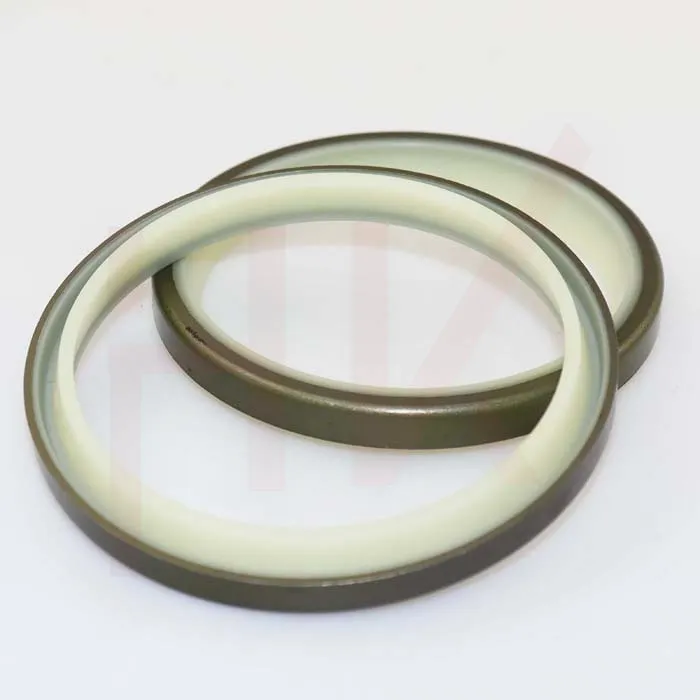
In practical terms, the reliability of rotary shaft oil seals translates into extended machinery life and reduced downtime. Their effectiveness in keeping lubricants in and contaminants out ensures that mechanical components remain well-lubricated and are protected from wear and tear, thus extending their longevity. This not only optimizes performance but also results in substantial cost savings by minimizing the need for frequent maintenance or part replacements.
rotary shaft oil seals
When selecting a rotary shaft oil seal, several factors warrant consideration. Shaft speed is paramount, as seals must withstand the dynamic conditions generated by rapid rotations. Material compatibility is equally critical; the seal must not interact adversely with the lubricants and chemicals it encounters. Temperature and pressure ranges of the operating environment should also dictate the choice of seal to ensure durability under extreme conditions. Finally, installation dimensions and tolerances must be meticulously adhered to, guaranteeing a secure fit and optimal function.
Installation precision can't be overstated when it comes to maximizing the efficacy of rotary shaft oil seals. Improper alignment, forceful fitting, or overlooking surface finishes can lead to premature seal failure. Employing careful alignment techniques and utilizing appropriate fitting tools is essential in preserving the integrity of the seal. This meticulous approach not only enhances sealing performance but also fortifies the dependability and efficiency of the overall mechanical assembly.
The evolution of rotary shaft oil seals continues as technological advancements foster innovative designs and materials. Today, there is a growing trend towards incorporating smart materials and advanced manufacturing processes in seal production. These developments aim to offer enhanced performance characteristics, such as self-lubricating properties and improved wear resistance, catering to increasingly demanding industrial applications.
In summary, rotary shaft oil seals are integral to the proper functioning of myriad mechanical systems. Their role in safeguarding vital components from the adversities of operation makes them invaluable in industrial, automotive, and agricultural applications. Understanding the nuances of their materials, designs, and installation is crucial in harnessing their full potential. This not only emphasizes the seals’ technical importance but also attests to their role in promoting sustainable engineering practices and optimizing operational efficiency.