Metric shaft seals are indispensable components in various machinery and equipment, ensuring that fluids do not leak from rotating parts while maintaining optimal operational efficiency. Understanding their intricacies and applications can offer unique advantages to manufacturers and engineers who aim to enhance machine longevity and reliability.
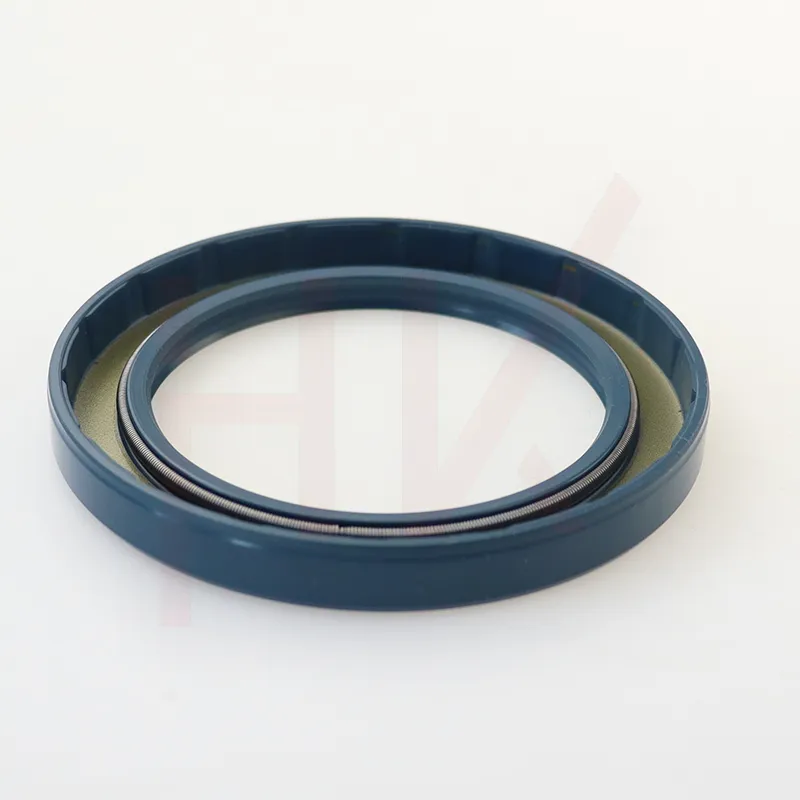
Shaft seals, commonly known as rotary seals or lip seals, play a vital role in preventing leakage of lubricants such as oils and greases while keeping external contaminants like dust and moisture at bay. They are particularly critical in environments requiring precision and where mechanical failure could result in significant downtime or costly repairs.
The science behind metric shaft seals lies in their engineered design and material selection. A key aspect of their function is the lip of the seal, which is designed to contact the shaft tightly to form an effective barrier. The material from which the lip is made is often a synthetic rubber or polymer, chosen for its ability to withstand harsh chemical environments, temperature extremes, and wear over time. Advanced formulations such as polytetrafluoroethylene (PTFE) or fluoroelastomer (FKM) are frequently used due to their excellent resistance to chemicals and thermal degradation, offering more durability than standard materials.
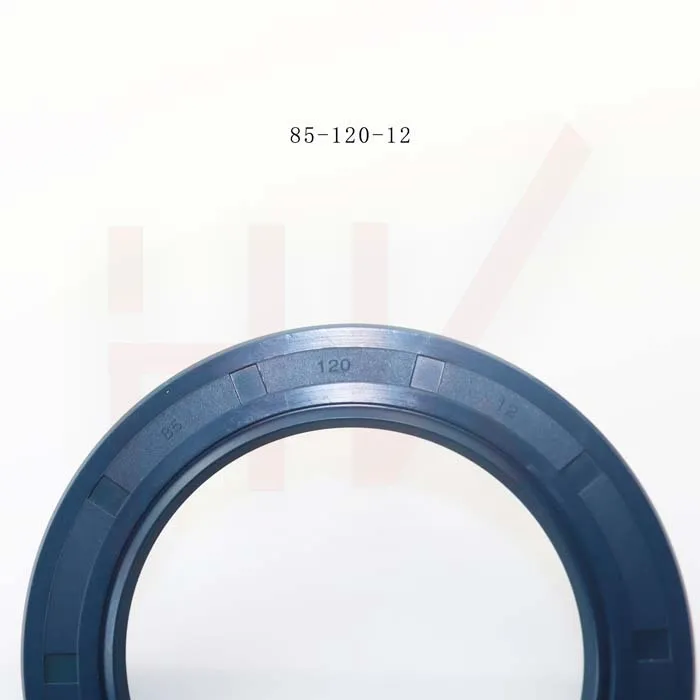
Moreover, the construction of metric shaft seals can incorporate spring-loaded mechanisms that enhance sealing capabilities by maintaining consistent contact pressure against the shaft. This ensures that even as the seal wears or encounters shaft misalignments, it continues to perform effectively.
In the broader context of mechanical engineering, the choice of metric over imperial measurement standards for shaft seals aligns with global industrial practices. Metric seals provide the precision required for compatibility with European and international machinery. This universality ensures that maintenance and replacement are straightforward for multinational operations, reducing downtime and inventory costs due to incompatible parts.
Real-world applications of metric shaft seals are diverse and crucial across various industries. They are essential in automotive engines, where they prevent the leakage of engine oil, thus ensuring the longevity of the engine and optimal performance. In manufacturing setups, they secure the integrity of hydraulic systems, preventing fluid leakage that could result in pressure loss and inefficiencies. Furthermore, in the food and beverage industry, specialized metric shaft seals are employed to meet stringent hygiene standards while resisting degradation from aggressive cleaning chemicals.
metric shaft seals
The experience of leading engineers and technicians consistently highlights that proper installation, monitoring, and maintenance of shaft seals significantly enhance their lifespan and reliability. It is crucial that sealing surfaces and shafts are impeccably clean and undamaged before installation.
Any imperfections can quickly lead to seal failure. Using the correct lubrication is equally important to minimize friction and wear between the seal and the shaft.
Furthermore, expert recommendations underscore the value of regular inspection and preventative maintenance. Technicians are advised to check seals routinely for signs of hardening, cracking, or excessive wear. Addressing these issues promptly can prevent fluid escape, ensuring continuous machinery operation and avoiding sudden breakdowns.
Choosing the right metric shaft seal involves careful consideration of the operating environment, pressure conditions, and the type of fluid being sealed. A one-size-fits-all approach is rarely effective; hence, consulting manufacturers or experienced suppliers for tailored solutions can yield significant benefits.
Establishing trust with a reputable supplier assures access to high-quality materials and seals tailored to specific applications. This partnership often includes technical support, ensuring that the seals chosen not only meet the necessary specifications but also contribute to the overall efficiency and reliability of the machinery involved.
By investing in quality metric shaft seals and prioritizing proper installation and maintenance practices, companies can significantly minimize risks of leaks and breakdowns, thereby securing a competitive edge through enhanced operational reliability and safety. This approach embodies the principles of expertise, authoritativeness, experience, and trustworthiness in industrial applications.