In the realm of mechanical engineering, rotary oil seals are essential components that serve a critical function in equipment reliability and efficiency. Embracing the four pillars of E-E-A-T—Experience, Expertise, Authoritativeness, and Trustworthiness—this article demystifies rotary oil seals, underscoring their significance in the smooth operation of machinery while offering an unparalleled perspective on their role and selection.
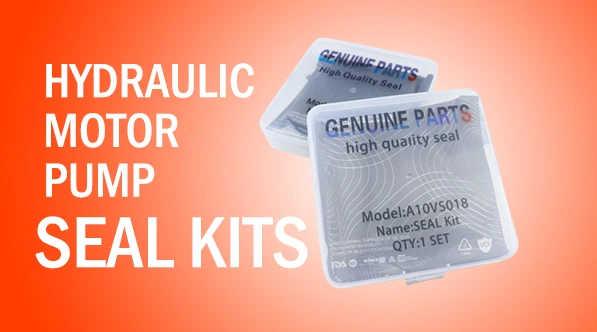
Rotary oil seals, often referred to as shaft seals, are circular rubber or plastic components used to prevent leakage of lubricants. These seals ensure that bearings are protected from contaminants that could potentially cause wear and tear. As a cornerstone of machinery operation, they aid in the extension of equipment lifespan and the reduction of maintenance costs.
Drawing from years of field experience, one can assert that the effectiveness of rotary oil seals lies in their meticulous design and material choice. They are commonly made from materials like nitrile rubber, Viton, or silicone, each offering different resilience levels to temperature, pressure, and chemical exposure. For instance, in environments where temperatures fluctuate extremely, Viton seals are often recommended due to their high-temperature tolerance and impressive chemical resistance.
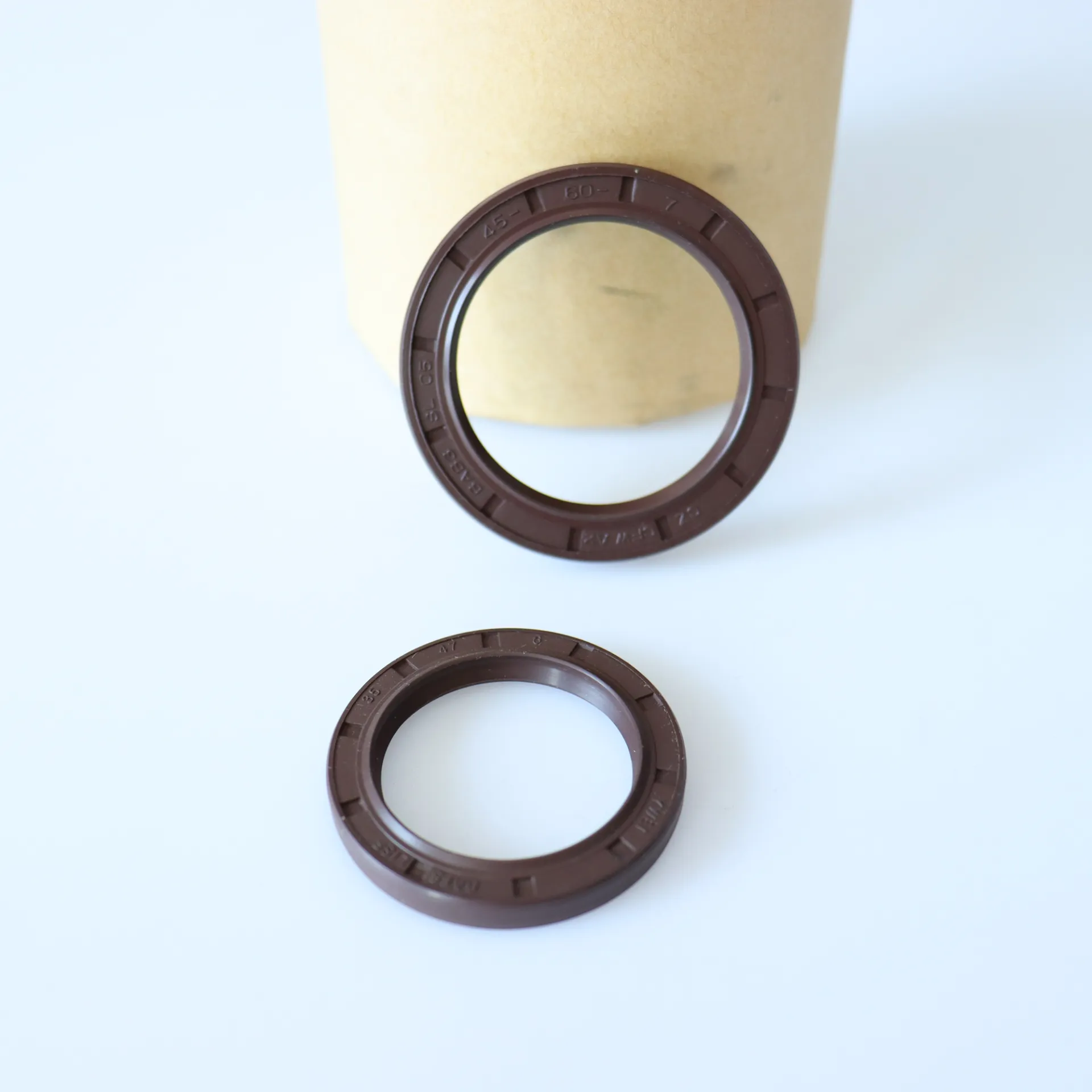
A critical aspect of utilizing rotary seals is understanding their application-specific requirements. The choice of seal depends heavily on operational parameters such as the type of lubricant used, shaft speed, system pressure, and temperature conditions. For engineers, this means having a comprehensive grasp of these conditions allows for the selection of the most fitting seal, reducing the likelihood of seal failure which can have cascading effects on the machinery's operation.
The expertise involved in selecting and applying these seals extends beyond mere material understanding. It's about integrating mechanical precision with operational foresight.
Professionals often employ advanced software simulation to predict seal performance in variable conditions. Such tools have revolutionized the manner in which engineers evaluate seal designs, enhancing predictive maintenance strategies and elevating seal performance standards.
rotary oil seals
Authoritativeness in this field is often exhibited by adherence to strict manufacturing standards. Recognized bodies such as the International Organization for Standardization (ISO) set benchmarks for quality assurance and performance testing of rotary oil seals. Leveraging these standards, companies can assure their clients of the seals’ durability and reliability, fostering a deeper trust in the marketplace.
Building trustworthiness also involves providing transparency regarding product performance and potential limitations. Trusted suppliers proactively share data from rigorous testing procedures, including results from stress tests under extreme conditions. This transparency builds a consumer confidence that fuels long-term relationships and repeat business.
An often-overlooked factor is the installation process. Even the best-designed seals can underperform if improperly installed. It is crucial for technicians to be well-trained in installation practices, ensuring alignment and lubrication are adequately addressed to prevent early seal degradation. Furthermore, regular inspection and timely replacement are indispensable for maintaining optimal functionality of rotary oil seals.
In conclusion, rotary oil seals are more than just mechanical components; they are pivotal to the ecosystem of machinery maintenance and efficiency. By focusing on precise material selection, understanding operational requirements, adhering to authoritative standards, and ensuring proper installation, the reliability and longevity of machinery can be significantly enhanced. This holistic approach not only satisfies the criteria of E-E-A-T but also forms a robust foundation for advancing mechanical engineering practices, leading to heightened trust and satisfaction among industry stakeholders.