Rotary lip seals, sometimes referred to as oil seals or radial shaft seals, play a crucial role in a vast array of industrial applications. They are engineered to retain lubricants, exclude contaminants, and separate fluids, all while ensuring the smooth operation of rotary equipment. These seals are vital for maintaining the efficiency, longevity, and safety of machinery, especially where rotational speed and pressure are significant factors.
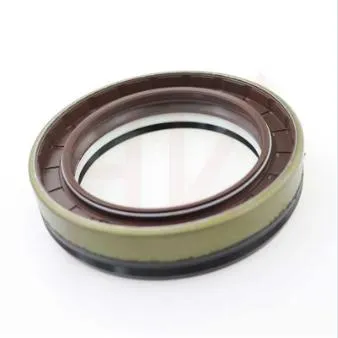
Understanding rotary lip seals requires a journey through their design, material composition, and functional capabilities. The core function of these seals involves maintaining the separation between lubricated and non-lubricated areas of a machine, preventing the ingress of contaminants, and controlling the leakage of lubricants such as oil and grease. This is essential for the optimal performance and durability of machinery, from automotive engines to industrial pumps and wind turbines.
The design of a rotary lip seal is ingenious in its simplicity yet profound in its impact. A typical seal comprises three key components the sealing lip, the metal case, and the spring. The sealing lip is often crafted from elastomers like nitrile rubber (NBR), fluorocarbon (FKM), or silicone, chosen for their flexibility, wear resistance, and chemical compatibility. The metal case provides structural support, typically made of stainless steel or another corrosion-resistant material. The spring exerts a consistent radial force, ensuring the sealing lip maintains contact with the rotating shaft.
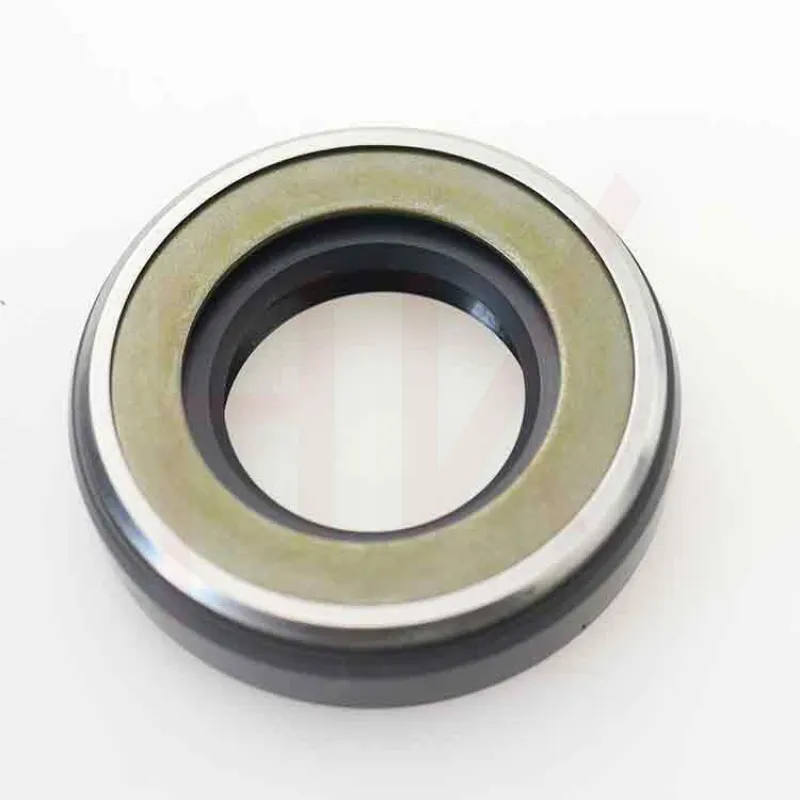
Imagine an industrial setting where a rotary pump moves viscous fluids at high temperatures. A breakdown in the sealing mechanism could result in catastrophic equipment failure, leading to costly downtime and repairs. Here, the expertise of selecting the right rotary lip seal is of paramount importance. Engineers assess factors like shaft size, rotational speed, temperature range, pressure differential, and chemical exposure. Understanding these parameters allows them to choose seals with the appropriate elastomeric composition and structural design.
The authoritativeness of a brand in the rotary lip seal market is often established through a combination of historical reliability, innovative design, and industry certifications. Leading manufacturers like SKF, Parker Hannifin, and Freudenberg Sealing Technologies are recognized for their cutting-edge research and high-quality products. They continually enhance their product lines to address evolving industrial challenges, such as increasing energy efficiency or reducing environmental impact.
rotary lip seal
To build trustworthiness in rotary lip seals, manufacturers and suppliers often provide comprehensive technical support. This includes detailed installation guides, maintenance tips, and troubleshooting advice to ensure end-users can maximize seal performance and lifespan. Additionally, warranties and guarantees further solidify the trust of the consumer, underscoring a commitment to quality and reliability.
Real-world experiences underscore the value of rotary lip seals. Consider a wind turbine in an offshore environment, facing the challenges of saltwater exposure, high winds, and temperature extremes. A well-chosen lip seal protects the gearbox from the harsh elements, ensuring reliable power generation and reducing maintenance costs. Such seals are tested rigorously to mimic these conditions, ensuring they perform under pressure and deliver consistent results.
As the industrial landscape shifts towards more sustainable practices, rotary lip seals are not exempt from scrutiny. Innovations in this field include the development of seals made from bio-based or recycled materials that meet stringent performance criteria, showcasing a commitment to environmental stewardship alongside mechanical excellence.
In conclusion, rotary lip seals are indispensable components in machinery across numerous industries. Their role extends beyond simple sealing, embodying the principles of efficiency, reliability, and sustainability. As technology progresses, these seals will continue to evolve, addressing new challenges and opportunities in various sectors. Choosing the right rotary lip seal involves a blend of technical expertise, material science, and practical application, ensuring machinery operates smoothly and effectively, safeguarding investments and enabling progress.