Navigating the world of high-pressure applications requires understanding and precision, especially when it comes to components such as oil seals. Oil seals, commonly referred to as shaft seals or rotary seals, play a crucial role in machinery that operates under high pressure. Their primary function is to retain lubricants and keep out contaminants, ensuring optimal performance and longevity of the machinery. Choosing the right oil seal for high-pressure settings is essential, and here’s an expert guide to understanding and selecting these critical components.
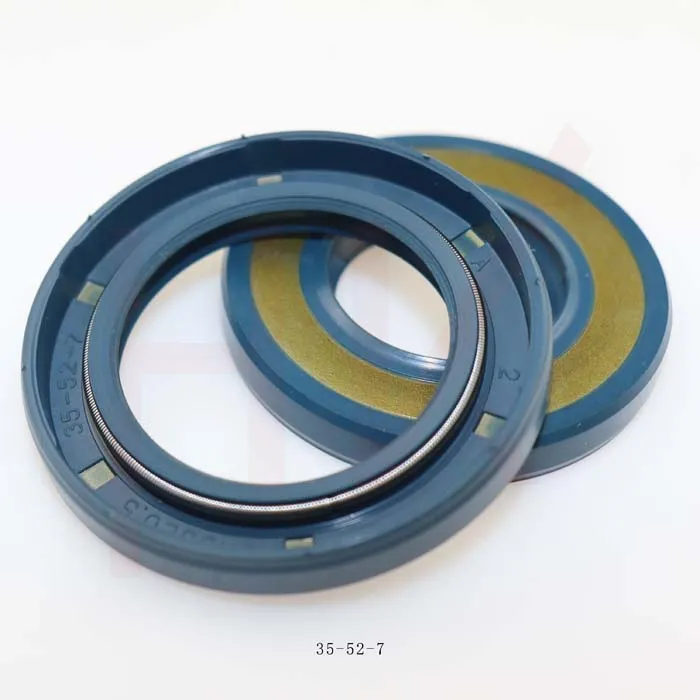
High-pressure environments demand robust oil seals, designed to withstand extreme conditions while maintaining their integrity. These seals are engineered from specialized materials like fluoroelastomer (FKM), hydrogenated nitrile butadiene rubber (HNBR), and polytetrafluoroethylene (PTFE), each offering unique properties. While FKM provides excellent resistance to heat and chemicals, HNBR is renowned for its superior performance in environments subject to high pressure and temperature fluctuations. PTFE, on the other hand, offers flexibility and is highly resistant to almost all chemicals, making it a favorite in diverse industrial applications.
Selecting the appropriate oil seal involves more than just choosing the right material. It requires an understanding of the application's operational parameters, such as pressure levels, temperature ranges, and fluid compatibility. For example, systems operating at pressures exceeding 500 psi need seals specifically designed to handle such loads. Traditional seals can fail under extreme pressure, leading to leakage, contamination, and ultimately machinery failure. Therefore, high-pressure oil seals are fortified with reinforced structures and enhanced lip designs to maintain a secure fit and proper function under demanding conditions.
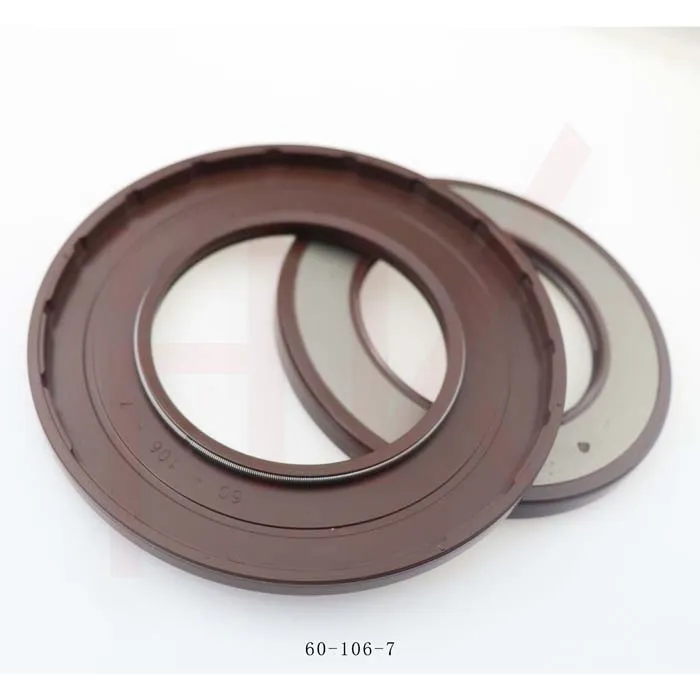
Expertise in installation is another critical factor influencing the performance of oil seals in high-pressure settings.
Incorrect installation can lead to seal damage and premature failure. Installation best practices include ensuring the shaft is free from nicks and scratches, applying appropriate lubricant to avoid dry running during start-up, and confirming the seals are neither too loose nor overly tight. An accurately installed oil seal can significantly extend the service life of both the seal and the machinery it protects.
oil seal high pressure
Trust in the manufacturer of oil seals is equally vital. Reputable manufacturers subject their seals to rigorous testing, simulating extreme pressure scenarios to ensure reliability and durability. Their adherence to international quality standards and certifications such as ISO 9001 reinforces the trustworthiness and reliability of their products. When sourcing high-pressure oil seals, prioritize companies with a proven track record and positive customer feedback, as these are indicators of product quality and customer support.
For businesses and engineers seeking authoritative data, it’s advisable to consult with industry experts and leverage simulation software that predicts seal performance under various conditions. These simulations, combined with empirical testing, provide invaluable insights, enabling informed choices that align with specific operational needs.
In conclusion, the right oil seal can significantly impact the efficiency and lifespan of machinery operating in high-pressure environments. A comprehensive understanding of material properties, precise installation techniques, and reliance on reputable manufacturers ensures that the selected oil seal not only meets but exceeds operational demands. Whether you are an engineer tasked with maintaining industrial equipment or a procurement manager, prioritizing these factors will lead to optimal outcomes, safeguarding your investment and enhancing operational efficiency.