Enhancing machinery performance hinges significantly on the efficiency of components, one of which is the often underestimated oil seal for rotating shafts. These vital components play a crucial role in safeguarding mechanical systems, ensuring their longevity and consistent performance. Through innovation in materials and design, oil seals have evolved, offering unparalleled reliability.
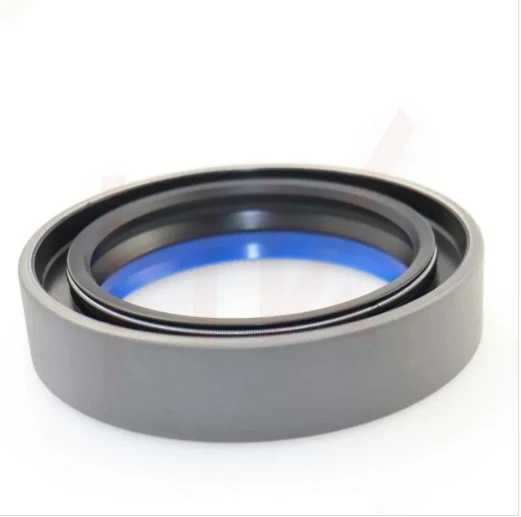
Oil seals, often dubbed as shaft seals, lip seals, or rotary seals, are essential in preventing fluid leakage between stationary and moving components in mechanical systems. By preventing contaminants from entering the equipment, they bolster the durability of the machinery, thus optimizing operational efficiency. This meticulous protection is critical, particularly in industries where equipment downtime can lead to substantial financial losses.
From an experiential standpoint, utilizing high-quality oil seals can markedly diminish maintenance costs. An insightful example is their application in automotive engines. A well-installed oil seal in an engine can dramatically reduce the deleterious effects of oil leaks, which otherwise lead to engine overheating or, worse, failure. For car enthusiasts and auto mechanics, ensuring that the oil seal is in peak condition means engines run smoother, less oil is consumed, and, ultimately, vehicle longevity is enhanced.
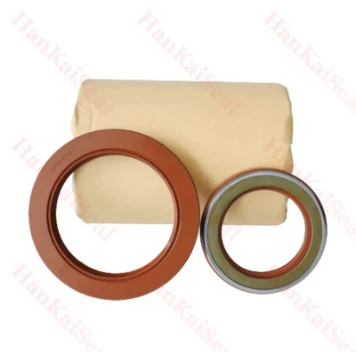
Oil seals are not one-size-fits-all. The specificity in design and material selection reflects their tailored approach to varying industrial requirements. For rotating shafts, seals are designed to handle both radial and axial loads, with materials ranging from nitrile rubber, offering excellent oil and temperature resistance, to polyacrylate and silicon, which provide superior heat resistance. Each material's properties have been scientifically researched and tested, ensuring they meet stringent industry standards.
oil seal for rotating shaft
In the realm of expertise, understanding the nuances of oil seal selection is pivotal. Engineers must consider factors such as shaft speed, operating temperature range, and pressure conditions. The appropriate seal reduces friction and wear on the shaft, significantly extending its life. Professionals in sectors such as automotive, aerospace, and manufacturing, where high precision and reliability are paramount, rely on in-depth knowledge of these seals to ensure optimal machinery performance.
From an authoritative perspective, leading manufacturers are continuously innovating. Advanced technologies, such as Finite Element Analysis (FEA), are employed to simulate conditions and optimize the design of oil seals. This commitment to cutting-edge solutions confirms the industry’s pursuit of excellence in seal performance. Companies at the forefront of seal technology provide extensive research data and field testing results, instilling confidence in their clients about product efficacy.
Trustworthiness in the context of oil seals isn't solely about product reliability; it's about sourcing from certified manufacturers who comply with international quality standards, such as ISO 9001. The assurance stems from rigorous testing processes that each product undergoes before market release. Engaging with suppliers who value transparency in these processes enhances trust and ensures users receive top-tier products.
In conclusion, oil seals for rotating shafts are indispensable in mechanical applications, offering sustainable and efficient performance. By combining experiential insights with professional expertise and adhering to authoritative standards, one can make informed choices that yield longevity and reliability. This, in turn, cultivates a trusting relationship between manufacturers, distributors, and end-users, guaranteeing machinery that operates seamlessly within its intended lifespan.