Oil seals, often referred to as rotary shaft seals, are essential components in pumps that prevent fluid leakage and exclude contaminants. Their functionality can make or break the efficient operation of machinery, highlighting the importance of choosing the right oil seal for your pump. As someone with years of experience in this field, I can attest to the significant difference a high-quality oil seal makes.
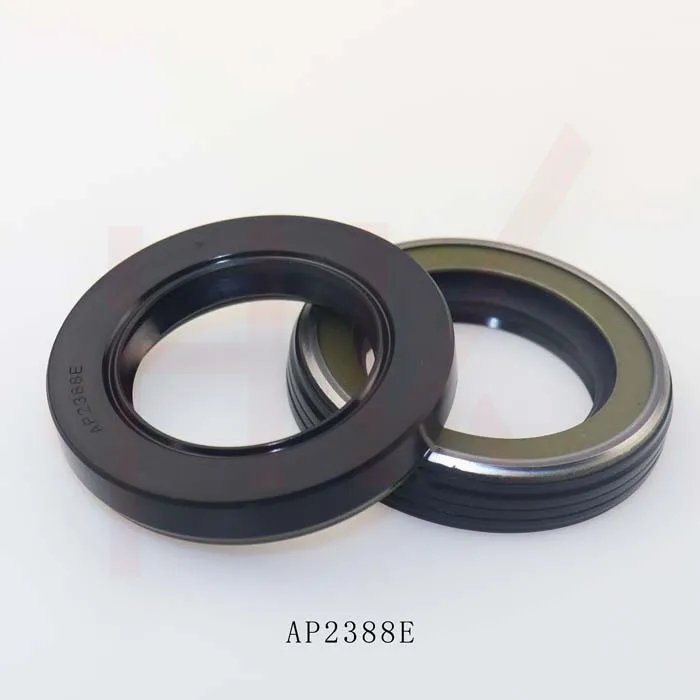
An oil seal operates primarily by sealing the rotating elements of the shaft, ensuring that lubrication is contained within the system while preventing external contaminants from entering. This is crucial for the longevity and efficiency of pumps, as any leakage or contamination can lead to equipment failure, increased maintenance costs, and operational downtime.
One of the fundamental aspects to consider when selecting an oil seal is the material. Oil seals are commonly made from nitrile rubber, which offers good resistance to oil and hydraulic fluids, and is suitable for temperatures ranging from -40 to 120 degrees Celsius. However, for more demanding applications—such as when the pump operates under extreme temperatures or in chemically aggressive environments—fluoroelastomer (FKM) oil seals might be preferred due to their superior resistance to heat and chemicals.
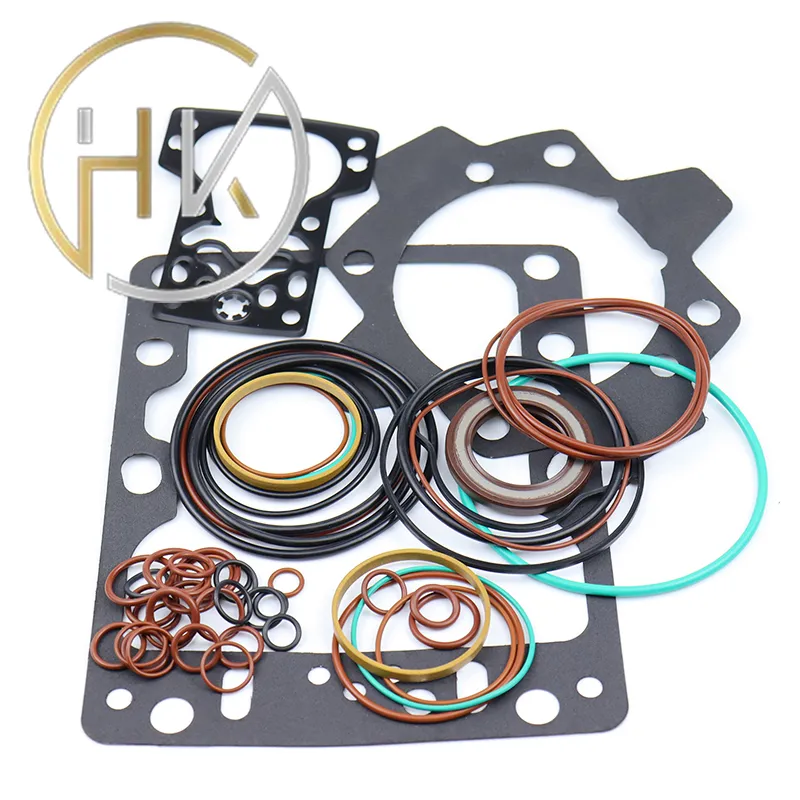
The design of the oil seal lip is another critical factor. Single-lip seals provide basic sealing against dirt and contaminants, suitable for simple applications. In contrast, double-lip or triple-lip seals offer enhanced protection, particularly in environments where dust or other particles are pervasive. A triple-lip design, for instance, provides a multi-barrier effect, significantly minimizing the risk of lubricant loss and contamination.
In our experience, the spring-loaded sealing edge is a feature that should not be overlooked. It maintains constant pressure against the shaft, compensating for minor misalignments and ensuring the seal remains effective even as the component wears. This feature is particularly beneficial in high-speed applications, where centrifugal forces could otherwise compromise sealing integrity.
oil seal for pump
Beyond the oil seal itself, the condition of the shaft on which it operates cannot be ignored. No matter how advanced or well-designed an oil seal is, if the shaft is not smooth or is out of tolerance, the seal’s effectiveness can be severely compromised. Regular inspections and maintenance are imperative to avoid rough or pitted shaft surfaces that could damage the seal lip.
Trust also plays a significant role in the selection of oil seals. Working with reputable manufacturers who comply with international standards—such as ISO and DIN—ensures not only quality but also reliability. This reduces the risks associated with premature failures and the need for frequent replacements, which can be particularly costly in industrial applications.
From personal experience, many industries now prefer to partner with specialists who not only supply oil seals but also provide comprehensive consultation based on the specific operational needs. This approach ensures the oil seal is not only fit for purpose but optimized for performance and longevity.
In summary, the careful selection of an oil seal for a pump involves understanding the specific operational environment and demands of your system. From choosing materials with the appropriate resistance properties, considering the mechanical design options, to ensuring compatibility with the shaft condition and partnering with trusted suppliers, each factor plays a crucial role in achieving optimal functionality and reliability.
Emphasizing these elements aligns with a proven strategy to maximize uptime, reduce costs, and enhance operational efficiency—core goals for any organization reliant on the seamless functioning of machinery. Use this information to make informed decisions and elevate the performance of your pumping systems with the right oil seals.