Selecting the right oil seal for a pump is crucial for ensuring optimal performance and longevity of the machinery. As a fundamental component, an oil seal plays a pivotal role in preventing the leakage of lubricants and the ingress of contaminants, which can significantly extend the life of a pump. This comprehensive guide explores the critical factors to consider when choosing an oil seal, the types available, and best practices based on real-world experience and authoritative expertise in the field of mechanical engineering.
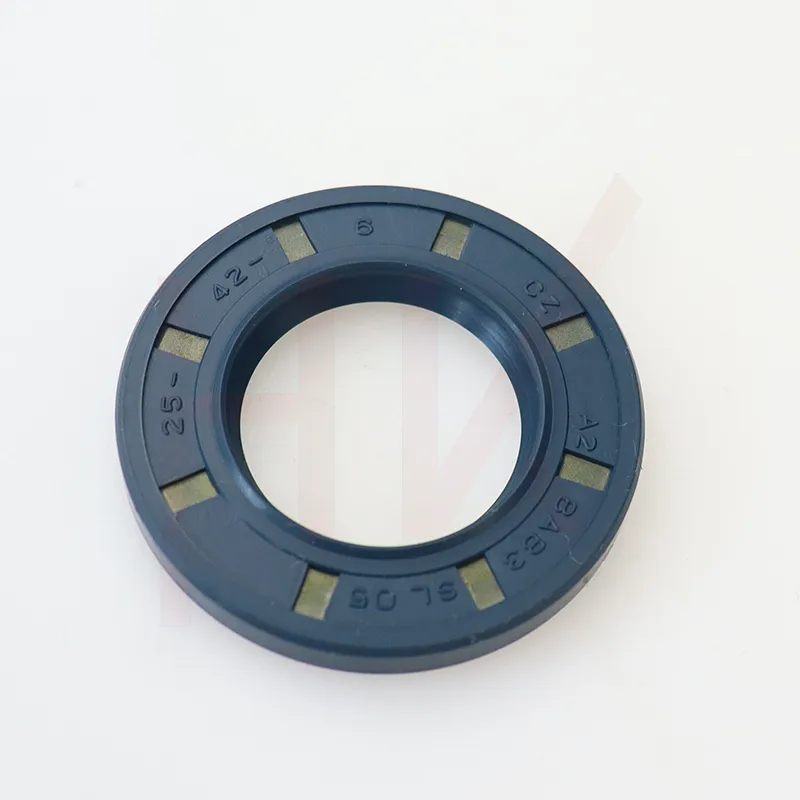
Understanding the role of oil seals in pumps, these devices are essential for maintaining the integrity of the lubricating system. They work by creating a barrier between moving and stationary components, thereby preventing leaks and reducing friction. This is especially important in pumps, where the movement of fluids or gases creates pressure that can easily lead to seal failure if not properly managed.
From the perspective of expertise, selecting an oil seal involves assessing several key characteristics. Material compatibility is paramount; the seal material must withstand the type of fluid used, operating temperature, and any potential chemical exposure. Common materials include nitrile rubber, silicone, and fluorocarbon, each offering distinct advantages. Nitrile, for example, is widely used due to its resistance to oils and affordable pricing. However, in high-temperature or aggressive chemical environments, fluorocarbon may be a better choice despite its higher cost.
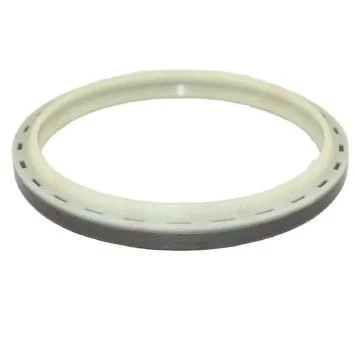
Adding to the trustworthiness of oil seal selection is the emphasis on correct sizing. An improperly sized seal can lead to either excessive friction or insufficient sealing, both of which can cause premature failure. Precise measurements of the shaft diameter, bore diameter, and seal width are essential. Advanced tools like calipers or even laser measurement devices are recommended for accuracy.
oil seal for pump
Exploring more on authoritativeness, one often-overlooked factor is the surface finish of the shaft. A smooth surface finish is essential for a good seal; too rough and it can cause rapid wear, too smooth and it may not seal adequately. It's recommended that the shaft's surface finish falls within 10 to 20 micro-inches. Consulting with pump manufacturers or experienced engineers can provide insights into the optimal surface preparation techniques.
Trustworthiness in application comes from following best installation practices. This includes ensuring the seal is installed in a clean environment to prevent contamination, using appropriate tools to avoid damage during insertion, and, if applicable, applying lubricant to facilitate installation. The importance of following manufacturer guidelines can’t be overstressed as these offer vital tips tailored to the specific seal model in use.
Finally, leveraging firsthand experience, routine inspection and maintenance of oil seals can prevent unforeseen failures. Regularly checking for signs of wear, such as hardening, cracking, or tearing, allows for proactive replacement before a major leak occurs. Implementing a scheduled maintenance plan, particularly in heavy-duty pump applications, enhances operational reliability and minimizes downtime.
In conclusion, choosing the right oil seal for a pump is more than just a selection process; it's a strategic approach to ensuring mechanical efficiency and durability. By combining real-world insights with technical expertise and authoritative guidelines, one can secure an effective sealing solution that offers long-term performance. This consideration not only optimizes the pump’s operation but also reinforces trust in the equipment’s dependability over time.