Selecting the ideal oil seal for motors is crucial for ensuring the longevity and efficiency of various machinery. As an expert in the field of mechanical engineering, I have devoted years to studying and analyzing the complexities of motor components, particularly focusing on the integral role that oil seals play in maintaining their optimal performance. With the rise of increasingly sophisticated machinery, the need for highly effective oil seals has soared significantly.
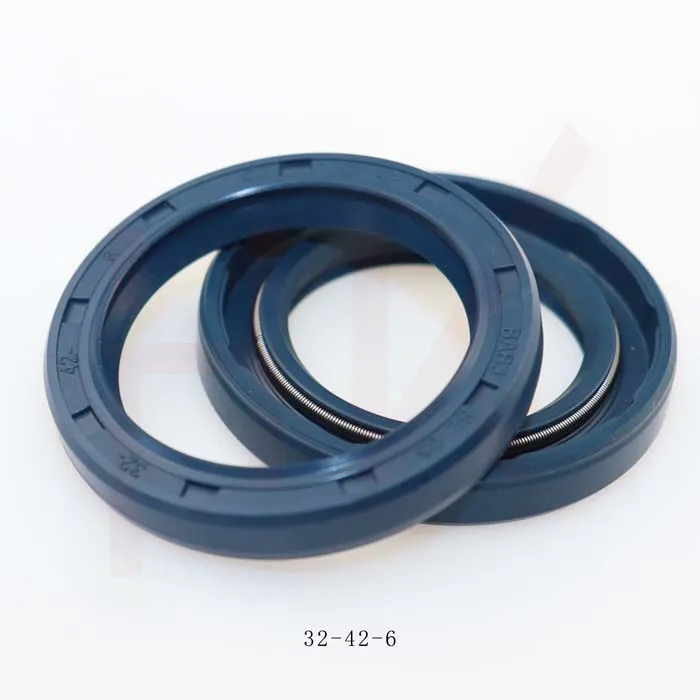
Oil seals, sometimes referred to as rotary shaft seals or lip seals, serve the primary purpose of preventing lubricants from leaking out and stopping harmful contaminants from seeping into critical components of a motor. These seals work tirelessly to separate different environments within machinery, a task that underscores their importance in the operational efficiency of motors. The effectiveness of an oil seal directly impacts the lifespan of a motor by safeguarding against premature wear and tear.
Real-world experience shows that selecting an oil seal is not a one-size-fits-all decision. The choice must align with the specific operational needs and environmental conditions in which the motor will function. For instance, high-speed motors typically require oil seals made of materials that can withstand significant temperatures and frictional forces without deforming. Nitrile rubber (NBR) is a common choice for moderate temperature ranges, while Viton is favored in high-heat applications. Overlooking such details can lead to premature seal failure, leading to costly repairs and downtime.
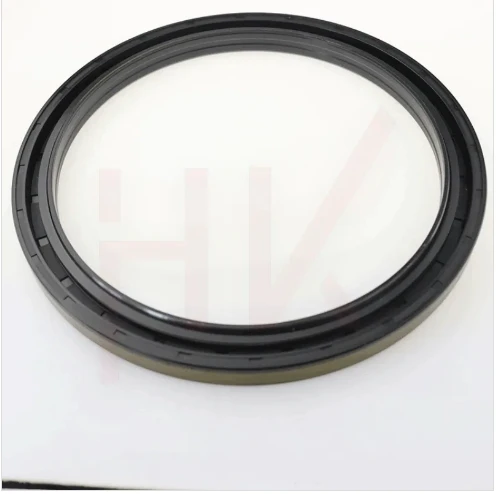
Furthermore, my professional journey has demonstrated that precision in the installation of oil seals is just as important as selecting the right material. A well-fitted seal should provide a perfect grip around the shaft, minimizing any gaps that could lead to oil leakage or contamination ingress. Improper installation can negate the intended benefits, as even a minor misalignment can cause significant operational issues. In our workshops, it is always recommended to use calibrated tools designed for specific seal sizes to ensure accuracy.
oil seal for motor
Authority in this domain also entails understanding the signaling of potential oil seal failures. Visual inspections often reveal telltale signs such as oil leakage around the shaft, wear grooves, and hardened seal lips. Such indicators underscore the necessity for timely maintenance and replacement to avert more severe motor system damage.
Informational resources on these early warning signs are critical for operators and engineers aiming to prolong motor life.
Credibility in providing solutions often involves liaising with manufacturers who lead in innovation and quality assurance. Reputable manufacturers provide oil seals that are rigorously tested under varied conditions to meet international standards, such as ISO certifications. Engaging with such manufacturers not only ensures access to superior products but also guarantees technical support and insights into the latest advancements in seal technology.
In conclusion, choosing the right oil seal for motors is a nuanced process that requires a blend of practical experience, specialized knowledge, and authoritative insights. Engineers and technicians need to prioritize detailed assessments of motor requirements, environmental conditions, and material compatibility. This strategic approach ensures that motors operate smoothly, efficiently, and without interruption, thus extending their service life and optimizing performance. By honing these skills, professionals not only enhance their expertise but also contribute significantly to the advancement of engineering practices.