Metric shaft seals play a crucial role in various industrial applications where precision and durability are paramount. These components are engineered to provide reliable sealing solutions in products ranging from automotive engines to large-scale industrial equipment. The effectiveness of a metric shaft seal can significantly influence the efficiency and lifespan of machinery, which is why it’s essential to choose the right type and specification for your specific needs.
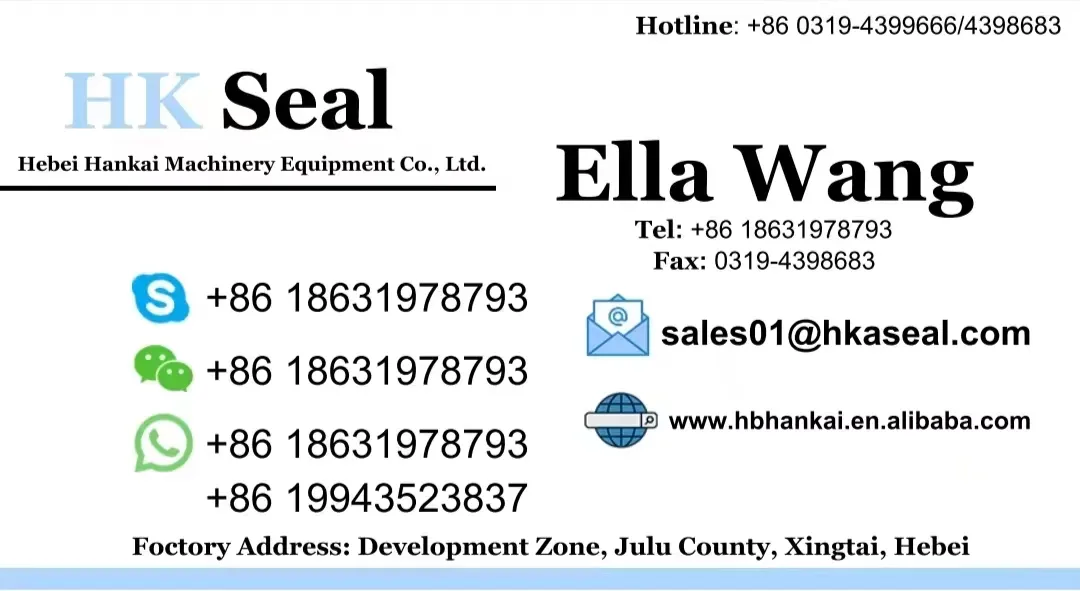
Professionals in the field recognize the importance of metric shaft seals in preventing leaks, contamination, and minimizing wear and tear on moving parts. For industries that operate under harsh conditions, such as chemical processing or heavy machinery, the selection of a high-quality seal is not merely a recommendation but a necessity. These seals maintain environmental integrity by preventing the ingress of contaminants and retaining lubricants, which is essential for maintaining the operational efficiency of machinery with rotating or reciprocating shafts.
A metric shaft seal's structure typically includes a rubber or elastomer component, a metallic insert for rigidity, and a garter spring to ensure constant radial shaft engagement. This composition enables the seal to accommodate various rotational speeds and temperatures, providing a robust solution for numerous applications. The expertise in selecting the right material—be it nitrile, silicone, or PTFE—plays a critical role in meeting the specific needs of different industries. For instance, seals made from nitrile are optimal for applications involving petroleum oils and water, whereas silicone is ideal for handling high temperatures and dry heat.
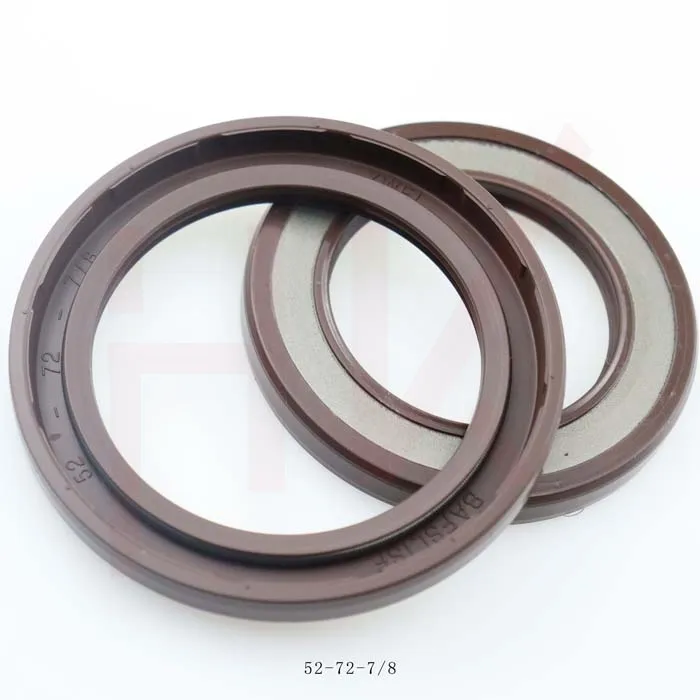
The authority in seal manufacturing comes from understanding the precise measurements required for achieving optimal performance.
Metric shaft seals are defined by their inner diameter, outer diameter, and width. Exact specifications ensure that the seal fits perfectly, reducing the risk of failure due to misalignment or improper fitting. Thus, engaging with manufacturers who can provide customized solutions ensures that each seal meets the strict demands of its operational environment.
metric shaft seals
Trustworthiness in seal performance is established through rigorous testing and adherence to industry standards. Quality suppliers conduct extensive testing on their seals to simulate real-world conditions, ensuring that each seal can withstand pressure variances, extreme temperatures, and chemical exposures. Certifications and compliance with international standards like ISO are indicators of a manufacturer's commitment to quality and reliability.
Real-world experiences from industry professionals underscore the critical nature of selecting appropriate metric shaft seals. Using inadequate or incorrect seals can result in mechanical failures, operational downtime, and increased maintenance costs. On the other hand, selecting high-quality seals contributes to operational efficiency, reduced maintenance interventions, and extended machinery lifespan. Companies that invest in premium metric seals often report higher ROI through improved equipment reliability and lower incidence of costly repairs.
In modern industrial landscapes, where machinery uptime and reliability are intertwined with business success, the choice of metric shaft seals is a vital consideration. This industry insight not only highlights the technical expertise required for selecting the right seal but also underscores the strategic importance these components play in broader business outcomes. Emphasizing experience, expertise, authoritativeness, and trustworthiness in metric shaft seal choices ensures that businesses maintain a competitive edge by optimizing their operational capabilities and safeguarding their investments.