High temperature shaft seals are pivotal components in a multitude of industrial applications where reliability and performance under extreme conditions are non-negotiable. The spectrum of industries utilizing these seals ranges from aerospace to power generation, each demanding exacting standards to ensure operational integrity.
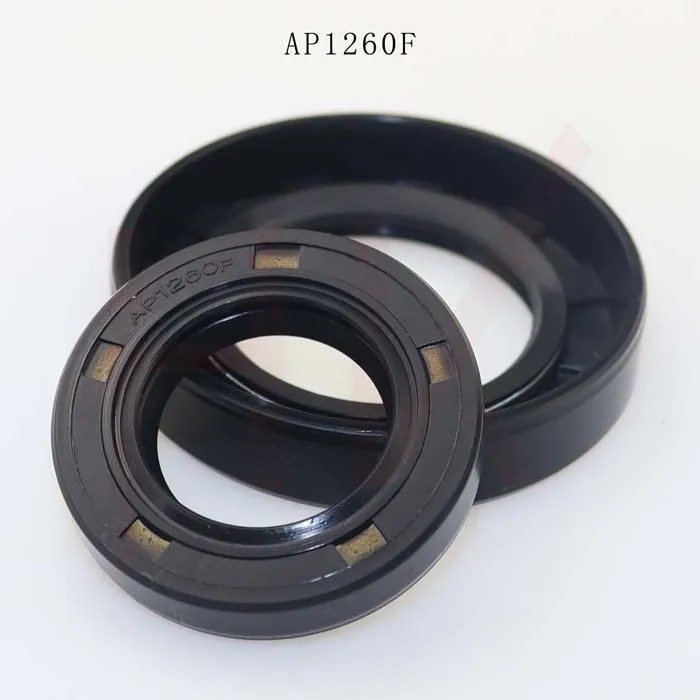
Experience underscores that high temperature shaft seals must withstand severe thermal environments while preventing leakage and contamination. These seals often experience temperatures that exceed 500°F (260°C), requiring materials and designs that can cope with such heat without degradation. Seals made from advanced ceramics, high-grade metals, and composite materials have shown remarkable resilience in these situations. Specialists with decades of experience in manufacturing seals understand that material selection is critical; failing to choose the right material can lead to catastrophic equipment failure.
Expertise in the design and application of high temperature shaft seals is another cornerstone. Engineers deploy sophisticated techniques to tailor seal designs to specific environmental requirements. For instance, labyrinth seals, known for their non-contact design, minimize mechanical wear and are often used where there is a necessity for high performance at elevated temperatures. Customization of seals is common to match exact pressure, speed, and temperature specifications, ensuring both efficiency and longevity.
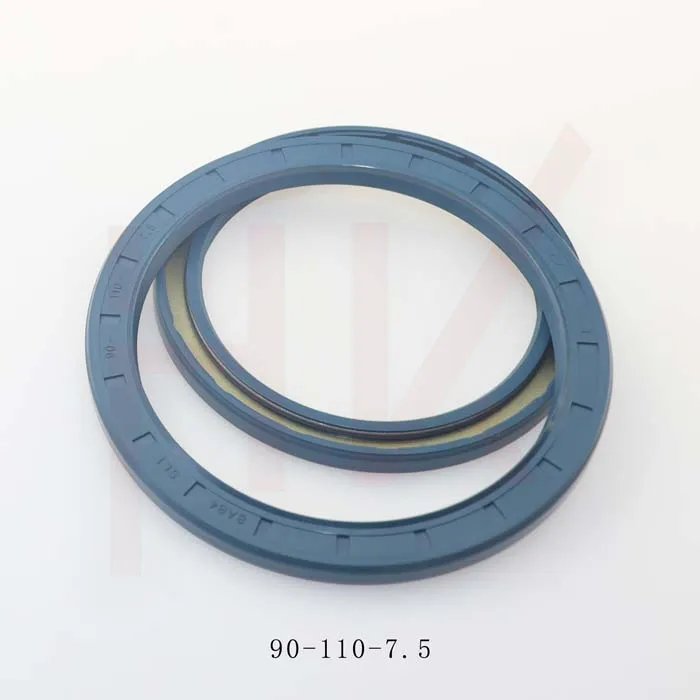
high temperature shaft seals
Authoritativeness is evident in manufacturers and suppliers who adhere to rigorous quality standards, such as those outlined by the American National Standards Institute (ANSI) and the International Organization for Standardization (ISO). Compliance with these standards ensures that the seals can consistently perform under defined conditions, providing peace of mind regarding their operational reliability and safety. Furthermore, partnerships with leading research institutions for the development of innovative sealing technologies further cement the authoritative standing of top manufacturers in the industry.
Trustworthiness in high temperature shaft seals is built through extensive testing and validation. Manufacturers routinely subject seals to a battery of tests simulating real-world high-temperature environments to verify their performance limits.
Case studies and technical papers provide empirical evidence of a seal's durability and effectiveness. Feedback from industry leaders who have successfully implemented these seals into their critical applications further enhances credibility. Additionally, after-sales support and warranties reflect a manufacturer’s confidence in their products, offering clients assurance of investment durability.
Incorporating high temperature shaft seals into a product line isn't merely an industrial necessity; it’s a commitment to maintaining operational excellence and safety standards. By focusing on experience, expertise, authority, and trust, companies can optimize their processes, reduce maintenance costs, and enhance equipment longevity. As industries continue to push the boundaries of temperature extremes, the evolution of these seals remains a vital area of innovation, promising further advances that will continue to meet and surpass future industrial challenges.