In industries where machinery operates at high temperatures, the functionality and longevity of equipment often hinge upon the smallest components. Among these, high temperature oil seals play a pivotal role in preserving the integrity and performance of machinery. These components are specifically designed to withstand extreme conditions while preventing leakage and contamination, ensuring seamless operational efficiency.
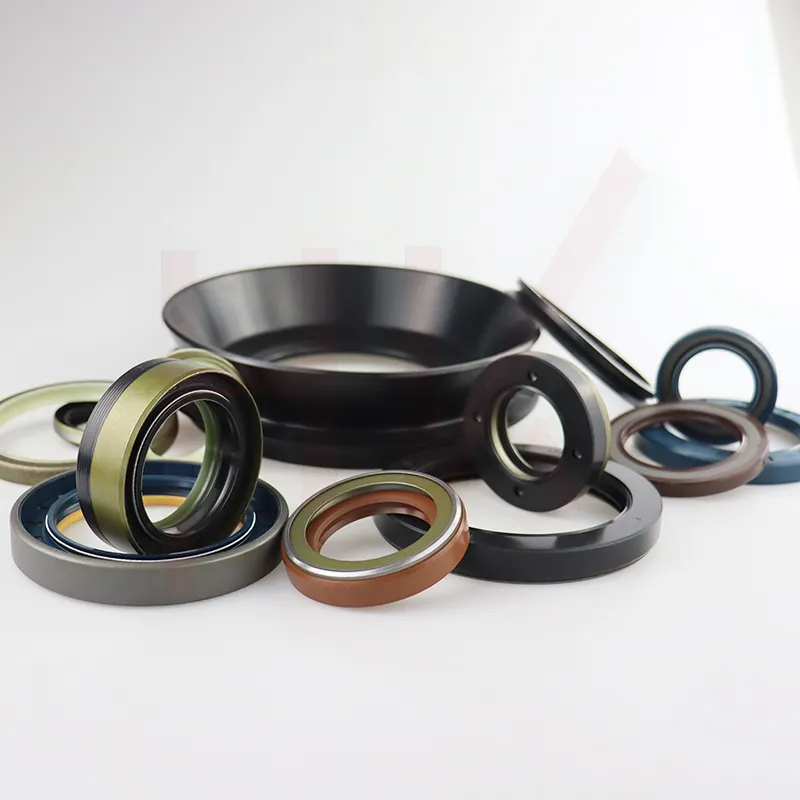
In many manufacturing environments, machines often face temperatures that can lead to premature degradation of seals. A high temperature oil seal is engineered to address these challenges, offering robust performance even in demanding conditions. Made from sophisticated materials such as fluorocarbon rubber (FKM) or silicone, these seals can endure temperatures ranging from -25°C to over 300°C, making them indispensable for sectors like aerospace, automotive, and heavy machinery.
One real-world testament to the effectiveness of high temperature oil seals comes from their use in automotive racing. In this realm, vehicles frequently operate at peak performance and high temperatures are a constant challenge. With conventional seals, there is a higher risk of oil leakage, which can have catastrophic effects not only on engine performance but also on safety. High temperature oil seals ensure that even under the most strenuous conditions, the engine remains protected, demonstrating their reliability and essential role in high-stakes environments.
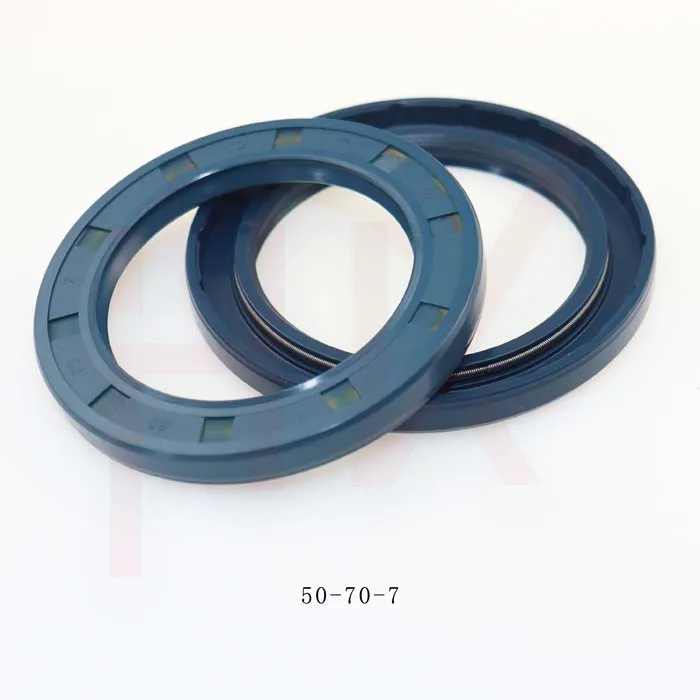
The expertise behind designing high temperature oil seals involves understanding the nuanced demands of heat and chemical exposure. Unlike standard seals, these are crafted with materials that resist thermal expansion and chemical breakdown, ensuring resilience over time. This is particularly crucial in industries where equipment downtime can result in significant financial losses. The choice of material is critical and often dictates the seal’s performance; thus, consulting with experts in seal technology can provide tailored solutions that align with specific industrial needs.
high temp oil seal
Authoritative knowledge in the field of high temperature seals is reflected in the advancements made by leading manufacturers. They continually invest in research and development to innovate seal designs that not only withstand higher temperatures but also offer improved durability and compatibility with various industrial fluids. By integrating cutting-edge technologies, these manufacturers set benchmarks in seal quality and performance, serving as trusted partners to industries worldwide.
Trustworthiness is paramount when selecting high temperature oil seals. Among the enticing claims of various products in the market, those backed by third-party testing and certifications offer a layer of assurance to buyers. Proven performance metrics and documented testing under simulated conditions provide the necessary confidence to industries that their selected seals will perform as expected. Moreover, customer testimonials and case studies can offer additional insights into the practical applications and experiences buyers have had with these essential components.
In summary, high temperature oil seals are not merely auxiliary items but are central to the optimal functioning of machines that operate under strenuous conditions. Investing in these specialized seals is not just a matter of purchasing a product, but committing to a standard of operational excellence and reliability. As industries continue to push the boundaries of temperature extremes, the demand for expertly crafted, authoritative seals that earn consumer trust will undoubtedly continue to grow. Selecting the right high temperature oil seal becomes a strategic decision, ensuring that equipment remains protected, efficient, and productive in any setting.