High temperature shaft seals often serve as the underappreciated heroes in industries characterized by extreme operating conditions. From aerospace to power generation, these seals ensure operational integrity by preventing leakage and contamination while maintaining pressure levels, even under the most demanding conditions.
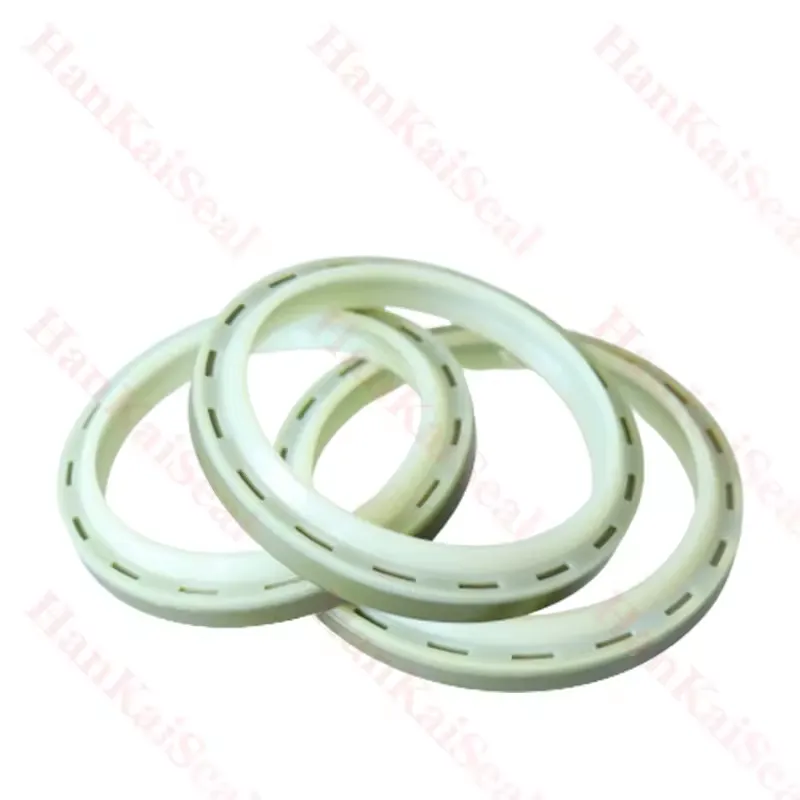
Drawing from years of industry experience, reliable high temperature shaft seals must balance durability with adaptability. They are engineered to withstand temperatures exceeding 500 degrees Celsius, a requirement in sectors where thermal resilience directly impacts safety and performance. The sophistication of these seals proves invaluable in protecting machinery from thermal stress and avoiding costly downtimes.
Expertise in materials science plays a pivotal role in crafting effective high-temperature seals. Advanced composites and alloys form the backbone of these seals, offering a mix of flexibility and thermal resistance. Notably, polytetrafluoroethylene (PTFE), graphite, and ceramics are frequently utilized for their exceptional thermal properties and resilience against corrosive environments. The integration of such materials ensures that seals maintain their shape and function, even when exposed to aggressive thermal cycles.
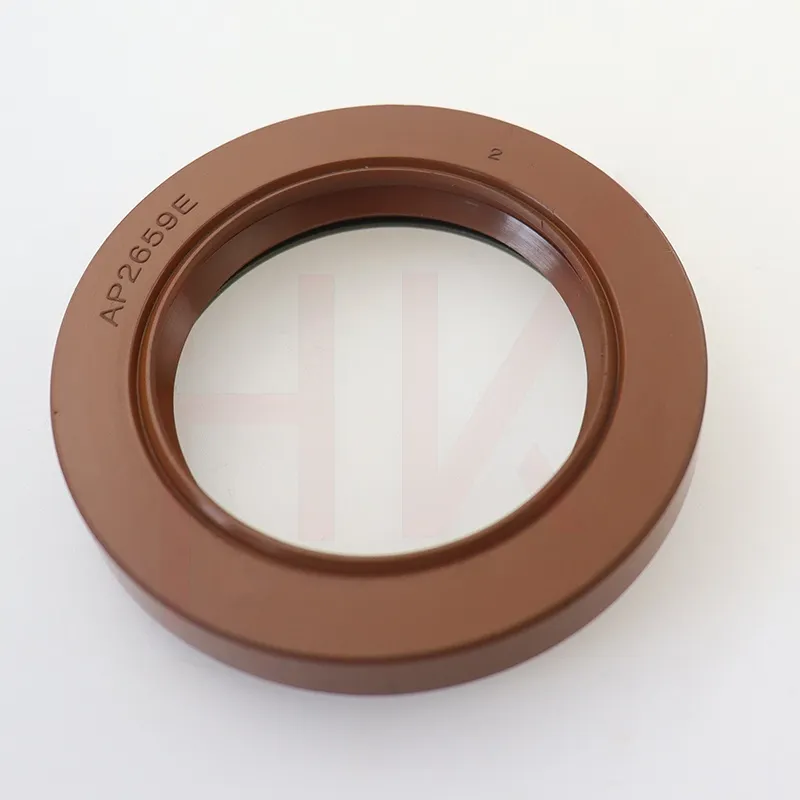
The authority of high temperature shaft seals is reinforced by rigorous testing and certification processes that establish their reliability and performance standards. Industry certifications, such as those from the American Society of Mechanical Engineers (ASME) or the International Organization for Standardization (ISO), are common benchmarks that facilitate trust among engineers and manufacturers. These certifications not only validate the material and design choices but also ensure compliance with safety and environmental regulations.
high temperature shaft seals
Trustworthiness, a fundamental aspect of any critical component, is paramount in the selection and usage of high temperature shaft seals. Trust is built through meticulous design backed by empirical testing. Computational fluid dynamics (CFD) and finite element analysis (FEA) are now integral to the design process, allowing engineers to predict seal performance under various thermal and mechanical stresses before actual deployment. Such predictive modeling ensures that only the most reliable seals reach the market, preserving industry trust and preventing operational failures.
From a product standpoint, the most effective high temperature shaft seals provide seamless integration with existing mechanical systems. They offer customizability in design, enabling tailored solutions for specific industrial applications. Comprehensive customer support and consultation services further foster user trust, ensuring that clients receive optimal sealing solutions tailored to their unique operational challenges.
As the industrial landscape continues to evolve with an increasing focus on energy efficiency and sustainability, the relevance of high temperature shaft seals only grows. They contribute to the substantial reduction of energy loss through leakage, enhancing the overall efficiency of machinery and reducing environmental impact.
By focusing on experience, expertise, authoritativeness, and trustworthiness in developing high temperature shaft seals, manufacturers not only deliver essential components but also ensure continued innovation and reliability within industrial sectors. As industries face ever-growing challenges posed by high temperature operations, shaft seals will remain indispensable for maintaining mechanical integrity and operational excellence.