High pressure rotary shaft seals are vital components in modern mechanical applications, serving as the unsung heroes that ensure the optimal performance and longevity of machinery. The expertise required to select and use these seals effectively is vast, and understanding their nuances is essential for engineers and maintenance professionals across industries.
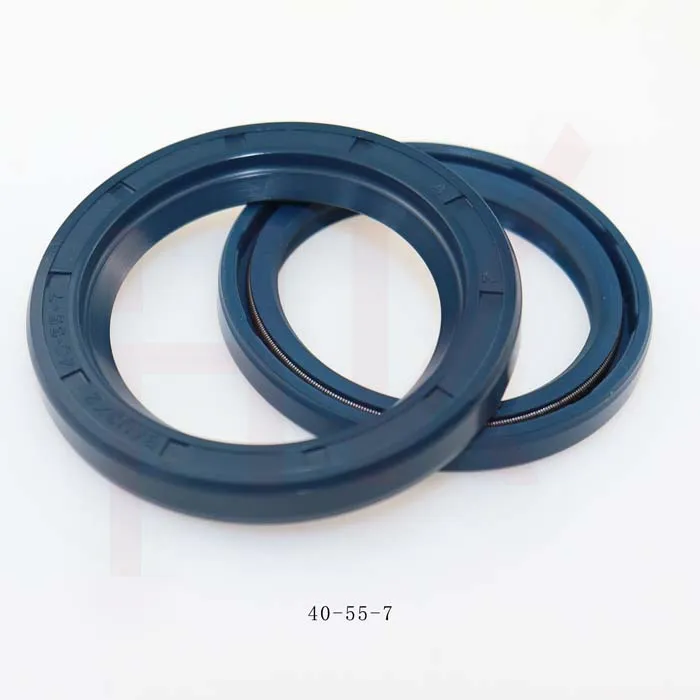
High-pressure environments present unique challenges, as they involve containing fluids or gases within systems that operate under demanding conditions. The rotary shaft seal's primary purpose in these settings is to prevent leakage, ensure lubricant retention, and protect against external contaminants, all of which are crucial for the efficient functioning of industrial machinery. These seals must withstand not just pressure, but also a range of temperatures and speeds, making material selection and design considerations paramount.
The materials used in manufacturing high pressure rotary shaft seals are selected based on their ability to perform under severe conditions. Common materials include advanced elastomers, PTFE composites, and metallic components that provide the strength needed to maintain seal integrity. The choice of material often hinges on the specific operational environment - for instance, seals operating in oil and gas sectors require different properties than those in pharmaceutical or food production facilities.
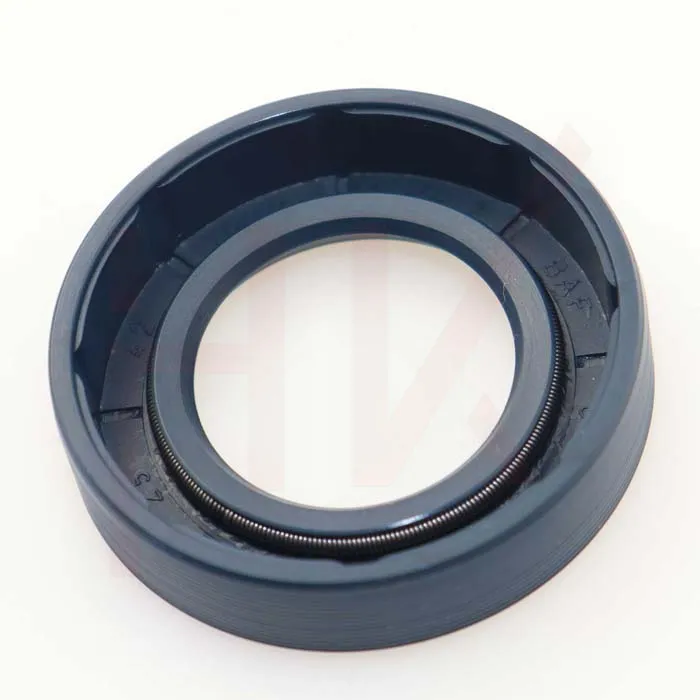
In terms of design, high pressure seals often incorporate advanced features such as multiple sealing lips, wave springs, and garter springs to improve sealing efficiency and accommodate shaft misalignment. These features are crucial for maintaining seal integrity over time and under varying operational loads.
Engineers must consider these design elements closely during the selection process to ensure compatibility with the specific application needs.
The expertise in selecting the right high pressure rotary shaft seal extends beyond just understanding the materials and design. Installation practices also play a critical role in the overall effectiveness and lifespan of these seals. Proper alignment, shaft finish, and housing dimensions directly impact seal performance. Experts recommend following meticulously defined installation protocols including lubrication application, use of specialized tools, and careful inspection during installation to avert premature failure.
high pressure rotary shaft seal
Continuous monitoring and maintenance are integral to the performance of high pressure rotary shaft seals. Routine checks to detect wear patterns and potential leakage can prevent more significant system failures and downtime. Experts often advocate implementing condition-based monitoring systems that utilize sensors and IoT integration to provide real-time insights into seal performance parameters, thereby enhancing maintenance regimes.
Trust in the performance of high pressure rotary shaft seals is established through rigorous testing and quality assurance by manufacturers. Leading companies in this sector invest in extensive R&D to innovate seal technology, ensuring products meet or exceed industry standards. Certifications from recognized bodies and compliance with global regulatory requirements reinforce the credibility of the seal products in the market.
Moreover, reliable customer support and technical consultation from manufacturers and distributors bolster the trustworthiness factor. Customers benefit significantly from expert advice on customization options and troubleshooting, which further enhances the operational efficacy of seals under pressure.
Authoritativeness in high pressure rotary shaft seals is demonstrated by leading industry publications, case studies, and collaborative projects that highlight successful implementations across various applications. Sharing insights from these projects can serve as valuable educational resources for engineers and decision-makers looking to optimize their mechanical systems.
By focusing on experience, expertise, authoritativeness, and trustworthiness, industry professionals can ensure that high pressure rotary shaft seals not only meet their application requirements but also contribute significantly to the overall reliability and safety of their machinery. This comprehensive approach to understanding and utilizing these seals results in enhanced performance, reduced downtime, and ultimately, cost savings for businesses operating under high pressure scenarios.