Oil seals are crucial components in many automotive and industrial applications. They are used to prevent the leakage of oil and other fluids from machines and equipment, ensuring smooth operation and preventing damage. The importance of oil seals cannot be understated, as they play a critical role in maintaining the efficiency and longevity of various machinery.
Oil seals are typically made from a variety of materials, including rubber, silicone, and polytetrafluoroethylene (PTFE). These materials are chosen for their durability, flexibility, and resistance to heat and chemicals. The composition of an oil seal can vary depending on the specific application and operating conditions, with some seals being designed to withstand extreme temperatures or pressures.
In terms of performance, oil seals are rated based on their sealing effectiveness. A seal with a 70% rating, for example, is designed to prevent up to 70% of oil leakage, while a seal rated at 90% can prevent up to 90% of leakage. The higher the rating, the more effective the seal is at containing oil and other fluids.
Oil seals are commonly used in engines, gearboxes, hydraulic systems, and other machinery where oil or lubricants are present. They are typically installed in areas where rotating shafts or moving parts come into contact with fluids, creating a potential leak point They are typically installed in areas where rotating shafts or moving parts come into contact with fluids, creating a potential leak point
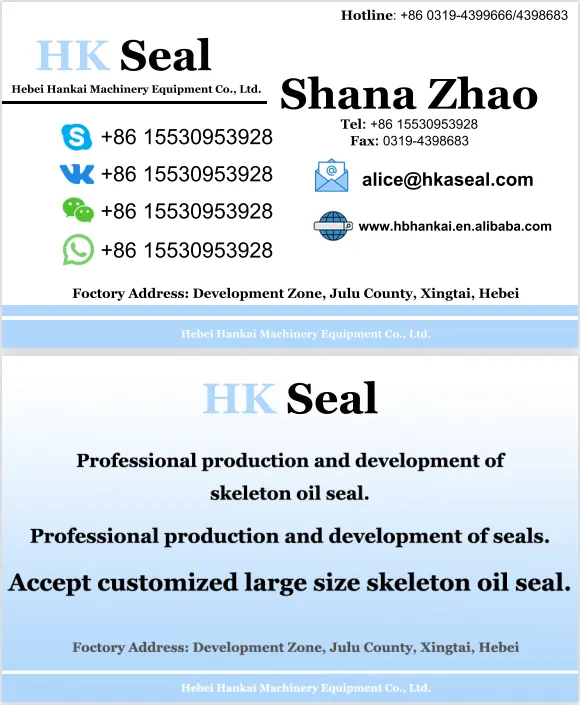
They are typically installed in areas where rotating shafts or moving parts come into contact with fluids, creating a potential leak point They are typically installed in areas where rotating shafts or moving parts come into contact with fluids, creating a potential leak point
70 90 10 oil seal. By sealing off these areas, oil seals help to maintain a consistent fluid level and prevent contamination or damage to the internal components.
Regular maintenance and inspection of oil seals are essential to ensure their proper function. Over time, seals can wear out or become damaged, leading to leaks and potential equipment failure. By monitoring the condition of oil seals and replacing them as needed, operators can avoid costly downtime and repairs.
In conclusion, oil seals are vital components in the smooth operation of machinery and equipment. With their ability to prevent oil leakage and maintain fluid levels, these seals play a critical role in ensuring the efficiency and longevity of various systems. By choosing the right seal material and rating for each application, operators can maximize the performance and reliability of their equipment. Regular maintenance and inspection of oil seals are essential to identify and address any issues before they escalate into major problems. Ultimately, investing in high-quality oil seals is key to protecting valuable assets and ensuring the continued success of industrial operations.