Rotary oil seals, also known as rotary shaft seals, are essential components used in machinery to prevent the leakage of fluids such as oil and grease. These seals are commonly found in rotating equipment such as turbines, pumps, motors, and gearboxes. They play a critical role in maintaining the efficiency and reliability of these machines by sealing the rotating shafts from contaminants and ensuring proper lubrication.
One of the key functions of rotary oil seals is to create a barrier between the internal components of a machine and the outside environment. This barrier prevents the entry of dust, dirt, water, and other contaminants that can cause abrasion, corrosion, and wear on the rotating shafts. By maintaining a clean and lubricated environment inside the machinery, rotary oil seals help to prolong the life of the equipment and reduce the need for costly repairs and downtime.
In addition to protecting against external contaminants, rotary oil seals also help to retain the lubricating fluid within the machinery. By forming a tight seal around the rotating shaft, these seals prevent the leakage of oil and grease, ensuring that the internal components remain properly lubricated and functioning smoothly. This is crucial for reducing friction, heat generation, and wear on the moving parts of the machine.
Rotary oil seals come in a variety of designs and materials to suit different applications and operating conditions
Rotary oil seals come in a variety of designs and materials to suit different applications and operating conditions
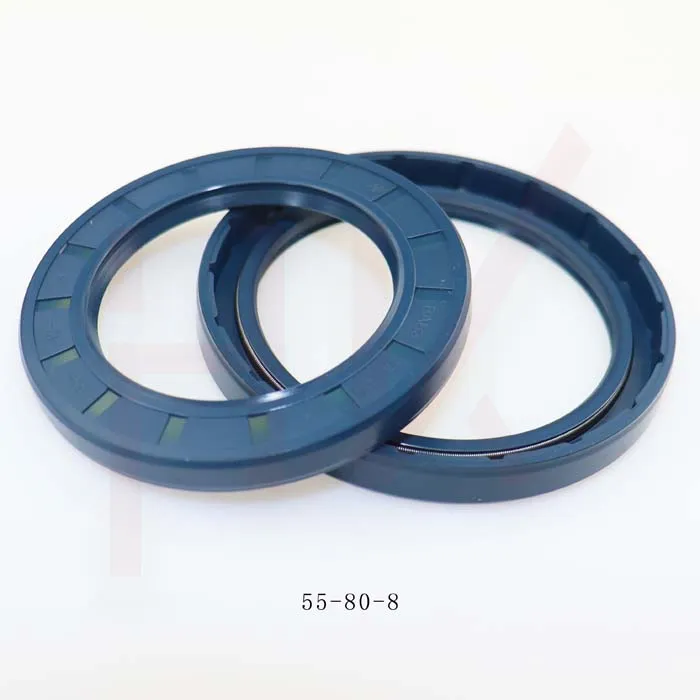
Rotary oil seals come in a variety of designs and materials to suit different applications and operating conditions
Rotary oil seals come in a variety of designs and materials to suit different applications and operating conditions
rotary oil seals. Common types of rotary seals include lip seals, labyrinth seals, and mechanical seals, each offering specific advantages in terms of sealing efficiency, durability, and resistance to high temperatures and pressures. The choice of seal depends on factors such as the speed of rotation, the type of fluid being sealed, and the temperature and pressure conditions of the operation.
Proper installation and maintenance of rotary oil seals are essential for ensuring their optimal performance and longevity. It is important to pay attention to the alignment of the seals, the cleanliness of the sealing surfaces, and the proper lubrication of the shafts to prevent premature wear and leakage. Regular inspections and replacement of worn seals are also necessary to prevent potential damage to the equipment and maintain its efficiency.
In conclusion, rotary oil seals are crucial components in machinery that help to protect against contamination, retain lubrication, and ensure the smooth operation of rotating equipment. By choosing the right type of seal and following proper installation and maintenance practices, manufacturers and operators can extend the service life of their machinery and avoid costly downtime. Investing in high-quality rotary oil seals is a wise decision for improving the reliability and performance of industrial equipment.