Understanding the intricacies of an oil seal, especially one with dimensions like 14x22x5, is essential for anyone in the field of mechanical engineering or maintenance. These components play a critical role in the efficient operation of machinery by preventing the leakage of lubricants and the ingress of contaminants. An oil seal with a specification of 14x22x5 refers to its crucial dimensions inner diameter, outer diameter, and thickness, respectively.
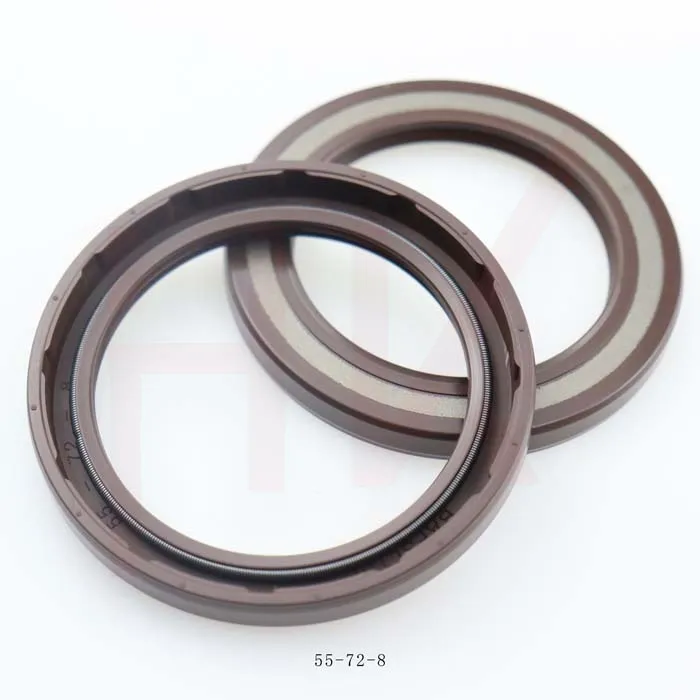
When it comes to real-world experience with oil seals of these dimensions, their application is vast. These seals fit snugly into small machinery or equipment that necessitates precision. For instance, compact engines, gearboxes, and pumps could utilize such a size. In practice, mechanics have noted that the compact nature of 14x22x5 oil seals demands precise installation to avoid premature wear or failure. Improper fitting could lead to oil leakage which jeopardizes machinery performance and longevity.
From an expertise standpoint, choosing the right material for a 14x22x5 oil seal can significantly impact its effectiveness. Common materials include nitrile rubber, silicone, and fluoroelastomer, each catering to different operational environments. Nitrile rubber is favored for its resistance to petroleum-based oils and moderate temperatures, making it suitable for automotive and industrial applications. On the other hand, silicone seals perform well under extreme temperature variations, while fluoroelastomers are known for their excellent chemical resistance, making them ideal for aggressive chemical environments.
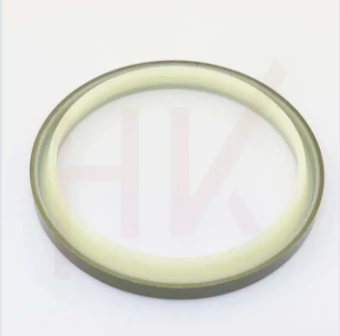
Furthermore,
the design of the lip in these oil seals is pivotal. A double lip design can offer enhanced protection by providing a backup sealing surface, which might be necessary in highly contaminated environments. This design consideration is central to establishing both trust and credibility in the maintenance and engineering communities, as it directly influences the longevity and reliability of equipment.
14x22x5 oil seal
When discussing the authoritative aspect of 14x22x5 oil seals, the support and information from credible manufacturers and suppliers are indispensable. Renowned brands often offer a wealth of technical data, including tolerance levels, recommended installation practices, and lifecycle expectations. These insights not only bolster the understanding of such components but also guide professionals in making informed decisions tailored to specific operational needs.
Establishing trustworthiness when discussing oil seals extends beyond just the product specifications. Authentic reviews and case studies from industry professionals who have implemented these seals provide a compelling narrative. For example, instances where the correct seal type significantly minimized downtime and maintenance costs become a testament to their utility. Professionals often share their recommendations on online forums and industry conferences—a practice that enriches communal knowledge and trust.
Additionally, factors such as proper storage and handling often get overlooked but are critical to maintaining seal integrity. Exposure to extreme conditions before installation can degrade the material properties, leading to seal failure. Hence, manufacturers' guidelines on storage conditions, such as avoiding direct sunlight and temperature extremes, are worth adhering to for optimal performance.
In summary, the 14x22x5 oil seal, though small, is a powerhouse in ensuring machinery efficiency and longevity. Its proper selection, installation, and maintenance are paramount and demand a thorough understanding of both material science and mechanical engineering principles. By leveraging expert insights and adhering to best practices, professionals can maximize the benefits and prolong the life of their machinery significantly. This attention to detail not only prevents costly downtimes but also champions a culture of reliability and excellence in industrial operations.