Hydraulic systems play a crucial role in numerous industries, from manufacturing to automotive, by converting energy into mechanical force. A vital component in these systems is the hydraulic seal, which ensures the efficiency and safety of hydraulic operations. However, frequent use and exposure to high pressures and temperatures can lead to wear and tear, necessitating repair. Understanding timely hydraulic seal repair not only maximizes operational efficiency but also prevents system failures that could lead to costly downtime.
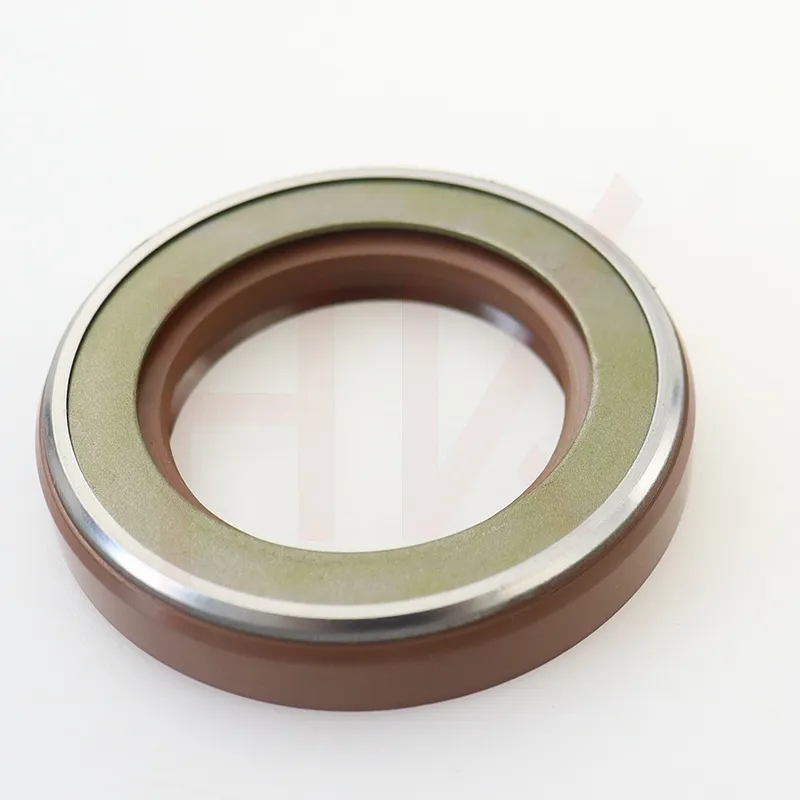
Expertise in hydraulic seal repair begins with a thorough assessment of the damage. Wear and tear on seals can occur due to various factors such as improper installation, high friction, and environmental exposure. A seasoned technician can identify early signs of seal damage, such as fluid leaks or decreased system performance. Early detection and repair are critical, as continued operation with damaged seals can exacerbate the issue, leading to more significant problems and expenses.
The repair process starts with the selection of the appropriate materials. Hydraulic seals are typically made of elastomers, PTFE, or polyurethane, each of which is suitable for different operational environments. Expertise in material science is essential to choose a seal that can withstand specific temperatures, pressures, and chemical exposures. Using the right material not only prolongs the lifespan of the seal but also enhances the overall system's efficiency.
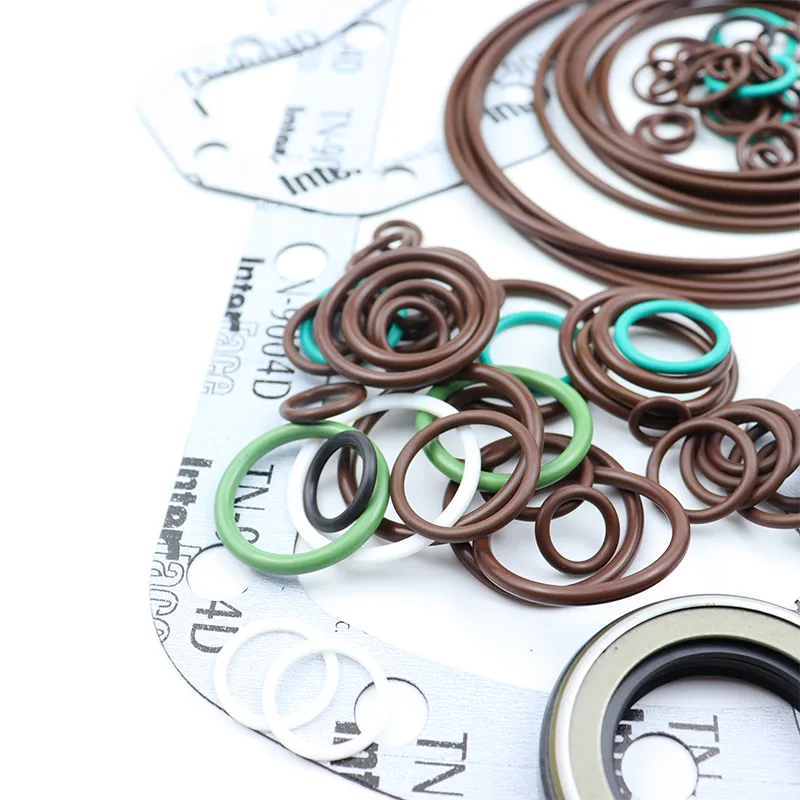
Precise installation is another critical factor in hydraulic seal repair. Even the best-quality seals can fail prematurely if not installed correctly. This requires expert understanding of hydraulic system schematics and the mechanical skill to follow precise installation protocols. Roundness, concentricity, and surface finish of the housing must align perfectly to ensure optimal seal performance. Technicians should utilize proper tools and techniques to avoid seal stretching, nicks, or other forms of damage during installation.
Hydraulic seal repair also requires reliance on advanced diagnostic tools to avoid trial-and-error methods. State-of-the-art tools, such as hydraulic analyzers and seal testing equipment, provide technicians with real-time data about the seal’s performance within the system. These tools help in accurate diagnosis and testing after repairs, ensuring that the system is restored to its optimal performance.
hydraulic seal repair
Authority in the field of hydraulic seal repair is established through continuous education and adherence to industry standards. Professionals in this domain should be well-versed with ISO and ASTM standards, which define the criteria for performance and safety in hydraulic systems. Mastery of these standards ensures repairs meet globally accepted guidelines, adding a significant layer of trustworthiness to their service offerings.
To maintain trustworthiness, hydraulic seal repair businesses should provide transparent service processes and clear communication with clients. Detailed documentation of the repair process, from assessment to completion, helps in building customer confidence. Offering warranties and post-repair support further reinforces trust, indicating that the business stands behind its work.
For industrial operations relying on hydraulic systems, regular maintenance checks are indispensable. Scheduled maintenance minimizes the risk of unexpected downtimes and keeps the operations running smoothly. Companies should develop a maintenance schedule that includes routine inspections, timely repair, and component replacement, tailored to their specific operational demands.
In conclusion, hydraulic seal repair is a complex endeavor that requires a nuanced understanding of materials, precise execution, and adherence to industry standards. By emphasizing expertise, authoritative adherence to standards, and transparent operations, businesses can ensure that their hydraulic systems remain reliable and efficient. This approach not only preserves the longevity of the equipment but also builds lasting relationships with clients based on trust and quality service.