Hydraulic cylinders play a crucial role in the functionality of a wide array of machinery, from heavy-duty industrial equipment to agricultural tools. As versatile components, they are subjected to rigorous operational demands, which inevitably leads to wear and tear over time.
One critical component in ensuring the longevity and efficiency of hydraulic cylinders is the repair seals. These small yet mighty elements act as the guardians against leaks and maintain the optimal pressure within the system. Having comprehensive knowledge about hydraulic cylinder repair seals can save industries substantial costs and downtime.
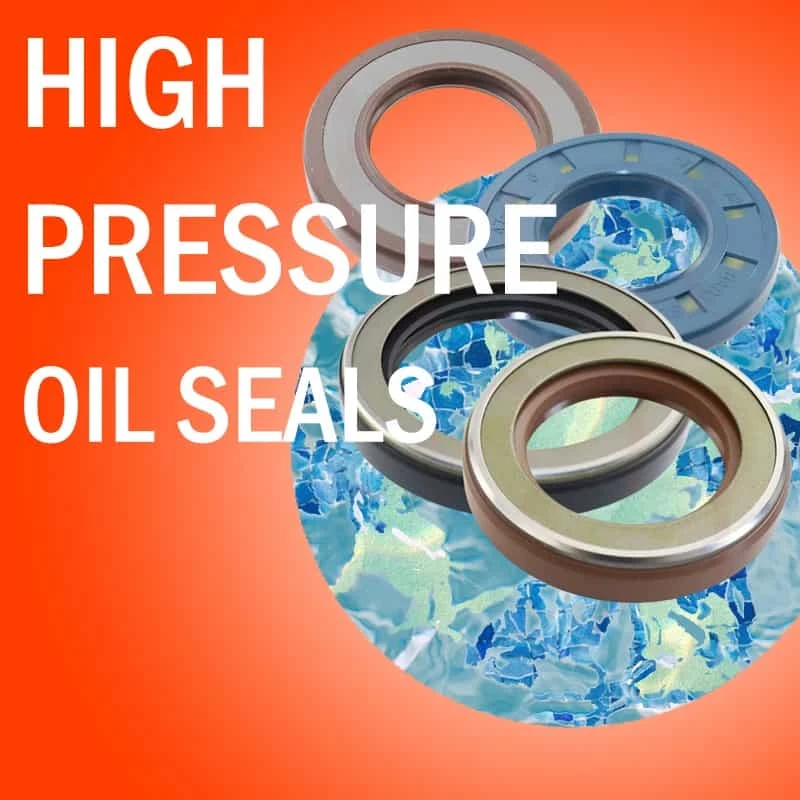
The primary function of hydraulic cylinder repair seals is to contain hydraulic fluids within the system while preventing contaminants from entering the cylinder. The seals create a barrier that keeps the internal environment controlled, ensuring the machinery functions without interruptions. There are diverse types of seals used in hydraulic systems, primarily including piston seals, rod seals, wipers, and buffer seals. Each type plays a distinct part in ensuring the dynamic and static efficiency of the system.
Piston seals, located between the piston and the cylinder bore, are pivotal in converting pressurized fluid energy into linear motion. These seals are essential in preventing fluid from bypassing the piston, hence maintaining the controlled direction of motion. Materials such as polyurethane, rubber, and PTFE are commonly employed for piston seals due to their resilience against high pressure and wear.
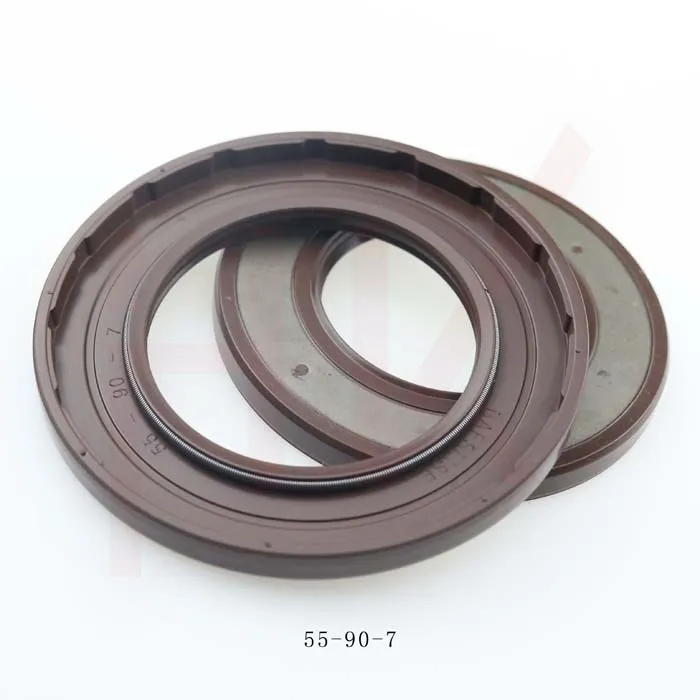
Rod seals serve the function of preventing fluid from leaking from within the cylinder to the external environment. Rod seals are typically positioned between the rod and the cylinder head, playing a vital role in fluid containment. The durability of rod seals is paramount as they frequently encounter friction and pressure fluctuations. Ensuring the correct installation and quality of materials like thermoplastic elastomers can enhance their longevity.
Wipers, or scrapers, though often overlooked, are pivotal in safeguarding the interior of the hydraulic system from external contamination. They scrape away debris and dust from the rod every time it retracts, maintaining the seal system's integrity. Materials like nitrile rubber or metal are prevalent choices due to their strength in harsh environments.
hydraulic cylinder repair seals
Buffer seals complement rod seals by absorbing fluctuations in pressure, ensuring the system remains stable even in extreme operational conditions. They act as the shock absorbers, preserving the functionality and lifespan of both the rod seals and the entire hydraulic system.
A meticulous approach to inspecting and maintaining these seals is imperative to prevent hydraulic cylinder failure. Scheduled maintenance should include regular inspections for any signs of wear like cracks, deformities, or material degradation. Replacing worn-out seals with high-quality replacements can prevent leakage and system inefficiencies.
Expertise in identifying the correct seal type and material is key to enhancing the performance of hydraulic systems. It is advisable to collaborate with seal manufacturers or hydraulic specialists who offer innovative seal designs tailored to specific machine requirements. Customization of materials to suit environmental challenges, such as temperature fluctuations or chemical exposure, can also significantly improve seal performance.
Investing in reliable and reputable sources for your hydraulic cylinder repair seals instills trust. Opting for seals that meet industry standards and certifications assures quality and durability. Emphasizing detailed documentation of seal replacements and system overhauls also augments the credibility and track record of machinery maintenance.
In conclusion, the importance of hydraulic cylinder repair seals goes beyond mere containment of hydraulic fluids. Their role in maintaining system integrity, efficiency, and longevity cannot be overstated. By understanding the varied types of seals and their specific functions, industries can make informed decisions resulting in minimized downtime and optimized machine performance. As industries continue to rely on hydraulic systems, the emphasis on high-quality seal maintenance stands as a testament to sustainable operational practices and economic prudence.