The versatility and reliability of metal-cased oil seals make them an essential component in a plethora of applications, ranging from automotive to industrial machinery. This article draws from a wealth of experience and expertise to explore the dynamic benefits, engineering nuances, and their role in safeguarding equipment efficiency.
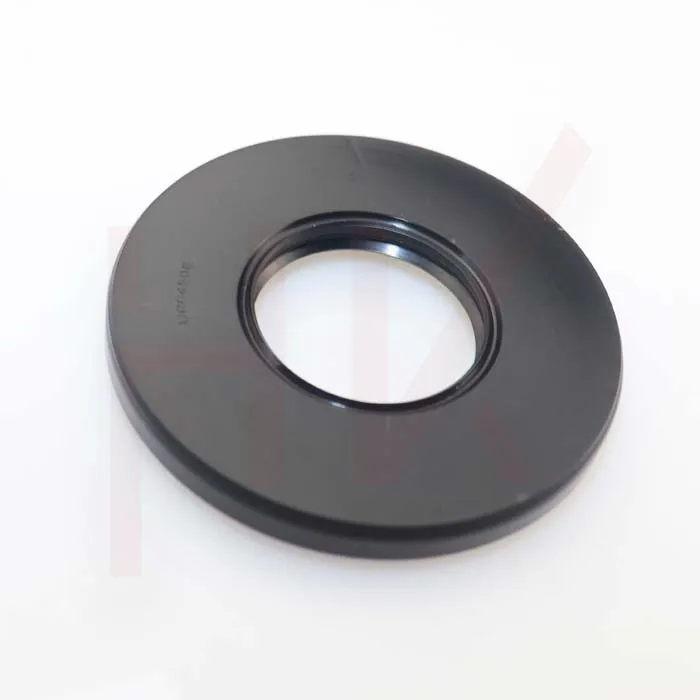
Engineered with precision, metal-cased oil seals boast a rugged construction that provides unparalleled protection against contaminants and fluid leakage. Specialists in the field leverage advanced metallurgy and elastomer technology, crafting seals that withstand extreme temperatures, pressures, and chemical exposures. This technological synergy ensures that each seal delivers optimal performance in even the most demanding conditions.
Drawing upon decades of industry experience, engineers understand the critical role that the metal casing plays in enhancing the seal's durability. The metal case acts as a robust backbone, enabling the oil seal to maintain its shape and functionality under substantial mechanical stress. This attribute is particularly vital in applications such as heavy machinery and automotive engines, where performance under pressure is non-negotiable.
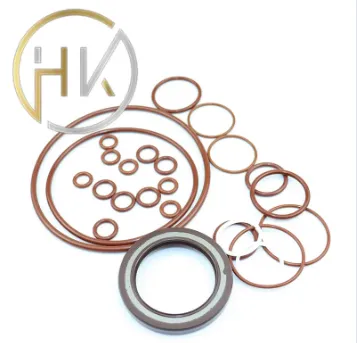
Authoritative knowledge in the field underscores the importance of material selection. The metal casing is often constructed from stainless steel or carbon steel, materials chosen for their strength, corrosion resistance, and thermal stability. Meanwhile, the sealing element, typically composed of nitrile rubber, fluorocarbon, or PTFE, ensures compatibility with a wide range of fluids, including oils, fuels, and hydraulic fluids. This thoughtful material pairing guarantees longevity, reducing maintenance costs and downtime.
metal cased oil seals
Trust in the efficacy of metal-cased oil seals stems from rigorous testing and industry standards adherence. Manufacturers conduct exhaustive assessments, replicating real-world stressors to ensure that seals perform flawlessly under specified conditions. This dedication to quality control bolsters user confidence, as equipment operators can depend on these seals to prevent costly leaks and environmental contamination.
Enhancing the appeal of metal-cased oil seals is their adaptability across various applications. Whether in automotive transmissions or industrial pumps, they are designed to fit seamlessly, maintaining fluid integrity and minimizing wear and tear. Additionally, their compatibility with automatic assembly processes enhances efficiency in high-volume manufacturing environments, a critical factor for original equipment manufacturers (OEMs).
The growing emphasis on sustainability further amplifies the relevance of high-quality oil seals. By preventing leaks, they contribute to a reduction in oil consumption and waste, aligning with broader environmental goals. Experts in the field predict a continuous evolution of seal technology, with innovations aimed at improving efficiency and reducing ecological impact, thus playing a crucial role in the transition towards greener industrial practices.
To sum up, metal-cased oil seals embody a blend of technical excellence and practical utility, making them indispensable in modern machinery. Their proven reliability and adaptability address the multifaceted challenges faced in equipment maintenance, delivering performance that industry professionals rely on. For businesses keen on optimizing machinery lifespan and operational efficiency, investing in high-quality metal-cased oil seals is a decision backed by expertise, authority, and unwavering trust.