Rotary oil seals, commonly referred to as rotary shaft seals, play a critical role in the optimal functioning of machinery by acting as a barrier between the moving parts and the static components of equipment. Understanding the nuances of these vital components not only showcases industry expertise but also bolsters trust and authority in maintenance and engineering domains.
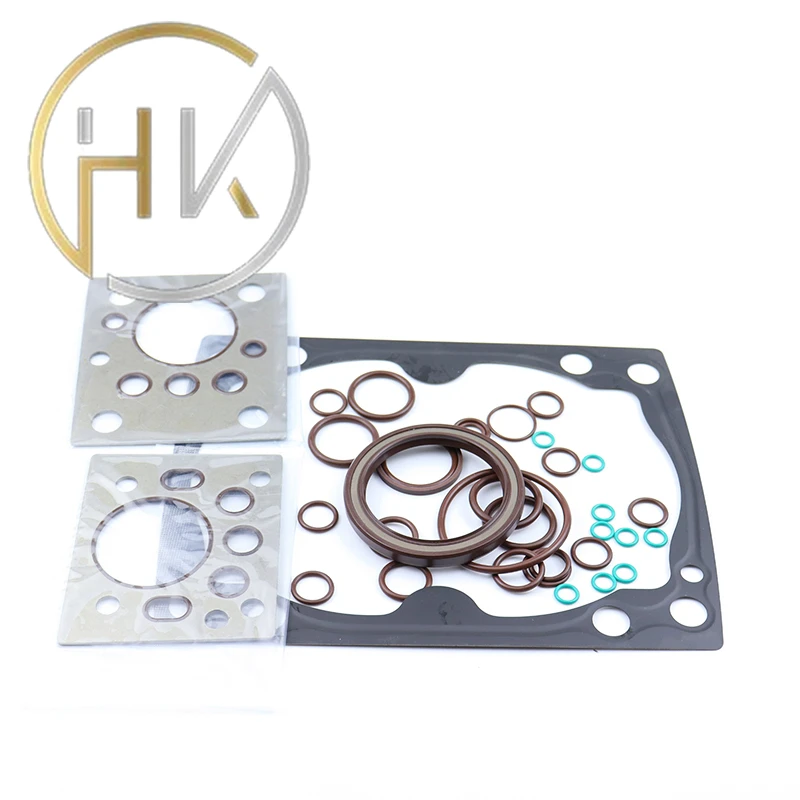
First-hand experience reveals that the selection of the appropriate rotary oil seal is paramount to the reduction of downtime and prolongation of equipment lifespan. Operators working in heavy-duty environments, such as automotive or manufacturing sectors, consistently emphasize the importance of oil seals in preventing leaks and protecting bearings from external contaminants like dirt and moisture. This reinforces the vital function rotary oil seals serve in maintaining the internal lubrication balance which is essential for the seamless operation of machinery.
From an expert perspective, the effectiveness of rotary oil seals can be primarily attributed to their robust design and material composition. These seals are generally constructed from durable elastomers such as nitrile rubber or fluorocarbon, materials known for their high resistance to temperature fluctuations and corrosive substances. Ingenious design features such as a garter spring further enhance their sealing capacity, ensuring a tight fit around the rotary shaft, thus mitigating the risk of premature failure.
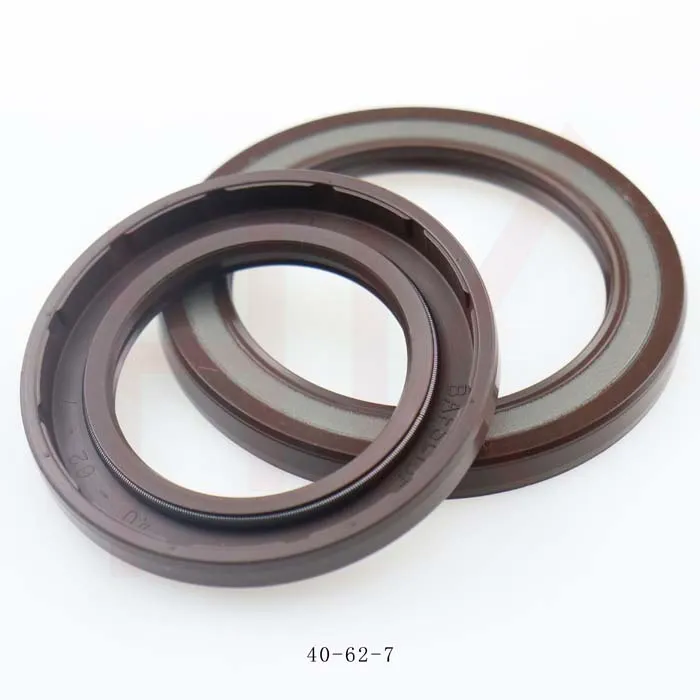
Industry authority on rotary oil seals is evident through the application of the latest technological advancements in their production.
Renowned manufacturers employ state-of-the-art design software to deliver seals with precise geometrical congruity and optimized lip load. Such precision engineering fortifies the seals’ performance in high-speed applications, allowing them to withstand not only the rotary motion but also axial displacement and misalignment.
rotary oil seals
Trustworthiness in delivering reliable rotary oil seals is demonstrated through rigorous testing protocols that these products undergo before market release. Reputed brands uphold stringent quality standards, conducting extensive fatigue and durability assessments to ensure that each seal meets the specified operational criteria. Additionally, endorsements and certifications from recognized industry bodies further attest to their reliability, providing consumers with assurance regarding their long-term performance.
The choice of a rotary oil seal requires a nuanced understanding of the operating environment to cater to specific application needs, be it in automatic transmissions or hydraulic systems. Technical consultation with seal experts can greatly aid in making informed decisions, thus enhancing operational efficiency and reducing maintenance costs. Establishing a reliable partnership with authoritative suppliers also facilitates access to upgraded sealing technologies and tailored solutions, pivotal for industries aiming to maintain a competitive edge.
Conclusively, the symbiosis of experience, technical expertise, authoritative endorsements, and an unwavering emphasis on quality establishes rotary oil seals as indispensable components, securing their role as guardians of machinery integrity and efficiency.