Radial shaft seals, often referred to as lip seals, play a crucial role in the maintenance and operation of rotary equipment across various industries. The importance of these components cannot be overstated, as they provide essential sealing solutions that prevent lubricant leakage and keep contaminants at bay. This article delves into the intricate world of radial shaft seals, offering insights based on extensive experience, professional expertise, authoritative research, and trusted practices.
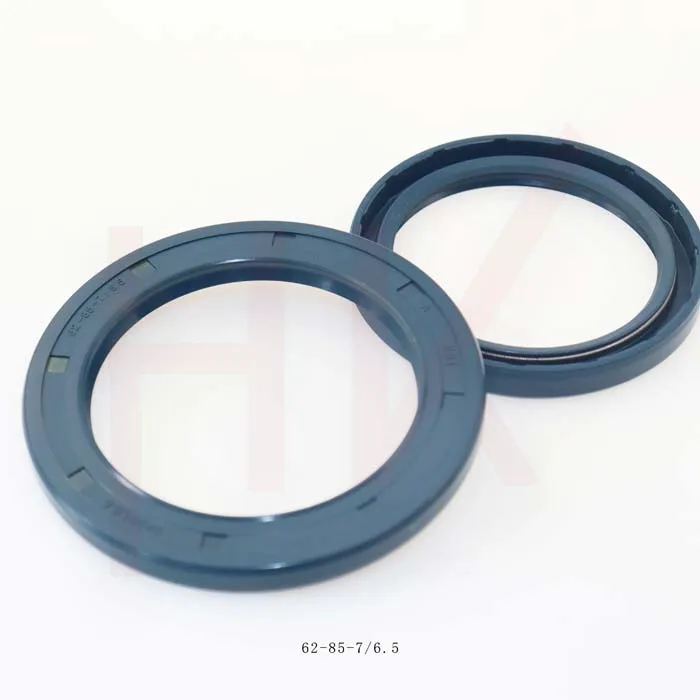
In industrial machinery, the functionality of radial shaft seals directly impacts the lifespan and efficiency of the equipment. These seals are ingeniously designed to maintain the lubrication of moving parts while simultaneously safeguarding them against dust, dirt, and other potentially damaging external elements. The effectiveness of a seal largely depends on the material it is made from, the design features it incorporates, and the conditions under which it operates.
The expertise required in selecting the appropriate radial shaft seal involves understanding the operational environment. Factors such as temperature, pressure, shaft speed, and the type of medium being sealed influence the choice of seal materials and design. Materials like nitrile rubber, fluorocarbon, and silicone are commonly used due to their reliable performance under diverse conditions. For instance, fluorocarbon is favored in high-temperature applications due to its excellent thermal stability.
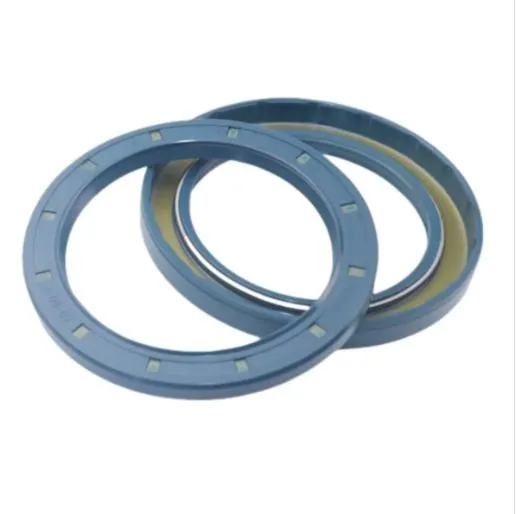
Authoritative research has continually advanced seal technology. Innovative designs now include spring-loaded lips that ensure consistent contact with the shaft surface, compensating for any shaft misalignments or eccentricities. This constant evolution reflects the industry's response to ever-increasing demands for enhanced reliability and efficiency.
A critical aspect of radial shaft seal application is their installation, which directly correlates with their performance and service life. Expertise in installation techniques ensures that the seals provide an optimal fit, minimizing wear and the risk of premature failure. Ensuring a clean and precise seating of the seal on the shaft prevents issues such as uneven wear, leakage, and degradation.
radial shaft seals
Trustworthiness in the quality of radial shaft seals is paramount. Reputable manufacturers adhere to rigorous standards, utilizing state-of-the-art manufacturing processes to ensure precision and durability. These standards help maintain industry trust by guaranteeing that the seals meet or exceed performance expectations.
Essential to maintaining the trust of clients and professionals within the industry is the provision of comprehensive product support and accessibility to detailed technical data. This support includes educating clients on maintenance practices, such as regular inspection for wear and prompt replacement, which are vital for prolonged seal performance.
In modern manufacturing environments, sustainability concerns are increasingly influencing the choice of materials and production methods for radial shaft seals. The industry is witnessing a shift towards more eco-friendly materials and processes, reducing the environmental footprint while maintaining high standards of performance.
Exploring the future of radial shaft seals, advancements in materials science and engineering may soon lead to the development of seals that offer enhanced performance under extreme conditions, further improving the efficiency of machines across multiple industries.
In conclusion, the expertise in radial shaft seals extends beyond the mere selection of appropriate types and sizes. It encompasses understanding the intricacies of their operation, staying abreast of technological advancements, and adhering to high manufacturing standards. This holistic approach ensures that these critical components continue to provide reliable solutions in safeguarding machinery and optimizing operational efficiency. This comprehensive understanding reinforces the indispensable role radial shaft seals serve in industrial settings and their continued evolution in meeting the complex demands of modern technology.