Cassette oil seals, an integral component in the mechanical and automotive industries, offer a unique blend of advanced engineering and practical utility. These devices are engineered to improve the longevity and efficiency of machinery by preventing the leakage of lubricants and the ingress of contaminants. Given their critical role, understanding the intricacies of cassette oil seals contributes significantly to the smooth operation of various systems.
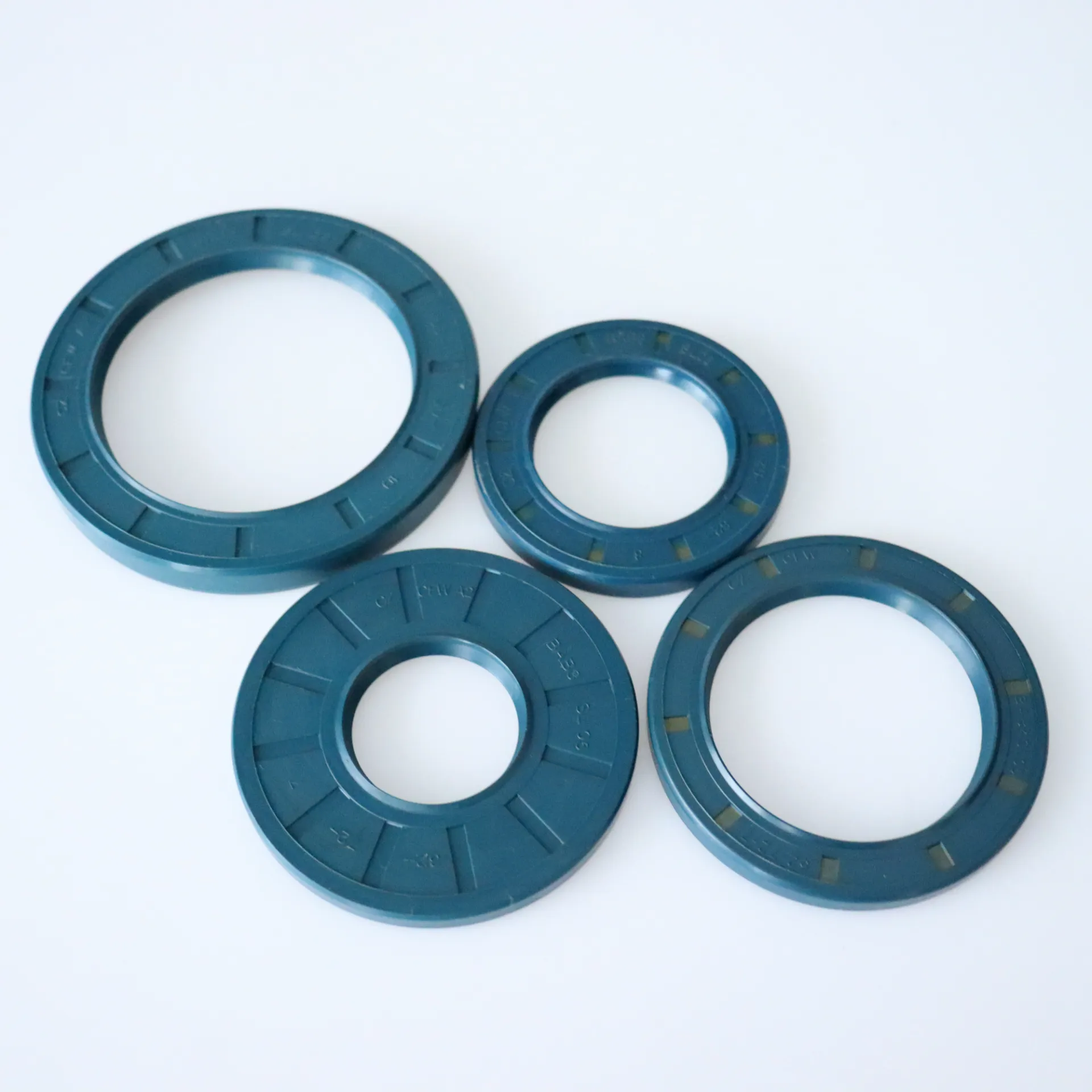
The unique construction of cassette oil seals differentiates them from traditional single-lip or multi-lip oil seals.
The design includes a sleeve over which a dynamic lip element is bonded. This configuration provides superior sealing capabilities under high pressure and in contaminated environments. The encapsulated design helps in shielding the sealing lip from external debris, a feature particularly valuable in off-road vehicles, construction equipment, and agricultural machinery.
Experience in diverse applications illustrates the robust performance of cassette oil seals in extending the lifespan of components subject to rigorous operating conditions. In heavy-duty trucks, for example, they maintain the integrity of wheel-end assemblies by withstanding heat, pressure, and contamination. Users have consistently reported reduced maintenance costs and downtime, affirming the reliability of cassette oil seals under real-world conditions.
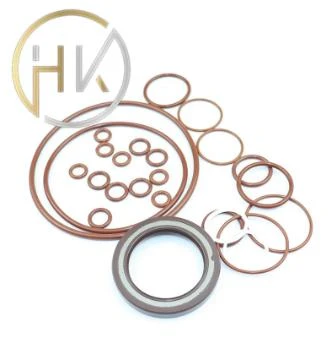
However, the performance of a cassette oil seal is heavily dependent on correct installation and application. Expertise in selecting the right seal involves a thorough understanding of the operational environment, including temperature ranges, rotational speeds, and exposure to contaminants. Manufacturers like SKF and NOK have developed sophisticated materials and designs to address these varied demands, yet the success of the application ultimately lies in matching the right product to specific operating conditions.
From an expertise standpoint, identifying the materials used in the construction of cassette oil seals is crucial. The materials must withstand friction, temperature variations, and chemical interactions. High-performance elastomers and fluorocarbon rubbers are commonly used for the lip material due to their excellent heat and chemical resistance properties. This aspect of material selection is critical as it impacts the seal's durability and effectiveness.
cassette oil seal
In terms of authoritativeness, the importance of adhering to industry standards cannot be overstated. Organizations such as the Society of Automotive Engineers (SAE) and the International Organization for Standardization (ISO) set rigorous benchmarks for the manufacturing and application of these seals. Compliance with these standards ensures that cassette oil seals meet the high demands of modern machinery and contribute to operational safety and efficiency. Engineers and procurement specialists should always verify that their chosen seals comply with relevant specifications to minimize risk and ensure optimal performance.
Cassette oil seals also play a significant role in sustainability efforts by supporting the efficient use of lubricants, thereby reducing environmental impact. By preventing leaks, these seals help in conserving oil resources and minimizing soil and water contamination. Industry leaders are continuously innovating to enhance the sustainable aspects of these components, considering the increasing emphasis on eco-friendly practices.
Trustworthiness in cassette oil seal applications can be assessed through rigorous testing and validation processes. Manufacturers typically conduct extensive laboratory simulations to evaluate performance under various conditions. Users benefit from this validation, as it assures them of the seal’s capability to function flawlessly over extended periods. Trust is further reinforced by the availability of warranties and technical support, allowing customers to make informed purchasing decisions confidently.
In conclusion, cassette oil seals embody a complex interplay of engineering precision, material science, and adherence to industry standards. Their design and application reflect an evolved understanding of mechanical efficiency and component longevity. As industries continue to demand higher performance from their machinery, cassette oil seals provide the reliability and effectiveness indispensable to meeting these challenges. An in-depth appreciation of these seals' construction and application solidifies their status as a cornerstone in the quest for operational excellence and sustainability.