The world of machinery and automotive maintenance thrives on the seamless functioning of various components. One essential part in this domain is the oil seal, notably the 70x90x10 oil seal. Understanding its role and ensuring its optimal use can significantly enhance equipment performance.
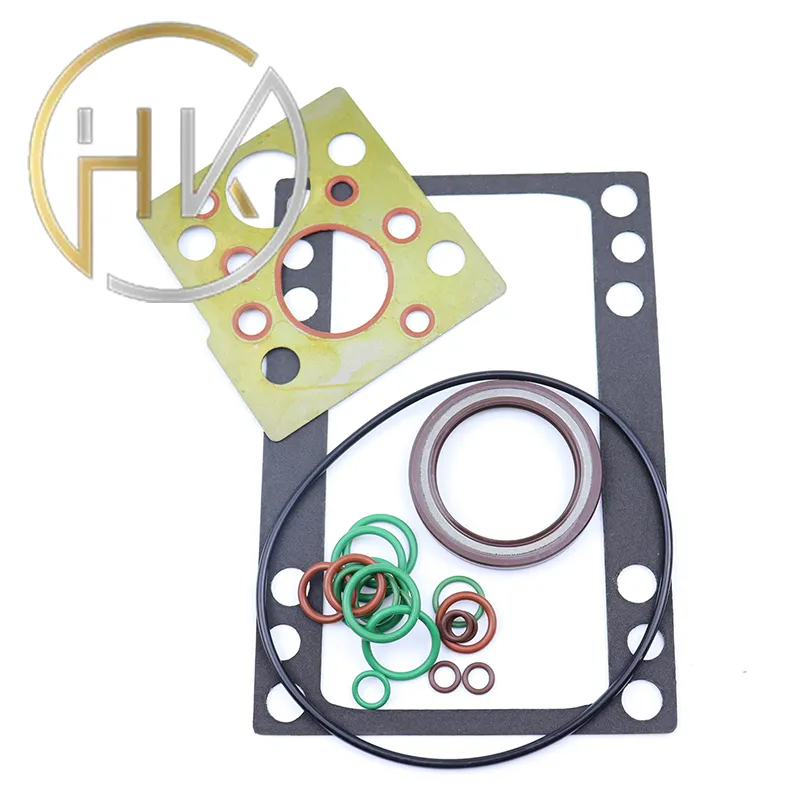
The 70x90x10 oil seal is fundamentally designed to protect machinery from contamination while maintaining optimal lubrication within components. The dimensions—70mm internal diameter, 90mm external diameter, and 10mm thickness—indicate its specific fit for various applications, ensuring a perfect match for seals required in numerous industrial settings.
Experience in mechanical maintenance highlights that utilizing the correct oil seal size is paramount. A mismatched seal can lead to oil leakage, contamination entry, and premature equipment wear. This specific seal size is frequently used in gearboxes, engines, and differentials, where it serves a critical role in sustaining fluid containment and dirt exclusion. Users have reported increased equipment longevity when proper seals are used, underscoring the importance of correct sizing.
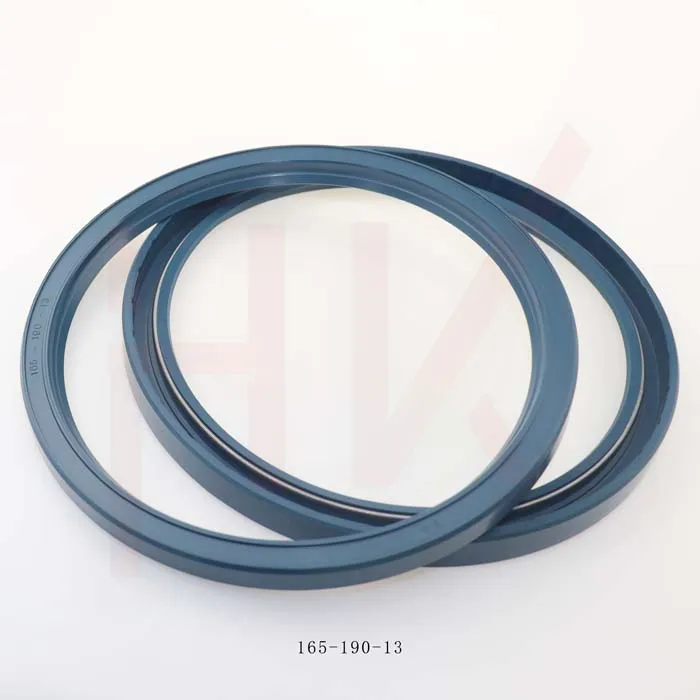
From a technical perspective, oil seals such as the 70x90x10 are engineered to perform under varying pressure conditions and temperatures. They are frequently crafted from materials like nitrile, fluorocarbon, or silicone, each offering unique benefits. For instance, nitrile is suitable for applications involving exposure to petroleum oils, while fluorocarbon is revered for its chemical resistance and high-temperature resilience. Selecting the appropriate material based on environmental conditions ensures optimal seal performance and longevity.
Professionals in the field stress the necessity of regular inspection and timely replacement of oil seals. Over time, even the best quality seals can degrade due to wear and tear. Regular checks can prevent unforeseen equipment failures. When replacing, it’s crucial to ensure that the seal is installed correctly. Improper installation can result in seal damage, rendering it ineffective. A precise fit during installation is required for maintaining the seal's efficacy.
70x90x10 oil seal
The expertise of seasoned mechanics reveals that a seemingly minute component like the 70x90x10 oil seal can profoundly impact an entire system's operational efficiency. They recommend sourcing from reputable manufacturers who adhere to rigorous quality standards. Quality assurance is vital; inferior seals can compromise machinery performance, leading to increased downtime and repair costs.
In terms of authority, manufacturers typically provide detailed specifications and guidelines for seal usage. Adhering to these recommendations, especially concerning installation torque and lubricant compatibility, guarantees better performance. Industry standards, such as ISO certifications, also assure that the seal meets certain performance criteria, providing added reassurance to purchasers.
Trustworthiness in the choice of oil seals cannot be overstated. A trusted supplier will offer not only high-grade products but also support services in terms of consultation and technical assistance. Engaging with suppliers known for their reliability gives consumers confidence in their machinery maintenance practices.
For those in the market to purchase, it’s advisable to consider additional factors such as the seal’s resistance to abrasion, compatibility with different lubricant types, and its flexibility to accommodate shaft misalignments. The long-term benefits of selecting the right oil seal extend beyond mere functionality—they include improved efficiency, reduced maintenance costs, and overall reliability of the machinery.
In conclusion, the 70x90x10 oil seal, while often overlooked, is a cornerstone for equipment reliability and performance. Through practical experience and professional insights, it’s clear that these seals play a pivotal role. By comprehensively understanding their function, selecting appropriate materials, and ensuring precision in application, users can achieve unparalleled machinery efficiency and longevity. The expertise shared by industry veterans only reinforces the critical nature of these components in maintaining industrial health and sustainability.