Navigating the world of machinery maintenance and repair requires understanding specialized components that make efficient operation possible. Among these critical components is the 40x52x7 oil seal, a small yet essential part that ensures the smooth functioning of equipment by preventing leakage and contamination. This article delves into the significance of the 40x52x7 oil seal, highlighting its practical applications, and contributions to machinery efficiency, and providing expert insights into its selection and maintenance.
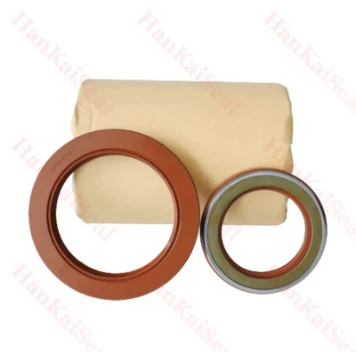
Understanding the 40x52x7 Oil Seal
Measured in millimeters, the dimensions 40x52x7 refer to the inner diameter, outer diameter, and thickness of the oil seal, respectively. This specific size is vital for compatibility with machinery where precision is crucial. The primary purpose of an oil seal is to protect bearings by keeping lubricant within the sealed area while preventing the intrusion of dirt and other contaminants. It safeguards the machinery by ensuring the internal lubricant remains uncontaminated, thereby enhancing the lifespan and performance of the equipment.
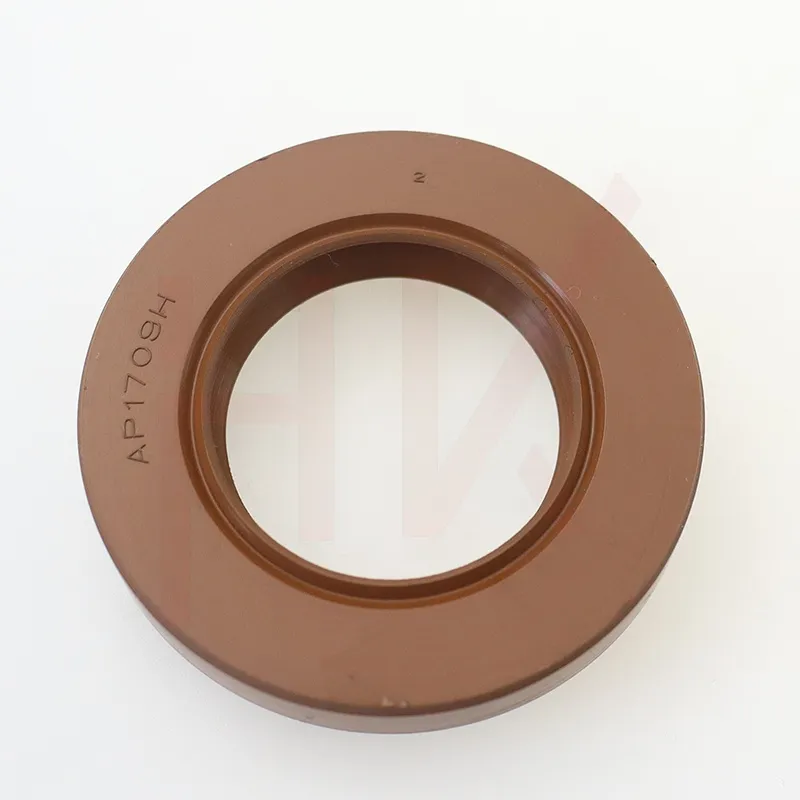
Applications Across Industries
The versatility of the 40x52x7 oil seal makes it indispensable across various industrial sectors. In automotive industries, these seals are essential for engines, transmissions, and axle systems, ensuring that oil does not leak from components, which could lead to mechanical failures. In the agricultural sector, heavy-duty machines such as tractors and harvesters rely on these seals to maintain hydraulic systems. Similarly, manufacturing and processing plants utilize oil seals to preserve the efficiency of their machinery, reducing downtime and maintenance costs.
Experience-Based Insights
Professionals across industries emphasize the importance of choosing the right oil seal to match specific applications. Incorrect seals can result in leaks, leading to equipment damage and increased operational costs. Experienced engineers recommend always checking the compatibility of the oil seal with the machinery specifications and the environmental conditions in which it will operate. Factors such as temperature, pressure, and exposure to chemicals can impact seal performance, making it essential to select materials and designs that match those criteria.
Expertise in Material Selection40x52x7 oil seal
Material selection is a critical expertise area when considering oil seals. Standard materials include nitrile rubber due to its excellent resistance to oil and wear. For applications exposed to higher temperatures or aggressive chemicals, fluorocarbon or silicone options are preferable due to their superior resistance to heat and chemical degradation. Understanding these material properties is key to extending the service life of oil seals and ensuring reliable performance under challenging conditions.
Ensuring Trustworthiness Through Maintenance
Regular maintenance contributes significantly to the effectiveness and reliability of oil seals. Inspecting seals at regular intervals for wear and tear, and replacing them as needed, can prevent unexpected machinery failures. Keeping the seals clean and ensuring that they are lubricated correctly extends their life and improves their sealing capability. Additionally, using trusted and quality-tested products from reputable manufacturers ensures that you are investing in seals that adhere to industry standards and regulations, thereby safeguarding equipment and operations.
Authoritative Insights
From a professional standpoint, choosing the correct 40x52x7 oil seal requires a combination of technical knowledge and practical experience. Industry experts advise consulting with manufacturers or suppliers who can provide detailed guidance based on specific operational requirements. Trusted manufacturers often have quality assurance systems in place, ensuring their products meet rigorous performance standards.
Conclusion
A 40x52x7 oil seal, although small, plays a significant role in maintaining the integrity and efficiency of machinery across numerous industries. Its selection requires careful consideration of size, material, and application specifics, backed by expert advice and reliable sourcing. Regular maintenance and quality assurance further enhance the reliability and functionality of these seals. By investing in the right oil seal, businesses can achieve better performance, reduce maintenance downtime, and ultimately, increase the longevity of their machinery.