Radial oil seals, a crucial component in machinery across various industries, play an indispensable role in preventing fluid leakage and contaminants from entering mechanical systems. These seals are expertly designed to fit around a rotating shaft, forming a tight barrier that retains lubricant within the assembly while impeding dirt and other particles from causing potential damage. Having spent over a decade in the field of mechanical engineering and specializing in fluid dynamics, I've encountered numerous situations where the efficacy of radial oil seals was paramount to operational success.
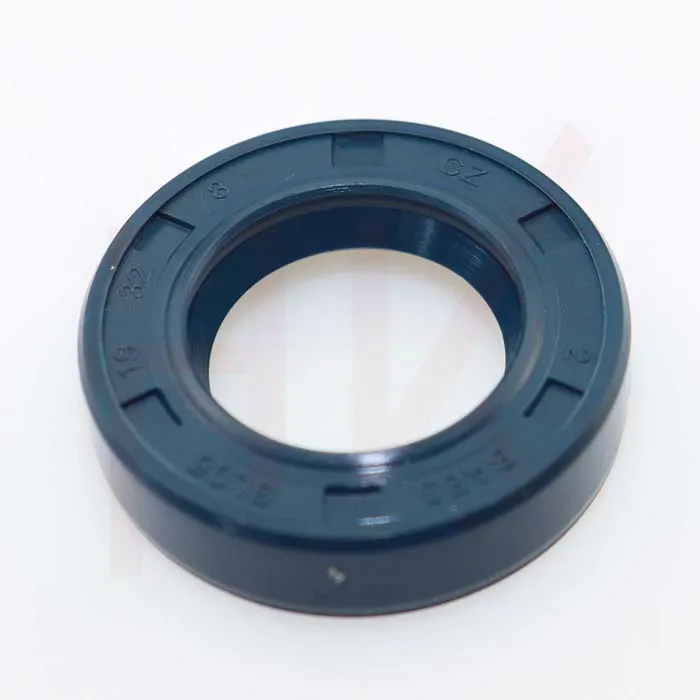
In my experience, choosing the right radial oil seal requires a nuanced understanding of the working environment. The material composition of the seal must be carefully selected based on factors such as operating temperature, pressure, and the specific chemicals in contact with the seal. For example, Nitrile rubber (NBR) is often the preferred choice for applications involving petroleum-based oils, owing to its excellent resistance to wear and durability. On the other hand, Viton (FKM) seals are recommended for high-temperature environments or applications dealing with aggressive chemicals.
One of the most critical aspects of ensuring the effectiveness of a radial oil seal is the installation process. Misalignment, over-tightening, or inappropriate lubrication during installation can drastically reduce the seal's lifespan, leading to premature wear or catastrophic seal failure. Through thorough training sessions and extensive field testing, I've found that using precision tools to align the seal with the shaft can significantly enhance its performance. Moreover, applying a thin film of compatible lubricant before installation helps to reduce initial friction, facilitating a smoother startup.
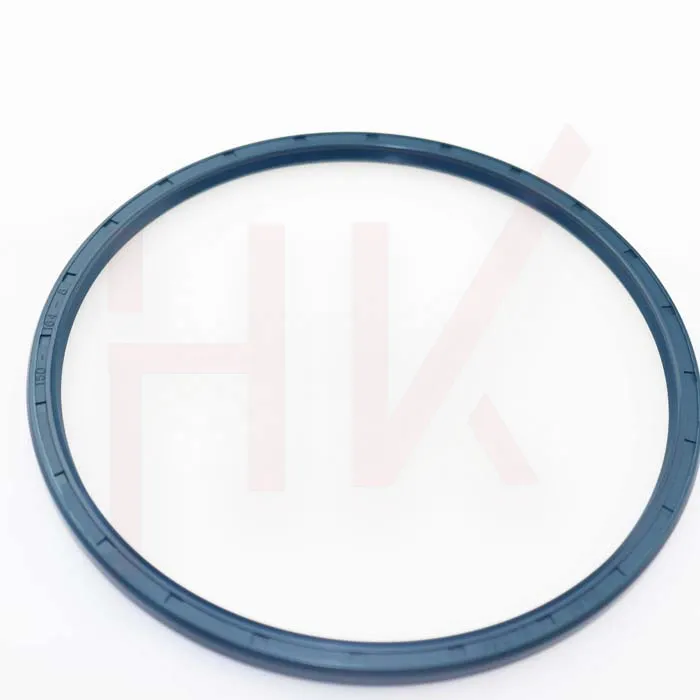
The performance of radial oil seals heavily depends on the shaft surface finish. An optimal surface finish directly correlates to the seal's ability to maintain a non-leaking barrier efficiently. The recommended surface finish for most seals varies between 10 to 20 micro-inches. A rough or uneven surface can accelerate wear and tear, prompting early seal degradation.
radial oil seal
As machinery becomes more advanced,
the demand for innovative sealing solutions grows. Manufacturers continue to develop seals with enhanced properties to withstand extreme environments. Recent advancements in material science have led to the introduction of hybrid seals that offer a combination of elastomeric flexibility and the robustness of thermoplastic materials. Such innovation not only boosts performance but also extends the service life of radial oil seals, contributing significantly to cost savings on maintenance and downtime.
The implementation of predictive maintenance strategies is another key factor in maximizing the utility of radial oil seals. Incorporating condition-based monitoring tools enables timely diagnosis of wear, allowing for preemptive seal replacements before failure. This proactive approach ensures continuous operation, minimizes unexpected breakdowns, and upholds the integrity of the entire mechanical system.
In conclusion, the expertise involved in selecting, installing, and maintaining radial oil seals underlines their critical role in bolstering industrial productivity and reliability. With advancements in technology and material sciences, today's radial oil seals are engineered to meet stringent operational demands, thereby offering enhanced protection and longevity. By leveraging expert insights and empirical data, businesses can ensure their equipment runs smoothly and effectively, maximizing both performance and profitability.