Understanding the critical differences between dust seals and oil seals is essential for engineers, mechanics, and anyone involved in machinery maintenance. Both these sealing components play vital roles in the function and longevity of mechanical systems, but they serve distinctly different purposes. Through experience and expertise, we delve into the nuances of these two types of seals and explore their significance in mechanical applications.
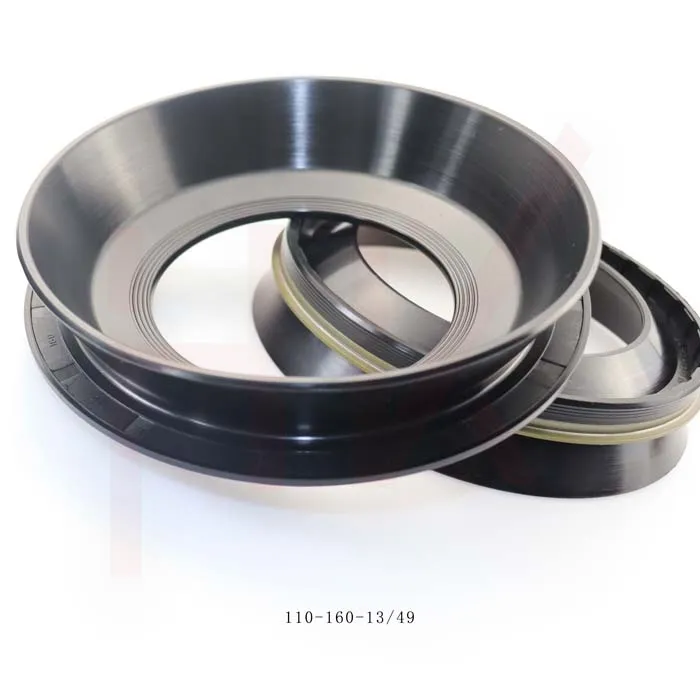
Dust seals are designed primarily to prevent contaminants like dust, dirt, and moisture from entering machinery. They are commonly used in environments where external particles can easily penetrate mechanical systems and cause wear and tear. Dust seals are integral to maintaining the cleanliness of the system, ensuring that the interior components remain free from abrasive materials that could lead to deterioration. In automobiles, for example, dust seals are widely utilized in shock absorbers and ball joints to maintain optimal performance and extend the lifespan of these components.
One key aspect that distinguishes dust seals from their counterparts is the material and design intricacies tailored to withstand dry particles. Generally, dust seals are made from flexible materials such as rubber or synthetics that can conform tightly to the surfaces they protect. The elasticity of these materials allows them to adapt to movement and vibration, ensuring a continuous barrier against environmental aggressors. Given their specific function, dust seals typically do not handle lubricants or operate under high pressure, which makes them unsuitable for applications that demand oil containment.
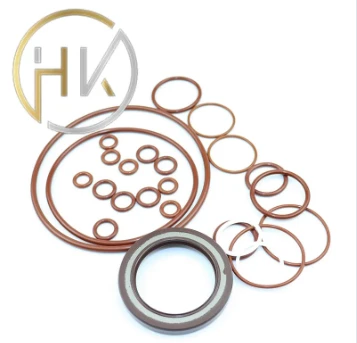
On the other hand, oil seals, sometimes referred to as rotary shaft seals or radial lip seals, are engineered to retain lubrication within the housing of an apparatus while preventing the leakage of lubricants like oils and greases. This is especially critical in systems such as engines, gearboxes, and pumps where maintaining lubrication is crucial to prevent overheating and reduce friction.
dust seal vs oil seal
Expertise reveals that oil seals must cope with higher internal pressures than dust seals, demanding robust construction and materials that can tolerate chemical erosion. Typically, oil seals incorporate a primary sealing lip, which rests against the rotating counterpart, often aided by a garter spring to maintain lip tension and ensure a tight seal. Reinforced materials like nitrile, silicone, fluoroelastomer, and polytetrafluoroethylene (PTFE) are commonly employed in oil seals for their excellent resistance to extreme temperatures and extensive wear and tear.
In terms of application, oil seals and dust seals can often be found working in tandem, especially in intricate machinery requiring comprehensive sealing solutions. An authoritative understanding of their integration is vital for ensuring that both contamination and lubrication retention are effectively addressed. Industries relying heavily on mechanical reliability, such as automotive, aerospace, and industrial manufacturing, benefit significantly from the combined use of these seals. By selecting the appropriate seal for each role, machinery can achieve optimal efficiency and reduced downtimes, fostering trust in consistent performance.
There’s a nuanced layer concerning the installation and maintenance aspects of dust and oil seals. Proper installation is imperative to function, as misalignment can lead to premature wear or failure, underscoring the importance of expertise in handling these components. Using the correct tools and adhering to manufacturer guidelines heightens their operational reliability. Furthermore, regular maintenance checks are crucial in identifying early signs of wear, such as cracks or hardening in dust seals and leaks or lip-separation in oil seals.
In conclusion, the choice between dust seals and oil seals should be guided by a comprehensive understanding of their distinct functionalities and material attributes. Meticulous selection and maintenance of these seals enhance machinery efficacy and device longevity, offering insights that mechanical experts have honed through years of hands-on experience. By leveraging expert knowledge, mechanical systems can be optimized for performance and durability, making these sealing solutions indispensable in safeguarding equipment integrity.