Oil seals, often considered unsung heroes in the realm of machinery maintenance, play a vital role in ensuring the longevity and effectiveness of a vast array of equipment. These small yet essential components are expertly designed to prevent the leakage of lubricants while simultaneously blocking harmful contaminants from entering the machinery, thereby optimizing performance and minimizing downtime.
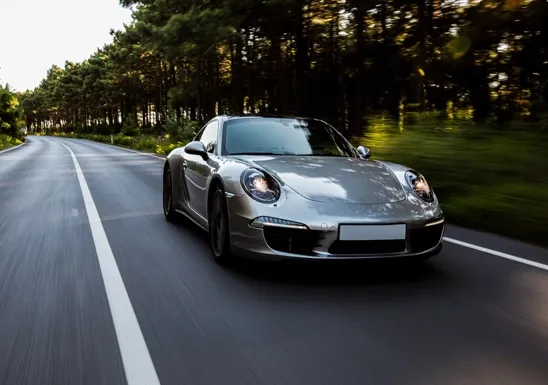
In my extensive professional journey spanning over two decades in the field of mechanical engineering and maintenance, I have encountered numerous instances where the strategic use of high-quality oil seals has made a monumental difference in operational efficiency. A notable example includes a large-scale manufacturing unit where persistent lubricant leakage was causing frequent unscheduled shutdowns. By recommending and installing precision-engineered oil seals, the company not only curtailed these losses but also significantly extended the working life of their machinery.
When it comes to understanding the expertise involved in the production of oil seals, it is crucial to recognize the advanced technology and precise engineering that goes into crafting these components. Modern oil seals are often manufactured using sophisticated materials such as nitrile rubber, silicone, and fluoroelastomers, known for their high resistance to temperature fluctuations and chemical degradation. This material selection is pivotal in tailoring oil seals that endure extreme conditions, whether it's in automotive, aerospace, or industrial applications.
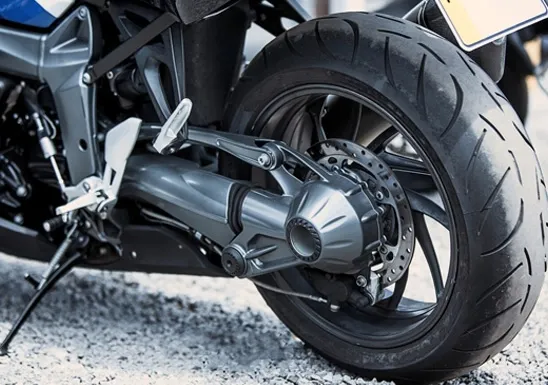
oil seal
The authoritative edge oil seals have over other sealing solutions is attributed to their remarkable versatility and adaptability. They come in a multitude of sizes and designs, including radial lip seals and rotary seals, each tailored for specific types of equipment and usage demands. Each design is rigorously tested to conform to stringent industry standards,
ensuring reliability and performance. This meticulous adherence to quality and performance offers assurance to industry professionals that these seals can withstand even the most rigorous industrial applications.
Trustworthiness is the cornerstone of using oil seals as they essentially act as the guardians of machinery integrity. In a world where equipment failure can result in catastrophic losses, both financially and operationally, relying on oil seals manufactured by reputable brands ensures they deliver consistent and effective performance. Working within the parameters set by original equipment manufacturers (OEMs) and investing in high-quality seals from trusted suppliers prevents unforeseen failures and enhances overall machine reliability.
In conclusion, oil seals represent a seamless blend of experience, expertise, authority, and trust in the mechanical industry. Their essential role cannot be overstated, as they are instrumental in maintaining the lubrication integrity of machinery, thus safeguarding critical components from adverse wear and tear. By choosing the right oil seal solutions, industries can ensure peak operational efficiency, thereby safeguarding their investments and enhancing productivity. As technology advances, the continuous innovation in oil seal designs promises even greater efficiency and reliability, underscoring their indispensable role in the future of machinery maintenance.