Achieving peak performance in industrial settings often requires reliable and efficient machinery. Among the critical components that ensure seamless operations in hydraulic systems are the hydraulic press seal kits. As the cornerstone of hydraulic press maintenance, these kits play a vital role in prolonging the life of machinery and enhancing performance.
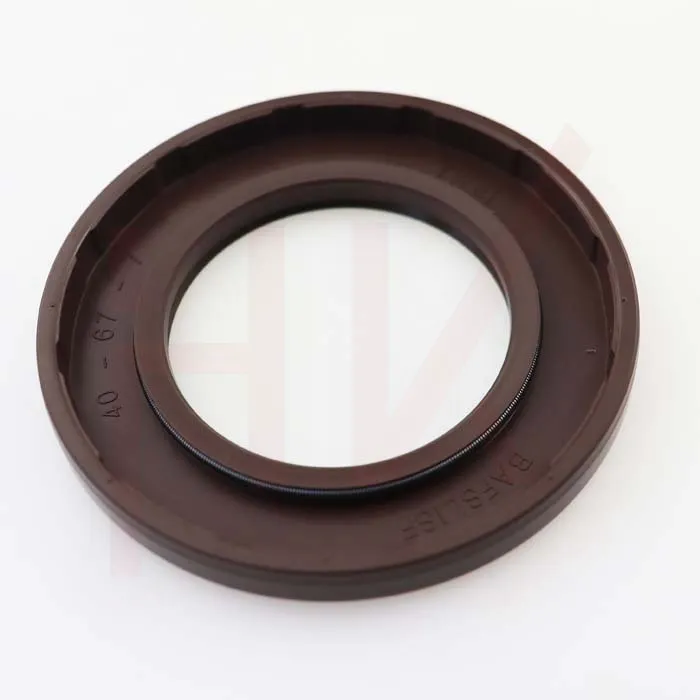
Understanding the intricate design and function of a hydraulic press seal kit requires delving into its composition. Typically, a seal kit includes various seals, gaskets, and O-rings designed to prevent leaks, ensure smooth motion, and maintain pressure levels within hydraulic equipment. These elements might seem minor, but they play a crucial role in maintaining the integrity of hydraulic systems. A fully functional seal kit ensures that hydraulic fluids do not leak out, which is essential for sustaining the power and efficiency of a hydraulic press.
One of the notable features of hydraulic press seal kits is their manufacturing from high-quality materials such as Nitrile Rubber (NBR), Fluoroelastomer (FKM), and Polyurethane (PU). Each of these materials has unique properties that cater to different industrial requirements. For instance, NBR is highly resistant to oil, making it suitable for heavy-duty hydraulic applications. On the other hand, FKM is used predominantly in environments exposed to high temperatures and corrosive substances due to its superior chemical resistance.
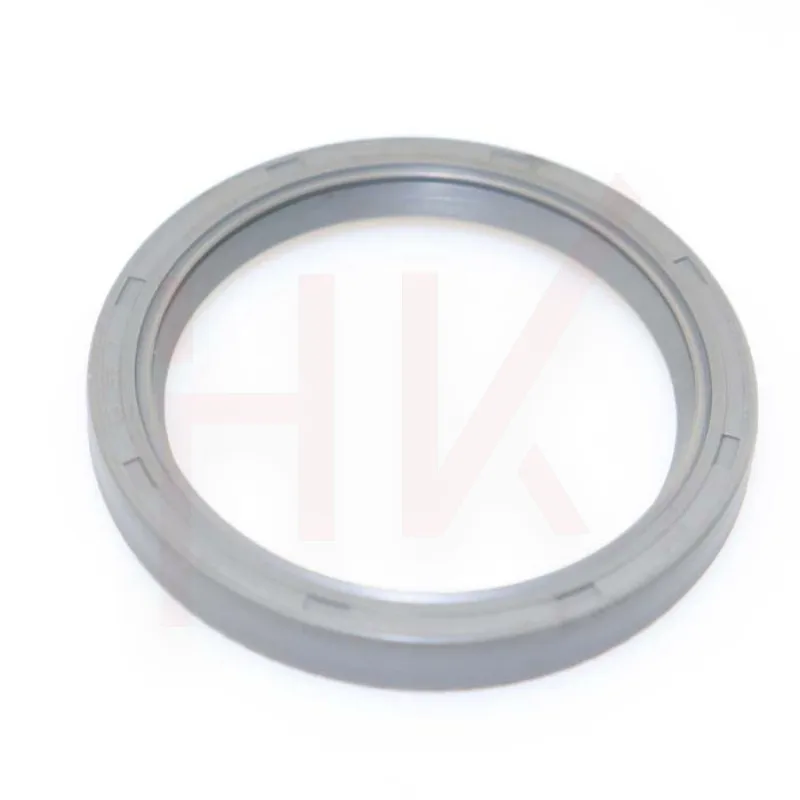
When selecting a hydraulic press seal kit, professionals consider several critical factors. The compatibility of the seal material with the hydraulic fluid is paramount. This compatibility ensures that the seal will not degrade over time, leading to potential system failures. Additionally, the operating pressure and temperature range of the hydraulic system play a pivotal role in determining the most suitable seal kit. An adept understanding of these factors is essential for industries looking to enhance their machinery's performance and reduce downtime.
hydraulic press seal kit
Professional maintenance of hydraulic equipment often hinges on the timely replacement of seal kits. Over time, the wear and tear from constant pressure and motion can deteriorate seals, leading to leaks and inefficiencies. Experts recommend regular inspection and maintenance schedules to identify and replace worn-out seals promptly. Implementing such routines not only extends the lifespan of the machinery but also ensures safe operation, preventing potential workplace hazards due to system malfunctions.
One of the primary advantages of using premium hydraulic press seal kits is their contribution to operational efficiency. High-quality seals reduce friction and wear between moving parts, leading to lower energy consumption and enhanced machinery output. This efficiency directly translates to cost savings for businesses, as machinery operates optimally with minimal breakdowns or repairs required. Moreover, using reliable seal kits underscores a company's commitment to machinery care and operational excellence, reinforcing its reputation for quality and dependability.
In practice, the use of hydraulic press seal kits goes beyond mere mechanical utility. They are integral to fostering sustainable industrial practices. By ensuring that machinery operates at peak efficiency, these seal kits help reduce the environmental impact of industrial operations. Lower energy consumption, minimized fluid leaks, and reduced emissions from efficient machinery all contribute to a smaller carbon footprint, aligning industrial operations with global sustainability goals.
In summary, hydraulic press seal kits are indispensable in the realm of hydraulic machinery. Their contribution to maintaining operational integrity, enhancing efficiency, and supporting sustainable practices cannot be overstated. For industries reliant on hydraulic systems, investing in high-quality seal kits is not merely a maintenance task; it is a strategic decision that underpins operational success and long-term sustainability. Choosing the right seal kit translates into smoother operations, cost savings, and a competitive edge in the marketplace. As such, businesses must prioritize the selection and maintenance of these critical components to ensure continued success in an increasingly demanding industrial landscape.