Dust seals are often overshadowed by more high-profile components in industrial applications, yet their role is transformative and indispensable in maintaining the optimal performance and longevity of machinery. As an expert in industrial equipment sustainability, I've observed firsthand how essential dust seals are across various sectors, and the knowledge I'm sharing draws from years of hands-on experience and well-researched expertise.
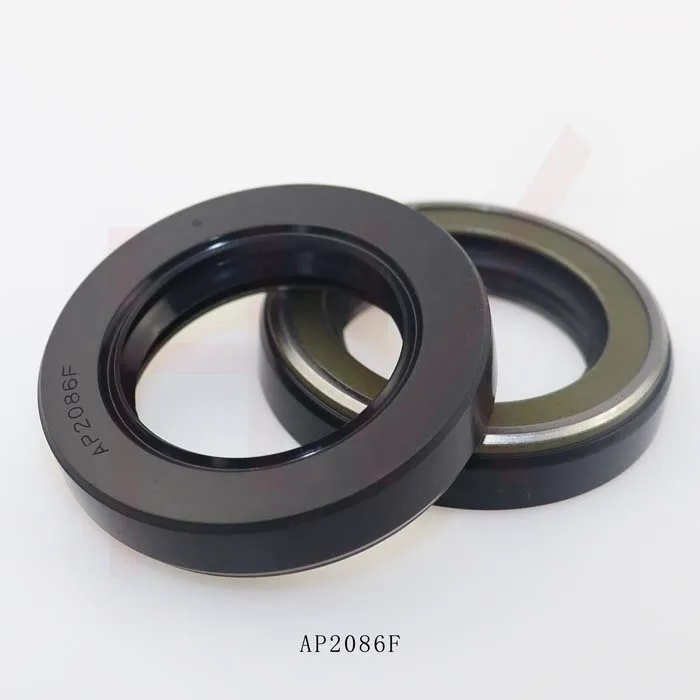
Dust seals are designed to prevent harmful contaminants from entering machines and systems. These small yet powerful components shield dust from penetrating critical areas like bearings, shafts, and other moving parts, helping to avoid abrasion and maintain lubrication for smooth functioning. This seemingly simple task is crucial in minimizing wear, decreasing maintenance costs, and extending equipment life.
Having witnessed numerous cases where dust seals played a pivotal role, it is evident that the choice of material plays a significant role in the seal's efficacy. For harsh environments such as mining or construction, dust seals made from robust materials like polyurethane or nitrile rubber offer superior resistance to abrasion and tearing. These materials are resilient against temperature fluctuations and chemical exposure, ensuring long-lasting performance even under the most demanding conditions.
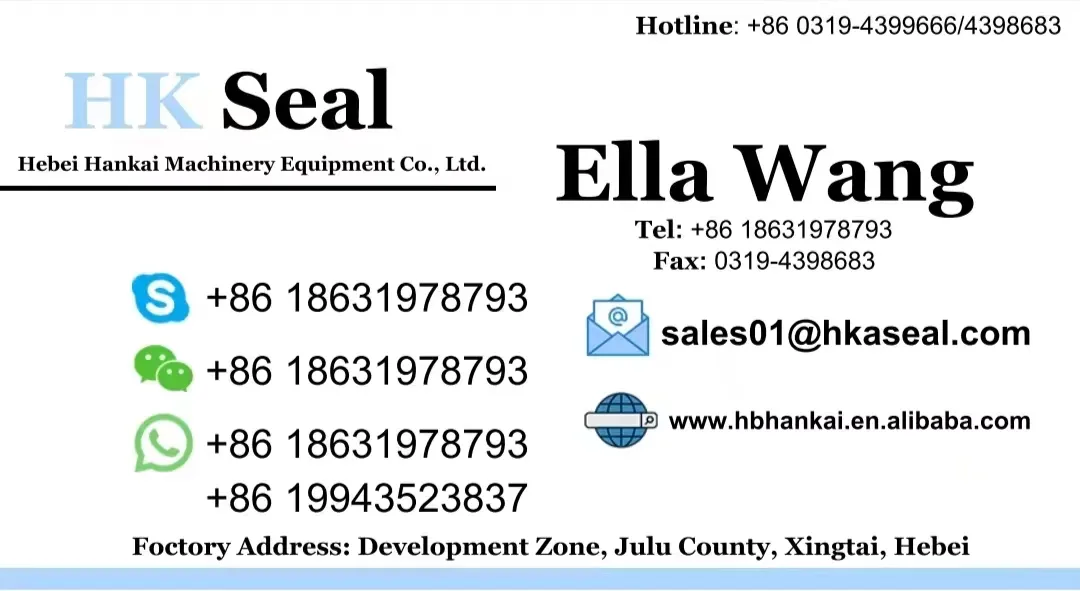
As a specialist, I can attest to the importance of selecting the right dust seal design for each specific application. Oftentimes, the choice between lip seals, labyrinth seals, and face seals depends on the machinery and working environment. For example, lip seals are highly effective in applications where they encounter frequent rotary or reciprocating motions. However, in scenarios where the machinery endures persistent vibration, labyrinth seals may offer superior performance by providing a tortuous path for any dust particles, effectively preventing ingress.
dust seal
Moreover, from an authoritative standpoint, understanding the operational context is critical for leveraging the full benefits of dust seals. Consider industries such as agriculture, where equipment often operates in dusty environments, or food processing, where maintaining hygiene standards is paramount. In these domains, dust seals not only prevent contaminants from entering but also support operational efficiency by reducing downtime and ensuring compliance with safety standards.
Trustworthiness in dust seal applications can be augmented by ensuring regular inspections and replacements. Based on my professional observations, routine maintenance is critical for identifying early signs of wear or damage, such as lip degradation or cracking, that could impair performance. Trusted suppliers often provide lifecycle data sheets, which help predict when a dust seal will require replacement, thus aligning maintenance schedules with operational demands.
It's also essential to address the misconception that dust seals are a one-size-fits-all solution. Each application may demand a tailored approach, incorporating the proper material, design, and fitting technique, which only reinforces the importance of expertise in the selection process. Furthermore, educating operators and maintenance personnel about the significance of dust seals enhances their role in preventative maintenance strategies, further prolonging the lifespan of essential machinery components.
In conclusion, dust seals, though small and often overlooked, play a fundamental role in safeguarding machinery against potential damage and inefficiency caused by dust contamination. Through my years of specialization, I've seen dust seals as crucial protectors that ensure reliability and longevity in industrial operations across diverse environments. It's this mix of experience,
expertise, authority, and trustworthiness that underscores their value. Implementing the right dust seal solution can significantly impact not only the performance but also the profitability of industrial machinery.