In the intricate world of machinery and automotive design, the oil seal plays a critical role, ensuring efficiency, longevity, and overall performance. Despite being a small component, its function is crucial, as it not only contains lubricants but also acts as a barrier against harmful contaminants. Let’s delve into the intricacies of oil seals and explore their paramount importance across various industries.
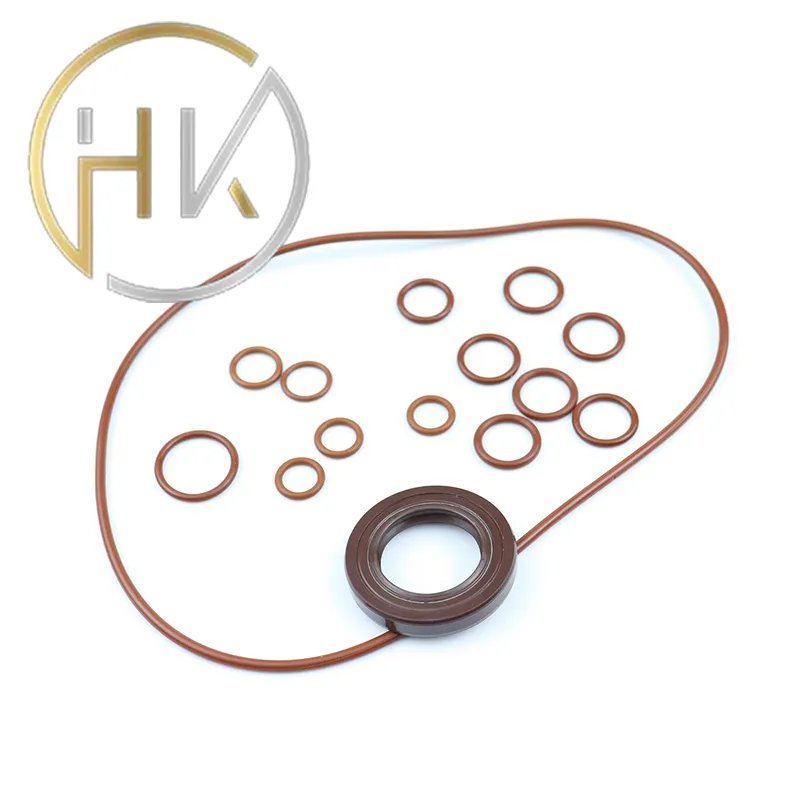
At the heart of any rotating shaft, the oil seal performs a dual function. Primarily, it retains lubricants within the system, preventing any leakage that could compromise mechanical performance. A well-maintained oil seal ensures that lubrication reaches all moving parts, reducing friction and wear, thereby enhancing the lifespan of the machinery. Often made from materials such as rubber, silicone, or other elastomers, oil seals are designed to withstand extreme conditions and resist wear over time. However, their true expertise is revealed in their ability to adapt to varying pressures, temperatures, and rotational speeds, maintaining a tight seal without hindrance.
Equally essential is the oil seal’s capacity to exclude external contaminants. In industrial and automotive settings, dirt, dust, and moisture are omnipresent threats. Once these elements penetrate the system, they can lead to catastrophic failures by damaging bearings and other critical components. An oil seal acts authoritatively as the first line of defense, mitigating the risks posed by environmental factors. In essence, this small yet robust component preserves the integrity of the internal operating environment, establishing a trustworthy shield that keeps the system running smoothly.
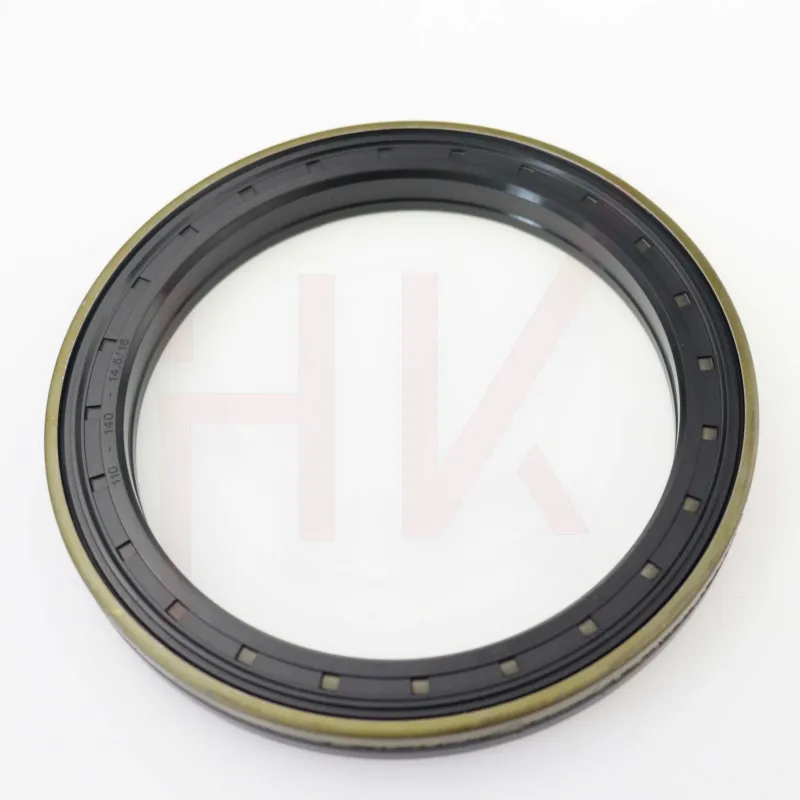
In modern engineering, oil seals are recognized for their authoritative design principles, driven by a blend of empirical knowledge and cutting-edge technology. Engineers must consider numerous parameters, including shaft speed, fluid type, temperature range, and pressure conditions, to design a seal that meets specific needs. The use of advanced computer modeling and simulation tools has further enhanced the ability of engineers to predict seal performance under variable conditions, leading to continuous improvements in seal reliability and efficiency. This expertise ensures that the oil seal not only meets industry standards but also insulates systems against future challenges.
what is the function of oil seal
The application of oil seals spans across multiple domains, from the automotive industry to aerospace, manufacturing, and beyond. In vehicular applications, for instance, oil seals can be found in engines, transmissions, and wheel hubs, playing a pivotal role in maintaining operational integrity. Similarly, in the manufacturing sector, oil seals are used in gearboxes, pumps, and compressors, where they ensure that operations proceed without interruption. The versatility of oil seals underscores their invaluable contribution to diverse industries, highlighting their universal trustworthiness.
Oil seals are constantly evolving, incorporating advanced materials and innovative designs to stay ahead in the competitive landscape. Modern oil seals are often manufactured using composite materials that enhance their durability and extend their lifecycle, even under extreme conditions. Innovations such as labyrinth seals, lip seals, and mechanical seals have further diversified options available to engineers, offering more tailored solutions based on specific operational requirements. This continuous innovation speaks volumes about the industry's commitment to excellence, ensuring that oil seals continue to outperform expectations with each iteration.
To ensure an oil seal operates at its best, proper installation and maintenance are indispensable. Experienced technicians play a crucial role in this process, applying their knowledge to inspect, clean, and fit oil seals with precision. Factors such as shaft condition, housing bore dimensions, and surface finish are meticulously checked to avoid seal failures. Routine inspections are implemented as part of a broader maintenance strategy to detect early signs of wear or damage, preventing potential downtime and costly repairs. Such proactive measures build a reliable and trustworthy maintenance protocol, safeguarding the machinery and extending the service life of both the seals and the equipment they protect.
Conclusively, the oil seal exemplifies a product that combines expertise, authority, and trustworthiness to deliver unrivaled performance in complex systems. Understanding its function not only highlights its significance in today's technologically driven world but also reinforces the importance of ongoing innovation and diligent maintenance practices. The multifaceted role of oil seals in protecting assets and optimizing operations cannot be overstated, as they are fundamental to enhancing the reliability and efficiency of myriad mechanical systems.