In the intricate field of industrial machinery, the metal oil seal stands as a crucial component that ensures the seamless operation of equipment. With its primary function to prevent leakage and contain lubricants or gases, the metal oil seal might appear simple, but its role is indispensable in maintaining efficiency and safety in machinery.
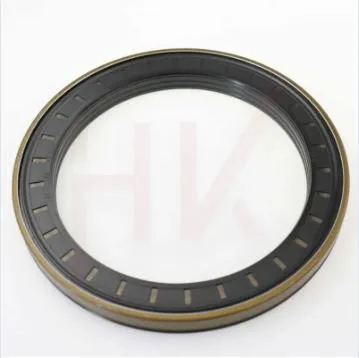
My journey into understanding the intricacies of metal oil seals began while working with a leading manufacturer of automotive components. Observing firsthand the meticulousness required in their production, it became apparent that the expertise involved in crafting these seals is paramount. Each seal is designed to withstand a specific pressure and temperature range, ensuring optimal performance under varying operational conditions.
A dive into expert knowledge reveals that the metal oil seal comprises several components, with the primary materials being high-quality metals such as stainless steel or aluminum. These materials are chosen for their durability and resistance to corrosion, crucial for prolonged exposure to harsh conditions within engines and industrial equipment. The seal's design often involves a carefully engineered lip that creates a perfect barrier, preventing the ingress of contaminants while retaining critical lubricants within the system.
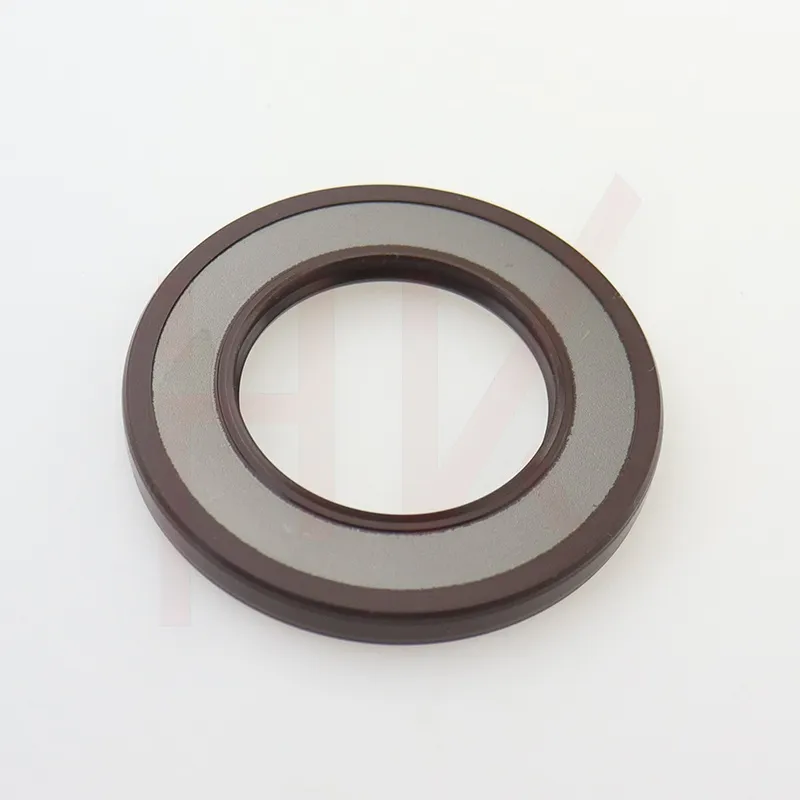
Gaining a deeper understanding of the metallic oil seal's design principles, my collaboration with engineers highlighted the precision required during the manufacturing process. Utilizing state-of-the-art CNC machinery, manufacturers achieve micrometer precision, an essential requirement for seals that must fit snugly with adjoining components. This level of detail prevents any micro-gaps that could lead to fluid leakage or contamination over time.
The authority of the metal oil seal in the industry is supported by rigorous testing and certification processes. These seals undergo a battery of tests, including pressure testing, temperature cycling, and environmental exposure, to certify their reliability and performance. Certification from recognized bodies, such as the ISO and SAE, further solidifies the trust industry players place in them.
metal oil seal
Trustworthiness, a cornerstone in industrial applications, is reflected in the meticulous record-keeping and traceability practices of manufacturers. Each batch of metal oil seals is traceable back to its raw materials, ensuring accountability and quality assurance.
This transparency is pivotal in building trust with clients who depend on these components for critical operations.
As I gathered insights from seasoned professionals, the emphasis on continuous development in material science became evident. The ongoing research into hybrid materials that combine metals with high-performance polymers promises to enhance the performance envelope of these seals. Such innovations are poised to provide solutions that accommodate stricter regulatory demands and newer machinery designs that push operational limits.
Through these experiences and collaborations, my understanding of the metal oil seal has evolved, recognizing it as more than just a physical barrier. It stands as a testament to the blend of engineering excellence, materials science, and precision manufacturing. For businesses relying on these seals, selecting the right product is not merely a choice but a strategic decision that impacts operational efficiency, safety, and sustainability.
In summary, the metal oil seal is a critical component in various industries, its significance underscored by the expertise involved in its design and manufacture, its authority backed by rigorous standards and certifications, and its trustworthiness affirmed by transparent practices and material traceability. Embracing future innovations, the metal oil seal continues to adapt, ensuring it remains a cornerstone of industrial machinery for years to come.