High pressure lip seals have become an indispensable component in industries where maintaining fluid integrity under elevated pressure is crucial. These sophisticated devices are not merely rubber or polymer rings; they are engineered components capable of withstanding relentless pressure demands while ensuring operational ideality. Understanding the nuances of these seals offers profound insights into their application, innovation, and integration into various industrial domains.

At the core of high pressure lip seal functionality is their unique design, which typically incorporates a flexible lip that presses against a rotating shaft. This configuration ensures an airtight interface, even in high-turbulence environments. The material composition of these seals has evolved, integrating composites capable of withstanding extreme temperatures and pressures. Industries such as aerospace, automotive, and oil & gas rely heavily on these seals, particularly because of their precision and efficiency in preventing leakage of lubricating materials or hydraulic fluids.
A pivotal advantage of high pressure lip seals is their ability to enhance the longevity of mechanical systems. They achieve this by minimizing lubricant degradation and preventing the ingress of contaminants into critical system components. Companies investing in robust seal technology often experience reduced maintenance costs and prolonged equipment life. Expert hands within these industries continually assess seal materials, like fluoroelastomers and PTFE, for their durability and adaptability to varying pressure specifications.
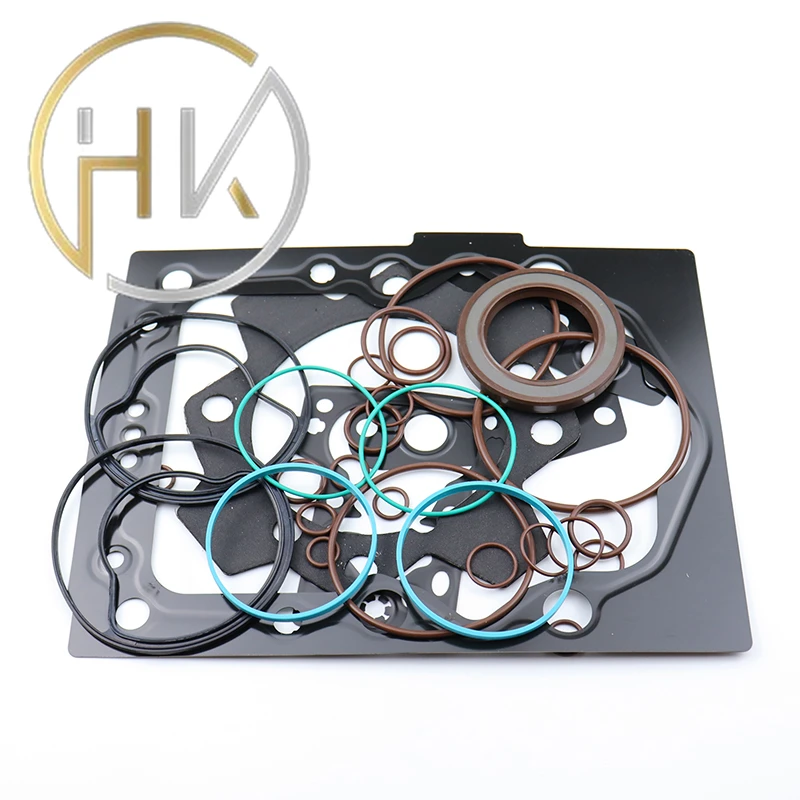
Moreover, the technological innovation surrounding these seals has been remarkable. Engineers are continually pushing the boundaries of seal design through computational fluid dynamics simulations and experimental validations. These advanced methodologies help in anticipating potential seal failures and optimizing design before the manufacturing phase. This predictive approach not only saves time and resources but also elevates the trustworthiness of the products in high-stakes applications.
high pressure lip seal
Authoritative manufacturers of high pressure lip seals often back their products with extensive research and development.
They conduct rigorous testing in simulated real-world conditions to ensure reliability and performance consistency. Customers seeking seals for critical applications should look for suppliers with proven track records and certifications that affirm their commitment to quality standards.
Within industry circles, having actual experience with high pressure lip seals is invaluable. Professionals emphasize the importance of understanding seal dynamics and the interaction between the seal materials and the fluids they are tasked to contain. Experience also breeds insights into installation techniques, the influence of pressure gradients, and the impact of fluctuating temperatures on seal performance.
The trustworthiness of high pressure lip seals is further solidified through transparent communication from manufacturers. Clear guidelines on installation, maintenance, and lifecycle management ensure that end users can implement best practices and optimize seal performance. Such detailed customer support fortifies user confidence in the longevity and dependability of these products.
In conclusion, high pressure lip seals represent a critical convergence of engineering expertise, material science, and reliability. Their application spans crucial sectors where precision and dependability are non-negotiable. As technology progresses, the continuous enhancement of these seals will likely lead to more sophisticated solutions, fortifying their position as the linchpin of fluid integrity in high-pressure environments. For enterprises aiming to bolster their operational efficiency through reliable sealing technologies, integrating high pressure lip seals remains a definitive strategy.