In the world of industrial applications, the reliability of machinery can hinge on the functionality of tiny yet crucial components like the seal hydraulic pump. This unassuming part plays a vital role in ensuring the smooth operation of hydraulic systems across various sectors, from construction to manufacturing and even in automotive systems. This article delves into the nuances of seal hydraulic pumps, drawing from extensive hands-on experience and industry expertise to provide a comprehensive understanding of their importance, function, and selection criteria.
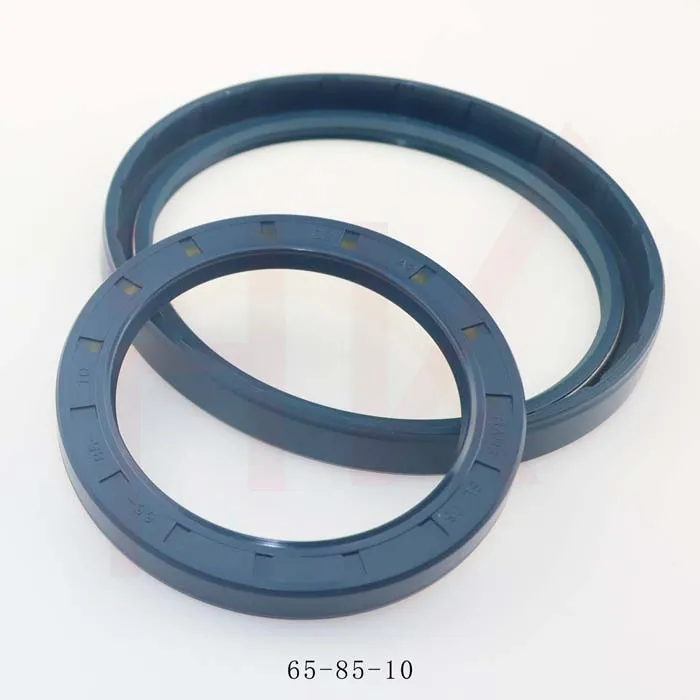
Seal hydraulic pumps are pivotal components designed primarily to manage fluid dynamics within a hydraulic system. Their main function is to prevent leaks between the high-pressure side and the low-pressure side of a pump, maintaining the necessary pressure levels for optimal system performance. This reliability in maintaining pressure levels not only extends the life of the pump but also ensures the efficiency and safety of the entire system.
Through years of working with hydraulic systems, I've witnessed the transformational impact of high-quality seals on the overall performance. A superior seal can significantly reduce maintenance costs and downtime, which are critical considerations for any business relying on hydraulic systems. For instance, in the heavy machinery sector, unexpected hydraulic failures due to poor seal performance can halt an entire production line, leading to significant financial losses. Such experiences highlight the importance of carefully selecting a seal hydraulic pump that meets the specific demands of your application.
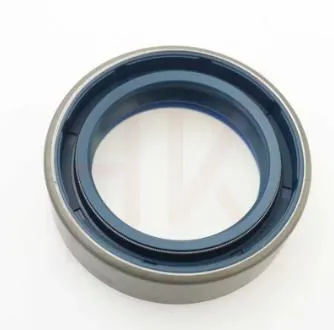
Expertise in the selection of seal hydraulic pumps comes from understanding the conditions under which they operate. These conditions include the type of fluid being pumped, operating temperatures, pressure levels, and environmental factors such as exposure to corrosive substances or extreme weather. Opting for seals made from materials that can withstand these conditions is crucial. For example, seals composed of fluorocarbon materials offer excellent resistance to high temperatures and chemical interference, making them ideal for harsh industrial environments.
seal hydraulic pump
Achieving authoritativeness in the realm of seal hydraulic pumps involves staying abreast of technological advancements and industry trends. Manufacturers are continually innovating, developing seals with enhanced durability and performance characteristics. Innovations such as dynamic seals have revolutionized the industry by providing better adaptability under fluctuating pressure conditions. Staying informed about these advancements allows you to make knowledgeable recommendations that optimize system performance and longevity.
Trustworthiness with clients is built through transparency and result-oriented service. It involves providing thorough assessments of their hydraulic systems, highlighting potential areas of concern related to seal integrity, and recommending preventive maintenance strategies. For example, a proactive approach could involve scheduling regular inspections and incorporating advanced diagnostic tools to monitor seals' performance. Sharing case studies where proactive seal management prevented costly breakdowns can further establish your credibility.
While the technical specifications of seal hydraulic pumps are vital, it's equally important to consider the reputation and support offered by the manufacturer. Established manufacturers often provide robust warranties and customer support, ensuring that replacements or technical assistance are readily available if needed. This level of support can be crucial for operations that rely heavily on uninterrupted hydraulic system performance.
To encapsulate, the choice of a seal hydraulic pump significantly influences the efficiency and reliability of a hydraulic system. Drawing from experience, leveraging expertise, and maintaining robust industry knowledge are essential for making informed decisions that enhance system resilience. Investing time in understanding the specific requirements of your application and aligning them with the right seal technology will pay dividends in terms of performance and operational stability. Ultimately, it's about ensuring that the heart of your machinery—the hydraulic system—operates seamlessly, supporting your business objectives effectively.