The rotary shaft seal, often underestimated, plays a pivotal role in a wide array of machinery applications. A marvel of engineering, these seals are crafted with precision, blending expertise, and innovation to ensure equipment operates seamlessly. From hydraulic systems to automotive engines, the functionality and reliability of these seals can make all the difference in performance.
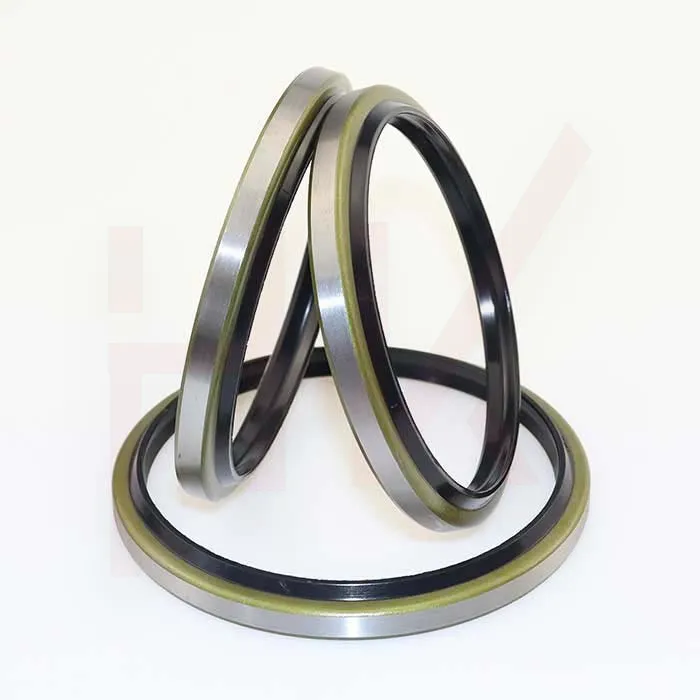
One cannot discuss rotary shaft seals without acknowledging their exceptional ability to prevent leakage of lubricants as well as contaminants intrusion. Their design, inherently sophisticated, ensures that the delicate balance between pressure and rotational speed is maintained. What makes these seals indispensably effective is the material composition and design intricacies tailored to meet diverse industrial needs.
Material selection for rotary shaft seals is an area where expertise significantly influences outcomes. Various materials like nitrile rubber, fluorocarbon, and silicone are deployed depending on the operational environment. Nitrile rubber, favored for its oil resistance properties, handles moderate temperatures effectively. On the other hand, fluorocarbon seals offer superior resistance to high temperatures and aggressive chemicals, supporting applications demanding extreme conditions. Understanding these material characteristics is vital, influencing durability and efficiency.
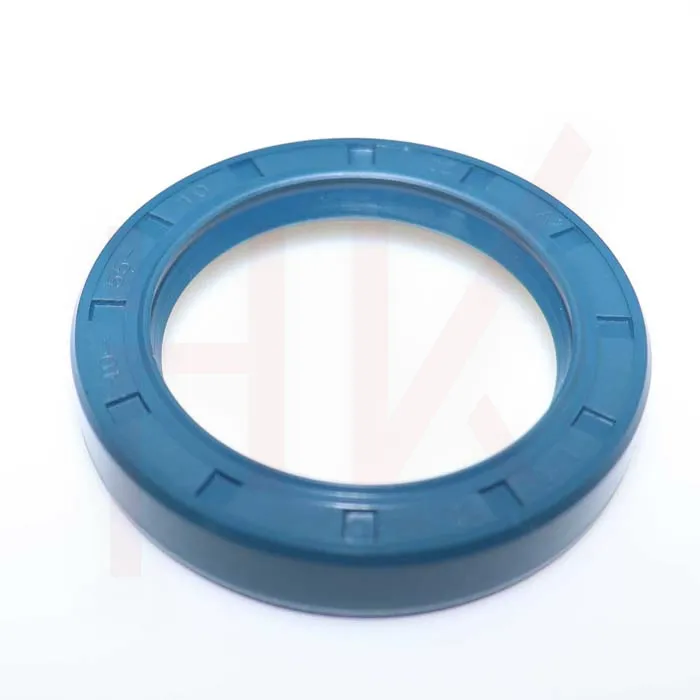
Expertise in the engineering of rotary shaft seals extends beyond materials. The processing decisions, including lip design and spring loading, bear a substantial impact. A single-lip seal might suffice for general purposes, but more intricate applications necessitate dual or even triple-lip designs to safeguard against contaminant ingress and egress leakage.
This layered protection underscores the adaptability of seals in varying contexts. Seasoned engineers consider these variables meticulously, ensuring that each seal performs optimally under its designated conditions.
rotary shaft seal
Authoritativeness in the field of rotary shaft seals comes with a commitment to quality and tested performance. Leading manufacturers submit their seals to rigorous testing protocols that replicate real-world scenarios, assessing them against parameters such as pressure endurance, thermal expansion, and friction management. The adherence to global standards enhances credibility, promoting Trustworthiness in an industry where failure is not an option. A reputation for robust testing processes assures end-users of reliability and longevity, two key metrics in assessing the true value of rotary shaft seals.
Trustworthiness is amplified through transparent engagement with clients and end-users. Leading experts in this domain understand the importance of customer feedback, utilizing it to refine production approaches continually. Technical support teams work closely with clients, guiding them in seal selection suitable for specific applications while addressing queries that influence purchasing decisions. This open channel of communication inspires confidence and, in turn, loyalty, fostering a culture where trust is reciprocated and valued.
In conclusion, the rotary shaft seal is emblematic of engineering brilliance, embodying a synergy of expertise, trust, and authority. For industries reliant on pinnacle performance and durability, these seals offer unparalleled assurance. When crafted and implemented with precision, they not only fulfill their primary function but also contribute to overall system efficiency and reliability. As industries continue to evolve, so too will the technology and expertise surrounding rotary shaft seals, a testament to their enduring relevance in a dynamic industrial landscape.