Hydraulic pumps are the lifeline of numerous industrial systems, driving essential processes with precision and efficiency. Among the various components that ensure these pumps operate flawlessly, seals play an indispensable role. For those familiar with the intricacies of hydraulic systems, understanding seal functionality and their impact on pump performance is crucial.
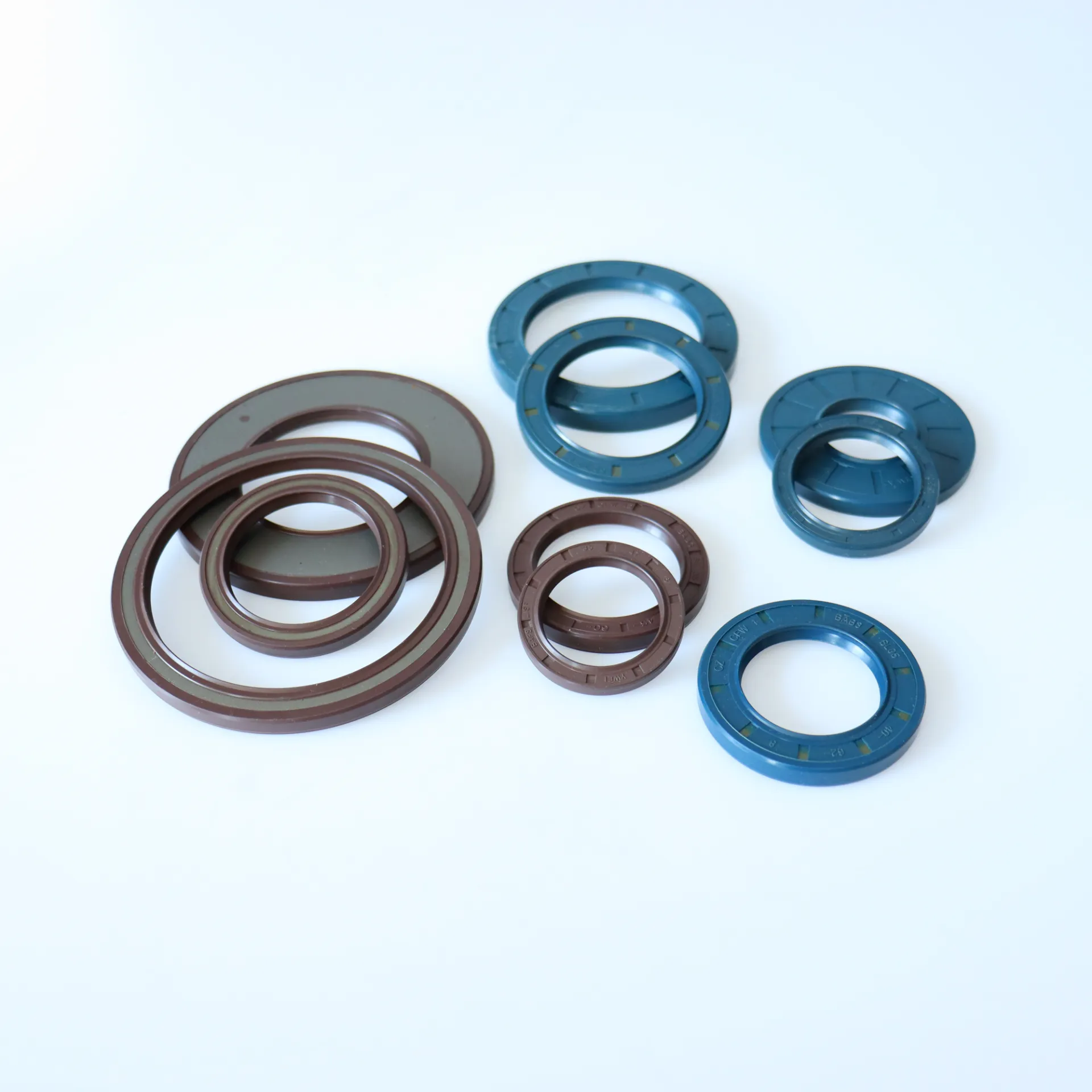
The Importance of Seals in Hydraulic Pumps
Seals in hydraulic pumps are not just peripheral components; they are pivotal in maintaining system integrity and efficiency. Their primary function is to prevent fluid leakage, which is critical in sustaining pressure and enabling the hydraulic system to function correctly. Without effective seals, the efficiency of the pump declines, leading to increased wear and tear and potential system failures. Thus,
seals are essential for extending the life of hydraulic pumps and ensuring optimal performance.
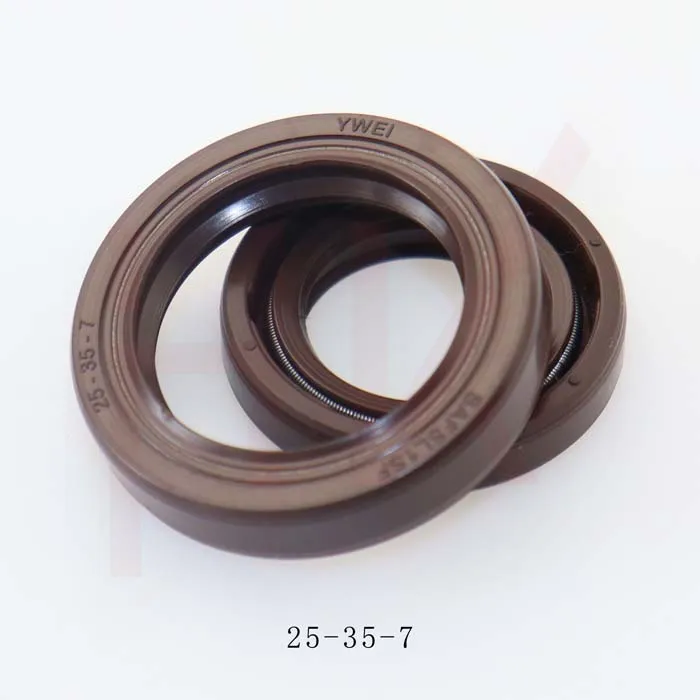
Types of Seals Used in Hydraulic Pumps
Hydraulic pump seals can be categorized based on their design and materials. The selection of seals can significantly impact the pump's overall performance. Common types include
1. O-ring Seals These are the most frequently used seals due to their simple design and reliable performance. They're ideal for static and dynamic applications and provide excellent resistance to high pressures.
2. Lip Seals Known for their versatility, lip seals are used in applications where there's relative motion between the components. They're adept at keeping contaminants out and preventing leakage.
3. Piston Seals Used within the pump's cylinder, piston seals ensure that the hydraulic fluid remains contained inside the cylinder, facilitating smooth motion.
4. Rod Seals Positioned around the rod of hydraulic cylinders, rod seals prevent fluid from leaking into the outside environment, safeguarding against contamination and ensuring efficient performance.
Material Considerations
seal hydraulic pump
The effectiveness of seals in a hydraulic pump also hinges on the material from which they are made. Choosing the right material can mean the difference between a seal that lasts for years and one that fails prematurely. Rubber and thermoplastic elastomers are popular due to their flexibility and resistance to wear. Meanwhile, polyurethane seals are favored for their robustness and excellent resistance to extrusion. It's crucial to select materials that can withstand the specific demands of different hydraulic systems, including temperature fluctuations, exposure to chemicals, and varying pressure levels.
Installation and Maintenance
While selecting the right seal is vital, proper installation and regular maintenance are equally important. A common mistake is neglecting the importance of proper seal seating during installation, which can lead to premature failure. Experts recommend ensuring that the shaft and bore are free from contaminants and damage before installation. Lubrication during the process can also aid in ensuring a snug fit and optimal performance.
Routine maintenance checks should include seal inspections to identify any early signs of wear, such as cracks or deformations. Timely replacement of worn seals can prevent more significant damage to the hydraulic pump, thereby avoiding costly downtime and repairs.
Industry Applications of Hydraulic Pump Seals
Hydraulic pumps, equipped with appropriate seals, are indispensable across various industries. In the construction sector, they're vital for operating machinery like excavators and loaders. The agricultural industry relies heavily on these pumps for equipment such as tractors and harvesters. They're also critical in manufacturing and automotive sectors, where precision and reliability are paramount. In all these applications, seals ensure that hydraulic systems operate smoothly, efficiently, and safely.
The Future of Hydraulic Pump Seals
Innovation in materials and seal design continues to enhance the performance and longevity of hydraulic pump seals. The industry is witnessing a shift towards more sustainable materials that offer the same, if not better, performance as traditional options. Developments like self-lubricating seals and seals with enhanced resistance to extreme temperatures and chemicals represent the future of hydraulic pump seals. As technology advances, seals will continue to play a pivotal role in hydraulic systems, making them more reliable and efficient.
Conclusion
The humble seal is a cornerstone of hydraulic pump performance, directly affecting the efficiency, safety, and durability of the system. For professionals in industries that depend on hydraulic systems, understanding the role of seals aids in making informed decisions about maintenance and operations, ultimately leading to enhanced productivity and reduced operational costs. Investing in quality seals and maintaining them diligently is a testament to the commitment to excellence in any industrial application.