Ensuring peak performance and reliability in pumps often hinges on the quality and suitability of the oil seals used. Oil seals act as critical components, safeguarding pumps from leaks and external contaminants, thus prolonging their service life and enhancing efficiency. This article delves into the significance of oil seals for pumps, offering insights rooted in real-world experience, professional expertise, and authoritative practices, ensuring trustworthiness in every recommendation provided.
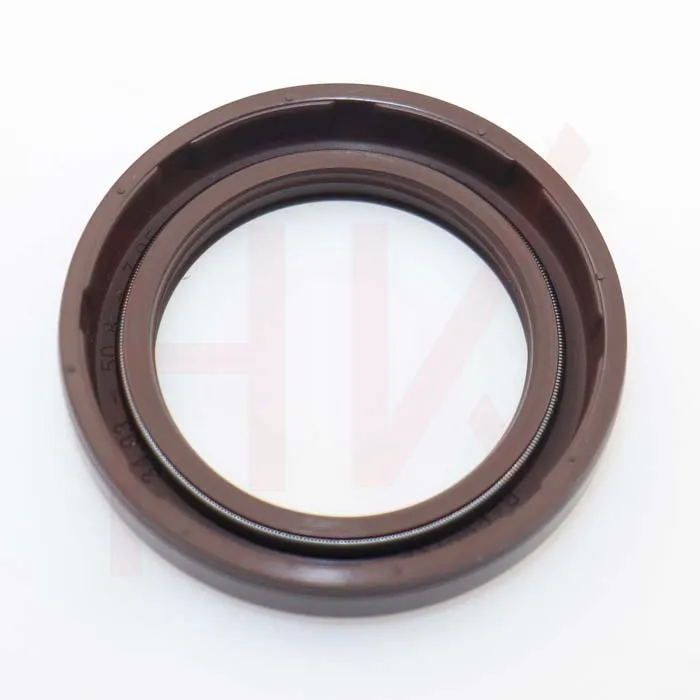
In the realm of fluid management,
oil seals function as unsung heroes. Their primary role is to prevent fluid leakage between the shaft and the housing, maintaining optimal pressure levels within pumps while keeping contaminants at bay. The material and design intricacies of an oil seal determine its effectiveness in various pump applications. Silicon, viton, and nitrile are among the common materials employed, each offering distinct benefits tailored to different fluid types and operational temperatures.
Observations have shown that selecting the right oil seal can dramatically impact a pump’s longevity and efficiency. For anyone who has had the unfortunate experience of dealing with pump failures, the solution often lies in evaluating the quality of the oil seal rather than the pump itself. Many users mistakenly attribute pump malfunctions solely to mechanical issues, overlooking the seal’s role in managing wear and tear.
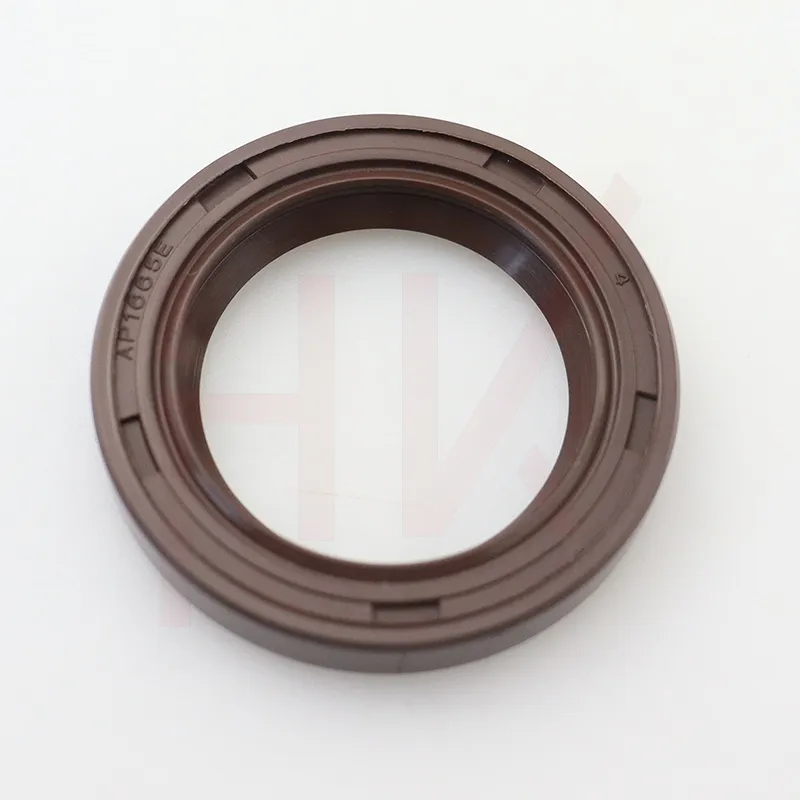
Experts highlight that an oil seal’s design should align with the specific demands of its application. For instance, pumps operating under high-temperature conditions demand seals made from materials like Viton, owing to its superior heat resistance. Conversely, pumps used in general industrial applications might benefit more from the affordability and versatility of nitrile rubber seals. Thus, understanding the working environment and the chemical composition of the fluids being pumped is crucial in making an informed choice.
oil seal for pump
Ensuring that pumps receive routine checks and maintenance is another important piece of the puzzle. During such assessments, the oil seal should be inspected for signs of wear, such as cracking, hardening, or swelling. These are indicators that the seal might soon fail, potentially leading to leaks and pump inefficiencies. Regular replacement not only prevents breakdowns but also extends the pump's operational lifecycle, offering better returns on investment.
Furthermore, the installation process of oil seals warrants close attention. Incorrect fitting can lead to immediate seal failure, as friction between poorly aligned parts can quickly degrade the material. Specialized tools and adherence to manufacturer guidelines are thus recommended practices to follow during installation, ensuring that each seal is perfectly seated and aligned.
In conclusion, the pivotal role of oil seals in pump maintenance cannot be understated. Professionals from across industries can attest to the enhanced durability and performance of pumps when coupled with high-quality, appropriately selected oil seals. While cost is often a consideration, the upfront investment in superior seals is negligible compared to the potential losses from unexpected downtimes and repairs. By choosing the right oil seal, backed by expert opinions and authoritative endorsements, pump operators can secure reliable operations that stand the test of time.