Oil seals, often referred to as shaft seals or rotary seals, play an indispensable role in modern machinery, ensuring the efficient and prolonged operation of various equipment. These devices are designed to prevent the leakage of lubricants and to keep contaminants at bay, preserving the integrity of the machinery they protect. When selecting an oil seal, several factors can heavily influence its performance, making it essential to choose the right one for your specific application.
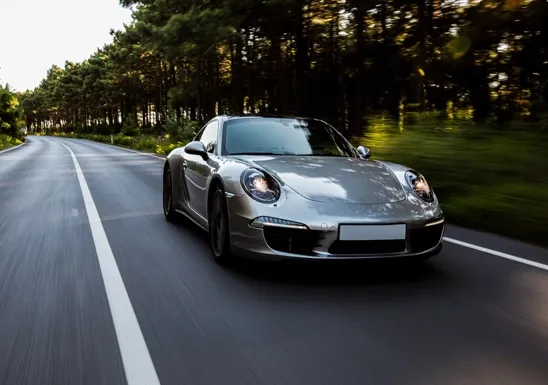
The first and foremost consideration is the material of the oil seal. Nitrile rubber (NBR) is a commonly used material, known for its excellent resistance to oils and operating temperatures from -40°C to 120°C. For more demanding environments, materials such as fluorocarbon (Viton) and silicone offer enhanced temperature resistance and chemical stability. Silicone, with its broad temperature range and flexibility, is often preferred in extreme temperature conditions, while Viton excels in chemical resistance, making it ideal for automotive and industrial applications.
Another critical factor is understanding the type of contaminants your machinery might be exposed to. For example, in farming equipment, where seals might be subject to dirt and moisture, having double lip oil seals provides an extra layer of protection against external contaminants. This ensures the lubricant remains clean, reducing wear and tear and extending the machinery's operational life.
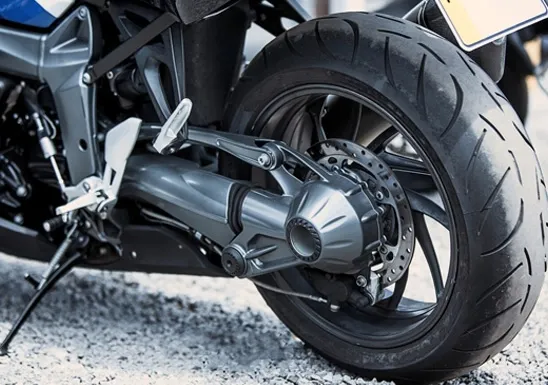
Installation of oil seals demands attention to detail and expertise. Improper installation can lead to premature failure,
causing costly repairs and downtime. It is crucial to ensure shafts are smooth, and any surface roughness is addressed to avoid seal damage. Furthermore, aligning the seal correctly and using the appropriate installation tools prevents distortion or misalignment, enhancing the seal's efficiency.
oil seal
Operational pressures and shaft speeds also dictate the type of oil seal required. High-pressure applications necessitate seals designed to withstand increased stress without compromising their structural integrity. PTFE seals, for instance, are known for their exceptional performance under high pressures and speeds, offering superior durability and reliability.
Regular maintenance and inspections of oil seals are paramount to maintaining operational efficiency. Periodically checking for wear or damage can prevent unforeseen failures and costly downtime. It is advisable to replace seals at the first sign of wear to avoid compromising the machinery's productivity.
Choosing the right oil seal extends beyond the immediate performance; it contributes significantly to the overall lifecycle and efficiency of the equipment. By selecting the appropriate material, ensuring correct installation, and maintaining regular inspections, businesses can optimize the performance and reliability of their machinery, proving invaluable in a competitive industry.
For industrial engineers and maintenance professionals, understanding the nuances of oil seal technology is not just a matter of operational efficiency but also a critical component of cost management and sustainability. Whether in automotive, aerospace, or heavy machinery sectors, the right oil seal can make a significant difference in reducing maintenance costs and extending equipment life, making it an essential consideration in the design and maintenance of mechanical systems.