Industrial oil seals play a crucial role in maintaining the longevity and efficiency of machinery across various sectors, from automotive to heavy industrial applications. Their ability to keep lubricants contained while preventing contaminants from entering ensures that machines operate smoothly and effectively. Utilizing high-quality oil seals is paramount for any industrial setup that prioritizes performance and maintenance cost-reduction.
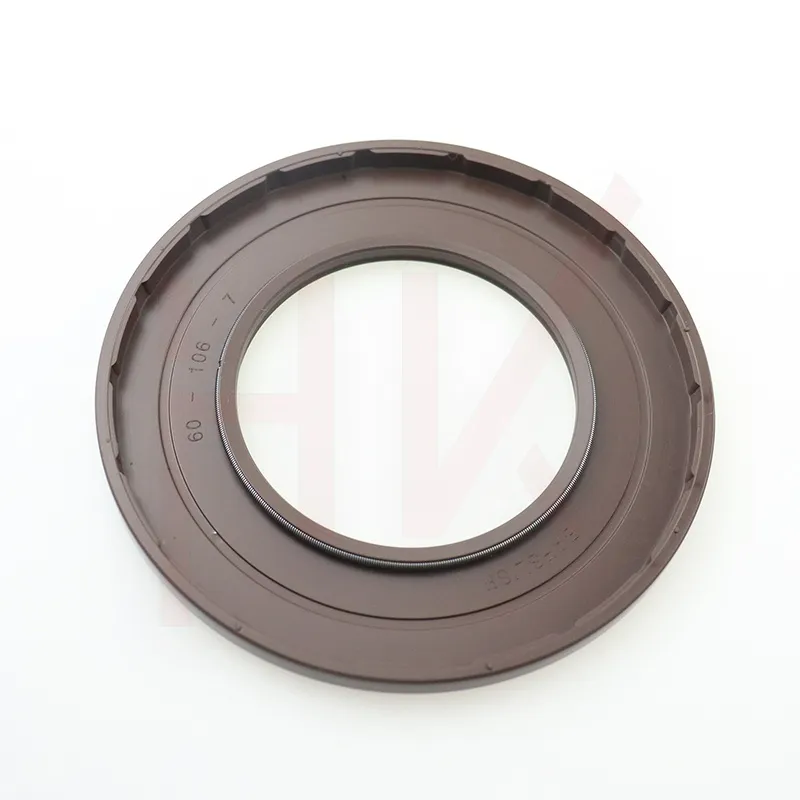
For anyone with years of experience in industrial maintenance,
the significance of oil seals cannot be overstated. Not all seals are created equal, and selecting the right one involves understanding specific requirements and operational environments. Materials such as nitrile rubber, silicone, and fluorocarbon are chosen based on the operational temperatures and chemical resistances required by the machinery. Coupling the right material with the appropriate seal type ensures a tight fit and extended service life, minimizing machinery downtimes and maintenance expenses.
Industry experts often emphasize the importance of understanding the detailed specifications of machinery when selecting industrial oil seals. The seal design must take into account the shaft speed and the amount of pressure exerted within the system. Dynamic applications typically require seals that can endure varying speeds and loads without degrading. For instance, rotary shaft seals are often favored for high-speed applications due to their excellent sealing capabilities and longevity.
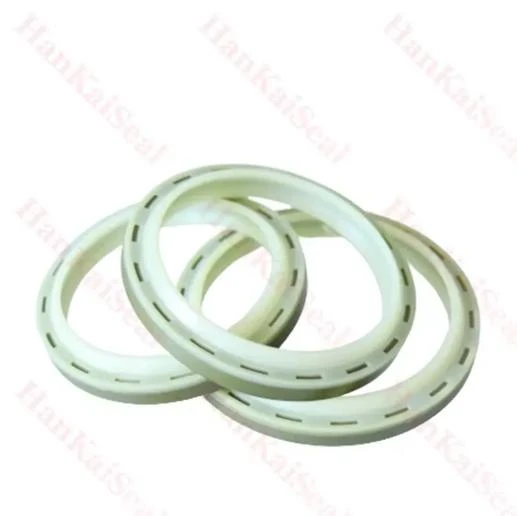
Authoritative sources in the field of industrial machinery maintenance recommend routine checks and correct installation procedures to maximize the effectiveness of oil seals. Incorporating preventative maintenance schedules ensures potential seal failures are identified and addressed before they lead to significant machinery breakdowns. Proper tool usage during installation prevents seal damage, while alignment checks prevent uneven wear—extending the lifespan of both the seal and the machinery it protects.
industrial oil seals
Trustworthiness in manufacturers and suppliers is another critical factor. Leading brands invest in material innovation and testing to provide seals that not only meet but exceed industrial standards. Certification from reputable organizations provides assurance that their products have undergone rigorous evaluations. Choosing products from well-established manufacturers guarantees access to technical support and comprehensive warranties—critical factors in trust-building for companies relying on these seals.
Real-world experiences often highlight the impact of selecting inferior quality seals. Leaks, contamination, and eventual machinery wear often result from cutting corners on seal quality, leading to costly downtime and repairs. On the other hand, investing in top-tier industrial oil seals manifests in tangible improvements in machinery reliability and performance consistency, echoing the advice of seasoned industry professionals.
The continuously evolving landscape of industrial technology offers constant improvements in seal materials and designs, enabling machinery to meet higher efficiency and environmental standards. Keeping abreast of the latest developments ensures industries leverage the best available products for their specific needs. Engaging with the latest industry studies and training programs is essential for professionals maintaining machinery at peak performance.
Investments in high-quality industrial oil seals pay dividends in the form of increased machinery lifespan, improved operational efficiency, and reduced maintenance costs. Quality seals are an indispensable component of any industrial operation committed to reliability and performance.