Double lip seals have emerged as a pivotal component in various industrial applications, offering enhanced sealing performance and reliability. These seals are designed with two lips that provide a dual barrier against the ingress of contaminants and the egress of lubricants, which is essential for maintaining the integrity and performance of machinery and equipment.

In industrial settings, double lip seals are celebrated for their expertise in managing harsh environments. From automotive engines to industrial pumps, these seals are employed to prevent dirt, dust, and moisture from entering critical components. This prevention is crucial as the infiltration of contaminants can lead to premature wear, corrosion, and ultimately, equipment failure. The dual-lip design ensures that even if one lip is compromised, the other continues to provide a barrier, thereby extending the service life of the machinery.
The trustworthiness of double lip seals is evident from their widespread adoption in industries that demand high standards of reliability and durability. For instance, in the automotive sector, these seals are utilized in wheel bearings and differential assemblies where they confront constant exposure to road contaminants and varying temperatures. Their ability to maintain performance under such conditions speaks volumes of their reliability.
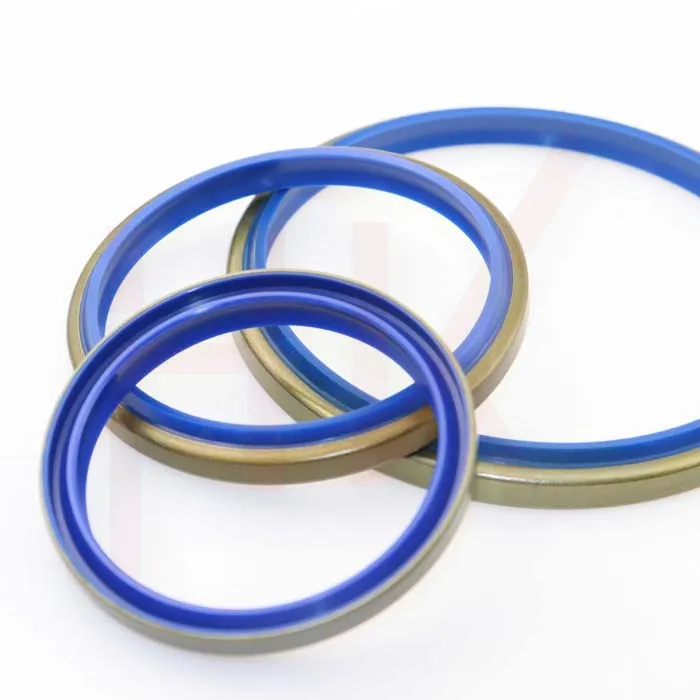
From an expertise standpoint, the engineering behind double lip seals involves careful material selection and precision manufacturing. Typically, these seals are made from high-grade elastomers or thermoplastics that can withstand significant temperature fluctuations, chemical exposures, and mechanical stresses. The inner lip is primarily responsible for holding lubricants within the assembly, ensuring smooth operation, while the outer lip acts as a primary barrier against environmental elements.
double lip seal
Authoritativeness in the field of sealing technology is often corroborated through rigorous testing and certification.
Double lip seals are tested for their endurance, tensile strength, and resistance to wear and tear by regulatory and industry bodies. Certifications from these authorities provide assurance to users about the quality and performance of the seals they employ.
Real-world experience underlines the importance of selecting the right type of double lip seal for specific applications. In heavy machinery environments, users have noted significant improvements in operational uptime after switching to double lip seals. The enhanced protection offered by the dual barrier system reduces maintenance needs and operational downtime, leading to increased productivity and cost savings.
For anyone considering the incorporation of double lip seals into their operations, it is crucial to collaborate with reputable suppliers. Suppliers with extensive experience in the field are better equipped to provide seals that meet specific application demands. They can offer guidance on the appropriate material and design specifications based on the operational environment and performance requirements.
In conclusion, the integration of double lip seals into industrial applications is a testament to their superior sealing capability and dependability. As industries continue to push for levels of efficiency and reliability, double lip seals will play a crucial role in ensuring machines and equipment operate seamlessly. By leveraging expert advice and relying on certified products, businesses can achieve significant gains in maintenance efficiency and operational longevity.